— 11 min read
11 Tips for Effective Construction Site Management
Last Updated Jul 10, 2025
Taylor Riso
Contributing Writer
87 articles
Taylor Riso is a marketing professional with more than 10 years of experience in the construction industry. Skilled in content development and marketing strategies, she leverages her diverse experience to help professionals in the built environment. She currently resides in Portland, Oregon.
Jacob Kunken
Solutions Engineer, Heavy Civil
26 articles
Jake Kunken currently works as Solutions Engineer for Procore's Heavy Civil division. He brings 14 years of experience working in various construction roles in New York and Colorado, including laborer, assistant carpenter, carpenter, assistant superintendent, superintendent, construction manager, safety manager, and project manager. Jake also spent time in EHS as an environmental engineer for Skanska. He’s worked on more than 40 commercial projects from ground-up, to heavy civil, hospital work, and tenant improvement. Jake studied Ecological Technology Design at the University of Maryland.
Last Updated Jul 10, 2025
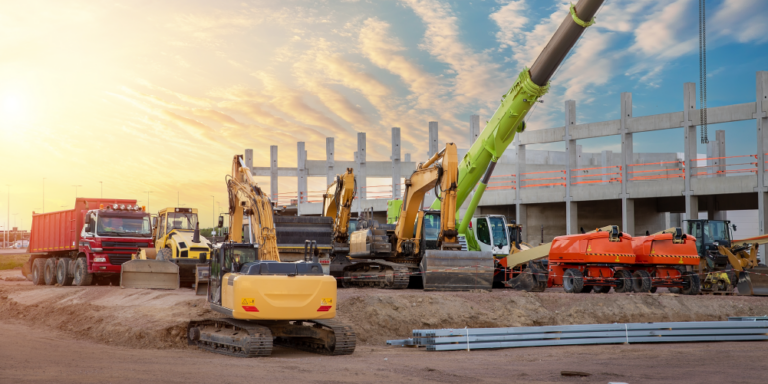
Construction site management is the process of orchestrating, supervising, and harmonizing the moving parts, including all activities, resources, and parties, involved in executing a construction project at a specific physical location. It serves as the backbone of the successful execution of construction projects.
Construction site management is multifaceted: At its core, it demands a mix of technical knowledge, leadership skills, communication abilities, and a thorough understanding of project management principles. Although construction site management takes place at the physical construction site itself, the process actually begins during the preconstruction phase. A proficient preconstruction process paves the way for streamlined construction site management by providing a well-defined roadmap, mitigating potential risks, and ensuring a clear understanding of project goals among stakeholders.
Implementing construction site management best practices ensures that projects are completed on time, within budget, and aligned with quality and safety standards. In this article, we will explore key best practices for contractors to utilize for construction site management to achieve the best possible results.
Table of contents
1. Keep safety a top priority.
Due to the industry’s higher potential for accidents and fatalities compared to other professions, safety is of paramount concern in construction site management. It plays a critical role in ensuring the well-being of workers and visitors, minimizing accidents, and maintaining a productive and compliant work environment. Construction sites inherently involve various hazards, ranging from heavy machinery operation to working at heights, and effective safety management is essential to mitigate these risks.
Commitment from leadership
Owners and organizational leaders must place safety at the forefront of their company culture. By ingraining adherence to safety regulations and accident prevention into daily communication and work routines, every member becomes actively involved and invested in fostering a safer operational environment.
It's essential to recognize that the efficacy of any safety program relies on the continuous delivery of consistent messaging and ongoing interaction with employees.
Comprehensive site safety plan
Developing a site-specific safety plan helps the contractor communicate and outline safety procedures for different work tasks and emergencies. These plans should be readily accessible to all workers, subcontractors, visitors and relevant stakeholders.
Ongoing education and training
Offer continuing safety education and training to keep workers informed of the most current safety protocols and regulations. Furthermore, mandate specialized training as needed based on the particular scope of work, tasks, or site-specific challenges to ensure the safe execution of activities on that particular project.
Consistent inspections
Safety inspections on jobsites are essential to systematically identify potential hazards, evaluate safety measures' effectiveness, and ensure adherence to safety regulations.
2. Understand site constraints — and opportunities.
Considering site-specific factors is key to effective construction site management. Every construction project is defined by a unique set of goals and parameters and the site conditions can play a significant role in determining project success. A thorough site analysis in the initial project planning phase is essential to identify and address both challenges and opportunities.
Site accessibility, which encompasses the ability of construction personnel, equipment, and materials to move to and from the site, greatly impacts project efficiency. Challenging site access can hinder project progress, cause schedule delays and increase costs.
When formulating the plan for construction execution, the contractor accounts for the site’s egress, local traffic conditions, ensuring adjacent safe pedestrian and public pathways, the scheduling of material deliveries, emergency access and adherence to applicable regulations. Prior to kicking off construction, the contractor also evaluates the site’s terrain, topography and soil conditions. The physical characteristics of the land — such as slopes, uneven terrain, or rocky ground, as well as the soil composition — affect construction methods, foundation design and excavation processes.
3. Foster a healthy jobsite culture.
Jobsite culture is the collective values, attitudes, behaviors and communication patterns of the individuals working on a construction project. Project leadership molds jobsite culture and subsequently imparts it to all those onsite, including workers and subcontractors. Maintaining a positive jobsite morale fosters open communication and effective collaboration among different trades, subcontractors and project stakeholders. Approaching the project as one team creates a culture that encourages problem-solving and continuous improvement, resulting in the development of creative solutions and innovative approaches to challenges that arise during construction.
Prioritizing the development and reinforcement of positive jobsite culture that aligns with the project's goals and values is a key piece to effective construction site management and ultimately fosters an environment where all workers can thrive and contribute to the project's success.
4. Map out the sequence of tasks.
Sequencing plays a pivotal role in defining the project workflow. It entails arranging tasks and activities in a strategic sequence to attain project goals with efficiency. This is of utmost importance because certain tasks may depend on the completion of others or have specific prerequisites. Once a clear sequence of tasks is established, a detailed project plan that outlines the specifics of each task, resource allocation, timelines, and milestones can be created.
Collaborate with internal project team members and specialty contractors to ensure that project timelines are feasible and account for any potential delays. It’s important to avoid overloading team members with unrealistic deadlines, as it can lead to burnout and compromised quality.
Once the sequencing order has been determined, it's crucial to communicate this information effectively to specialized contractor partners. Ensuring that everyone is on the same page regarding the order and timeline of tasks and activities helps confirm their availability and prevents any misunderstandings later on in the project.
As the project progresses, continuously review and update the project plan to accommodate evolving circumstances or conditions. This enables the team to respond to changes, tackle challenges, and ensure that the plan remains relevant. Typically, this process often involves reallocating resources such as manpower, materials, and equipment to align with the critical path forward.
5. Strategically select subcontractor partners.
Strategically selecting subcontractor partners is a key aspect of construction site management that has a significant influence on the project’s success. Subcontractors play a crucial role in executing specialized scopes of work, and their performance can impact project quality, timelines, and overall outcomes. General contractors frequently compile a roster of pre-qualified speciality contractors to choose from. During the prequalification stage, the general contractor assesses specialty contractors using criteria such as their past performance, safety rating, experience, references and financial stability.
A general contractor should consider the project's parameters and goals when selecting a subcontractor. For example, if sustainability and efficiency is important to the project owner, the general contractor should prioritize selecting subcontractors who possess expertise aligned with these aspects within their scope of work. Investing time and effort in choosing reliable, capable, and compatible subcontractor partners can lead to smoother project execution, enhanced project outcomes, and improved client satisfaction.
6. Document everything.
Documenting in construction site management is essential for maintaining transparency, accountability, and effective project execution. Construction projects involve numerous stakeholders, complex processes, and potential risks. Proper documentation helps capture critical information, facilitate communication, and provide a historical record of project activities.
When tasks, responsibilities, and timelines are documented, it becomes easier to hold individuals and teams accountable for their agreed-upon contributions. This helps avoid finger-pointing and facilitates problem-solving if issues arise.
Construction projects also often must adhere to regulatory standards and permits. Proper documentation helps demonstrate compliance with applicable laws and regulations. In addition, properly documented information can serve as evidence and support legal claims or defenses in case of conflicts or legal challenges. This encompasses aspects like delineating the contract's inclusions and exclusions, specifying the mutually agreed-upon scope of work, outlining procedures for handling change orders, addressing payment and invoicing, and establishing standards for quality control.
7. Incorporate rigorous quality management procedures.
Implementing effective quality control and quality assurance practices is essential for ensuring that construction projects meet the required standards and deliver high-quality outcomes. The first step of quality management is clearly defining standards. Establishing clear and detailed quality standards for each aspect of the project, including materials, workmanship, and final deliverables, creates alignment between all stakeholders on project outcomes. Regularly conducting inspections and quality tests at various stages of the project helps to identify and address potential issues early, minimizing cost and schedule impacts as the work progresses.
A comprehensive plan to quality oversight reduces rework, improves the final product, boosts client satisfaction and enhances a contractor’s reputation. A track record of projects executed with precision and minimal issues due to effective quality management also builds trust and credibility, solidifying a contractor’s positioning in the market.
Build a Strong Foundation with our Preconstruction Course
With 20+ years of experience, Ben Ashburn teaches you how to streamline planning, bidding, and procurement for better outcomes.
Master preconstruction, elevate your project planning
Expand your preconstruction knowledge with our comprehensive preconstruction course.
Enroll in the courseMaster preconstruction, elevate your project planning
Expand your preconstruction knowledge with our comprehensive preconstruction course, and discover how Procore's platform can streamline and enhance your project workflows.
Enroll in the courseRequest a demo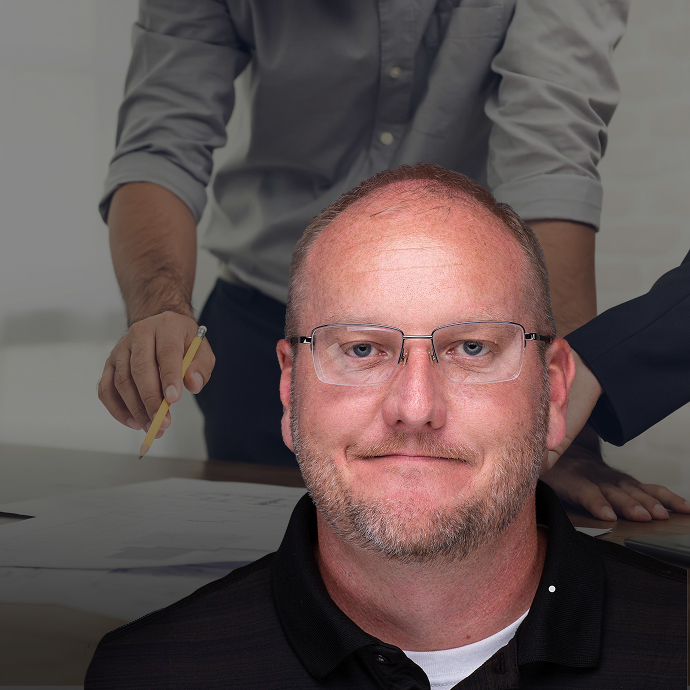
8. Prioritize open and clear communication.
Effective communication is a cornerstone of successful construction project management. Emphasizing clear, open, and respectful communication can enhance collaboration, minimize misunderstandings and contribute to the overall success of construction projects. Establishing reliable communication tools and methods, such as regular team meetings, email updates, and dedicated communication software or platforms, ensures that all project stakeholders know how and when to communicate any updates, issues, and progress.
Leadership that encourages transparency where team members feel comfortable sharing progress updates, concerns, and suggestions further fosters trust and collaboration. This supports project teams proactively addressing risks or challenges that arise as opposed to merely responding to them after they develop.
9. Embrace technology.
The recent integration of technology in the construction industry enhances efficiency, accuracy, communication, collaboration, and overall project outcomes. Construction management software and tools aid in planning, scheduling, collaboration, budgeting and reporting. These platforms also provide a centralized platform for storing project documents, plans, contracts, and communications, enabling easy access and organization for all stakeholders.
The use of Building Information Modeling (BIM) enhances project visualization and coordination. BIM creates a digital model that contains detailed information about the physical components, geometry, materials, and spatial relationships in a project. It serves as a shared knowledge resource for all stakeholders throughout the project lifecycle.
BIM also enables clash detection, a process that identifies conflicts among different building elements or trades before construction commences. Clash detection, previously referred to as a coordinated set of drawings, is an ask between the mechanical, electrical, and plumbing (MEP) trades before installing materials in a structure’s plenum space.
This proactive approach mitigates the need for expensive modifications during the construction phase. For instance, consider an area within a building where multiple systems converge—a mechanical duct intersects with a structural beam and electrical conduit. In the absence of coordination, these systems might clash, leading to cost overruns, project delays, and potential safety risks during construction. By utilizing BIM's clash detection, it becomes evident that the mechanical duct intersects with a structural beam and electrical conduit. Consequently, specialty contractors collaborate to alter the duct's pathway or adjust the placement of the beam and conduit, all prior to the commencement of work on-site.
In addition, mobile devices and apps now enable real-time communication and information sharing among members of on-site teams. They facilitate instant updates, photo sharing, progress tracking, and issue reporting directly from the field.
These platforms are also now cloud-based, offering secure storage and accessibility of project data from anywhere, fostering collaboration and communication between all project parties.
10. Incorporate lessons learned from past projects.
Learning from past experiences is a fundamental aspect of effective construction site management. It involves reflecting on past projects, identifying successes and challenges, and applying those lessons to improve and streamline future projects.
By analyzing past projects, contractors can pinpoint areas where processes, strategies, or communication could have been more efficient. Implementing improvements based on these insights enhances overall project performance. Contractors are able to gain an understanding of how resources were allocated on previous projects, which contributes to improved planning and optimization in terms of labor, materials, equipment, and budget considerations.
11. Create a project closeout checklist.
Project closeout is the final phase of construction site management that ensures the completion and successful handover of the project to the client.
This process encompasses various elements including:
- Gather necessary documentation: Compile and organize all project documentation, including drawings, operation and maintenance (O&M) manuals, warranties, permits, and inspection reports for handover to the client.
- Address the punch list: Identify and resolve any outstanding issues, defects, or deficiencies in the punch list before final handover. Work with subcontractor partners to ensure all items are resolved satisfactorily, adhering to predetermined quality benchmarks.
- Perform the final inspections: Conduct thorough final inspections to verify that all work aligns with quality standards and regulatory requirements.
- Walk the client through the final space: Offer the client a tour of the final space to ensure they’re satisfied and address any questions or concerns they may have.
Effective construction site management stands as the foundation of successful project execution. By meticulously planning, coordinating resources, fostering communication, and adopting innovative strategies and tools, contractors can navigate the complexities of construction with precision. As the industry continues to evolve, embracing new technologies and methodologies while valuing safety, continuous improvement, and collaboration will undoubtedly continue to shape the future landscape of construction site management.
Was this article helpful?
Thank you for your submission.
100%
0%
You voted that this article was . Was this a mistake? If so, change your vote here.
Scroll less, learn more about construction.
Subscribe to The Blueprint, Procore’s construction newsletter, to get content from industry experts delivered straight to your inbox.
By clicking this button, you agree to our Privacy Notice and Terms of Service.
Thank you!
You’re signed up to receive The Blueprint newsletter from Procore. You can unsubscribe at any time.
Categories:
Written by
Taylor Riso
Contributing Writer
87 articles
Taylor Riso is a marketing professional with more than 10 years of experience in the construction industry. Skilled in content development and marketing strategies, she leverages her diverse experience to help professionals in the built environment. She currently resides in Portland, Oregon.
View profileJacob Kunken
Solutions Engineer, Heavy Civil | Procore
26 articles
Jake Kunken currently works as Solutions Engineer for Procore's Heavy Civil division. He brings 14 years of experience working in various construction roles in New York and Colorado, including laborer, assistant carpenter, carpenter, assistant superintendent, superintendent, construction manager, safety manager, and project manager. Jake also spent time in EHS as an environmental engineer for Skanska. He’s worked on more than 40 commercial projects from ground-up, to heavy civil, hospital work, and tenant improvement. Jake studied Ecological Technology Design at the University of Maryland.
View profileExplore more helpful resources
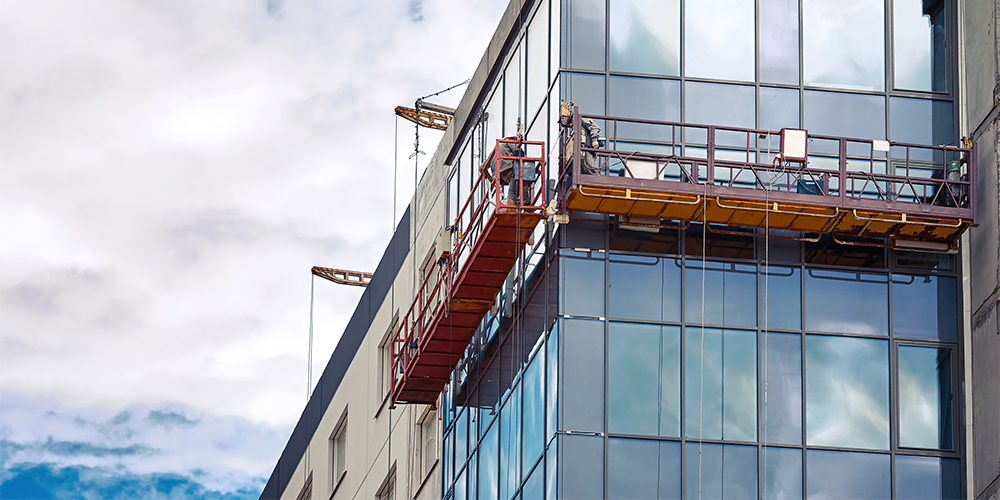
Preparing for Post-Construction: A Guide to the Final Phase of a Project
Large construction projects often take years to plan, more years to design, and even more years to build. From the groundbreak point of view, it’s often difficult to see the...

A Guide to Construction Commissioning
During project closeout, an owner wants to receive any documents, training and warranties needed to take over the management and maintenance of their building. But they also want assurance that...
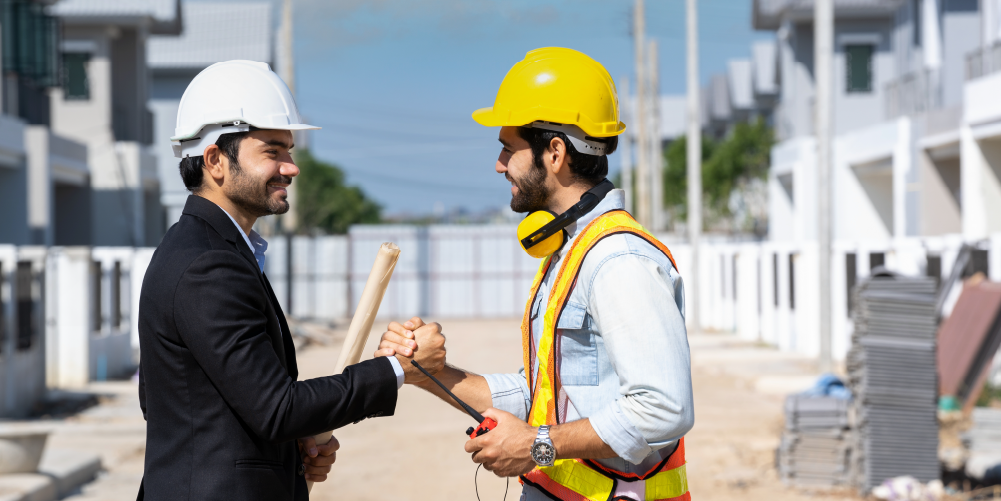
Construction Handover: Keys to an Efficient Process
After the months or years it takes to complete a construction project, the handover process begins. Project handover is the final part of the construction process, where a project, along...

Construction Closeout Documents: What’s Included & Why
Few parts of the building process can feel as stressful and as complicated as closeout: the multi-step, final phase of construction in which a project is prepared to be handed...
Free Tools
Calculators
Use our calculators to estimate the cost of construction materials for your next project.
Templates
Find a template to help you with your construction project tasks.
Material Price Tracker
Get the latest U.S. retail prices and view historical trends for common building materials.
Glossary
Explore key terms and phrases used in the industry.