— 6 min read
Construction Safety Management: Building a System to Reduce Risk
Last Updated Sep 1, 2024
Clark Jensen
Strategic Product Consultant, Quality & Safety
10 articles
Clark Jensen joined Procore as a Senior Strategic Product Consultant, Quality & Safety where he spearheads product knowledge education and executes product demonstrations. He brings several years of experience in roles both on and offsite as a former senior project safety manager for a general contractor in Salt Lake City, and a senior risk control consultant for a large U.S.-based insurance firm.
Elizabeth Rivelli
Contributing Writer
12 articles
Elizabeth Rivelli is a freelance writer specializing in insurance and finance. Her writing has been featured in dozens of publications, including Investopedia, The Balance, Forbes, Bankrate, NextAdvisor, and Insurance.com. Elizabeth holds a degree in Communication Studies from Northeastern University. She lives in New England.
Last Updated Sep 1, 2024
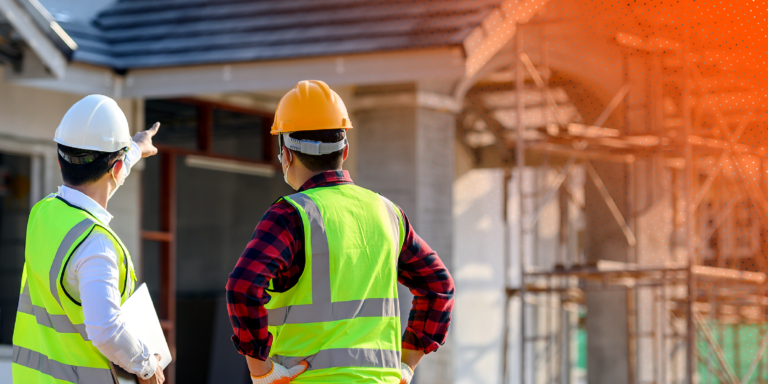
Due to the high-risk nature of construction work, having a comprehensive construction safety management plan is essential. Construction safety management is the formal process that details how safety plans are rolled out within the company. Using a construction SMS can help companies reduce accidents, improve insurability, and increase productivity across teams.
While safety officers play a significant role in creating and executing a safety system, these plans should also be integrated with other company areas. In this article, we’ll take a more detailed look at the benefits of implementing a safety plan, and what construction companies should consider when rolling them out.
Table of contents
Goals of safety management
Having a comprehensive safety management plan is important for any construction company, no matter the size of the organization or the type of projects in the hopper. Below are five key benefits from creating a system that company personnel is familiar with.
Reduced accident rates
Identifying potential project hazards and create standard operating procedures (SOPs) to ensure the right safety practices are followed should be part of any company’s safety plan. Performing a job hazard analysis can help mitigate onsite accidents, and inform everyone of the proper steps to take in case an incident occurs.
Higher productivity
An effective safety management plan should unify teams on the company’s safety goals, and ensure everyone is held to the same standards and protocols. Implementing the plan requires communication across teams, both in the field and in the office.
Legal and regulatory compliance
Properly managed safety may help keep construction companies out of legal trouble. Plans should ensure organizations comply with federal, state, and local regulations, including OSHA standards. Following safety procedures outlined in a company’s safety plan may reduce jobsite accidents and hazards and adhere to any local authorities, such as city inspectors or fire departments.
Improved insurability
When an insurance company analyzes a company’s risk, safety procedures, plans and programs that are in place may determine the organization’s experience modification rating (EMR). Implementing a comprehensive construction safety management program, may improve a company’s insurability and potentially, lower premiums.
Worker satisfaction
Working in construction can be very risky. If workers feel unsafe on the jobsite, it could impact employee retention. Creating a robust construction safety program keeps workers safe, but also demonstrates the organization’s commitment to health and safety when all players follow the procedures.
A peer-reviewed study conducted in 2022 found that reducing the perception of health risks among employees can improve job satisfaction and increase buy-in and participation in safety programs and activities.
Courses about construction.
For construction.
Unlock your career potential with our free educational courses on Health & Safety, Data in Construction, and more.
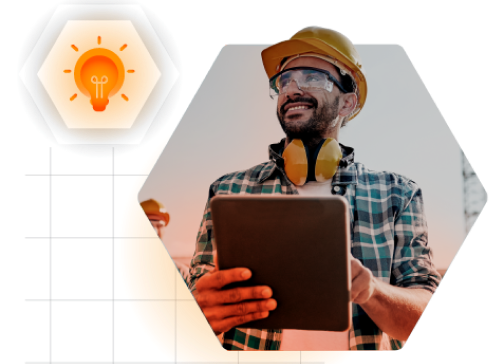
Elements of a successful safety management program
Because safety management plans are comprehensive, several factors must be considered when putting one together. Below are some things that should be included when developing a safety management system.
Employee Buy-in
Whether an existing safety management plan needs improvement, or creating a safety plan from scratch, buy-in is essential for the plan's success. Safety plans should be simple and efficient enough to encourage compliance throughout the entire organization, from executives to onsite workers.
To develop a good construction safety management system, it’s helpful to leverage other individuals and organizations. Contacting an insurance carrier or insurance broker, risk consultants, or industry groups like the Associated General Contractors of America’s (AGC) safety & Health department for insight and feedback when the plan can ensure it is relevant and covers all the bases.
Once the system has been developed, establish a committee of people with varying job titles to review it. It’s important to get input from field staff, like foremen and project managers, who can provide their perspective from the jobsite. Additionally, the committee should review the plan regularly and make changes as needed.
Safety Policy
A company’s safety management plan helps outline the organization’s commitment to safety. Specifically, it defines safety roles and responsibilities for all workers and sets clear expectations for everyone in the company regarding safety practices.
Hazard identification and risk assessment
Hazard identification is an essential part of any safety system. Periodic inspections on job sites for potential risks, such as hazardous materials, faulty equipment, and trip and fall risks should be woven into the company’s safety policy. Each hazard should be identified and evaluated based on its potential to cause accidents.
Safety training and education
Safety education is key for any construction company, and your training protocols should be outlined in your organization’s construction SMS. Trainings should include general safety practices, as well as job-specific safety procedures.
Safety stand-downs, for example, are helpful trainings specific to certain topics. If there is an uptick in trips or falls onsite, the construction safety manager may conduct a standdown to review proper procedures and safety protocols with workers. This should include general safety practices, as well as job-specific safety procedures.
Emergency response plan
Safety procedures should include an organization’s emergency response plan in case of an emergency, natural disaster, or other situation that could put workers in danger. It’s important that onsite personnel are aware of the evacuation processes, contact information for local emergency services, first aid procedures, and who is the safety person to facilitate emergency responses onsite.
Incident investigation
It’s also critical to include directions for properly reporting accidents or near-misses. These incidents need to be investigated to understand what caused them and prevent similar things from happening in the future. The process for reporting incidents, who receives the report, and how changes are implemented following the investigation should also be depicted and clear for employees.
Safety procedures and work practices
Another major construction safety management system component is the company's specific workplace plans for jobsite activities. Make note of the process for enforcing safety procedures and what happens if employees don’t follow the correct standards.
Personal protective equipment (PPE)
Your SMS should have information about the use of PPE on the jobsite. This includes what types of PPE are required for employees in specific scenarios and how workers are trained on proper PPE use. Also, make a note about the company’s PPE procurement practices to ensure that your employees always have properly-fitting PPE.
Communication
Communication is fundamental to any construction safety management system. It’s important to have regular discussions about safety issues, hold safety meetings, use proper safety signage on jobsites, and document safety issues. This keeps safety top of mind for both employees and leadership across the entire organization.
Success measures
Safety goals should also be considered when creating a company’s safety management plan. Safety executives and directors should define the metrics used to measure the safety system’s success and hit safety-related goals. This might involve quarterly or annual reports on the company’s progress towards safety goals, and what system improvements are made overtime to guarantee positive safety outcomes.
Continual improvement
Safety plans will evolve and change overtime. The safety system should include regular audits to ensure everyone follows established safety policies and procedures. These reviews should also check for areas that need improvement based on company policy or new industry regulations. This ensures the system's efficiency — even as safety goals and plans change.
Prioritizing safety helps boost a company's reputation.
Every construction company can benefit from an efficient safety plan. A sound construction safety management system keeps everyone in the organization safe and reduces the risk of workplace accidents. And not only does a safety system keep workers safe, it’s also a smart business move.
Was this article helpful?
Thank you for your submission.
100%
0%
You voted that this article was . Was this a mistake? If so, change your vote here.
Scroll less, learn more about construction.
Subscribe to The Blueprint, Procore’s construction newsletter, to get content from industry experts delivered straight to your inbox.
By clicking this button, you agree to our Privacy Notice and Terms of Service.
Thank you!
You’re signed up to receive The Blueprint newsletter from Procore. You can unsubscribe at any time.
Categories:
Written by
Clark Jensen
Strategic Product Consultant, Quality & Safety | Procore
10 articles
Clark Jensen joined Procore as a Senior Strategic Product Consultant, Quality & Safety where he spearheads product knowledge education and executes product demonstrations. He brings several years of experience in roles both on and offsite as a former senior project safety manager for a general contractor in Salt Lake City, and a senior risk control consultant for a large U.S.-based insurance firm.
View profileElizabeth Rivelli
Contributing Writer
12 articles
Elizabeth Rivelli is a freelance writer specializing in insurance and finance. Her writing has been featured in dozens of publications, including Investopedia, The Balance, Forbes, Bankrate, NextAdvisor, and Insurance.com. Elizabeth holds a degree in Communication Studies from Northeastern University. She lives in New England.
View profileExplore more helpful resources
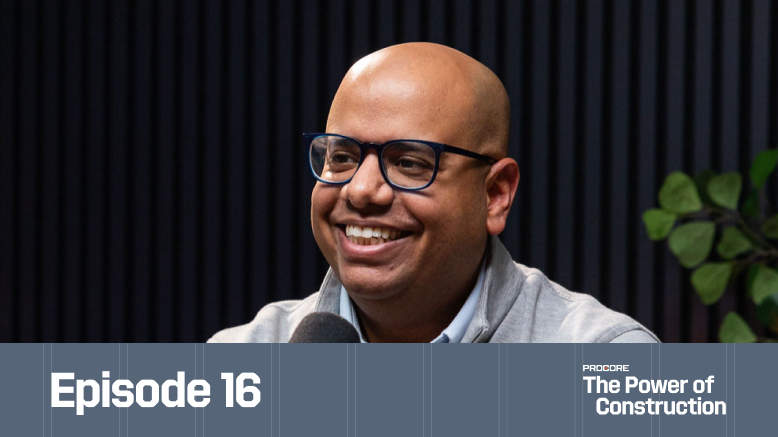
Will AI Replace ‘Paperless Builders’—or Redefine Them?
How can artificial intelligence enhance rather than replace human expertise in construction? In Episode 16, Hamzah Shanbari, Director of Innovation at Haskell and author of “The Paperless Builders,” reveals how...
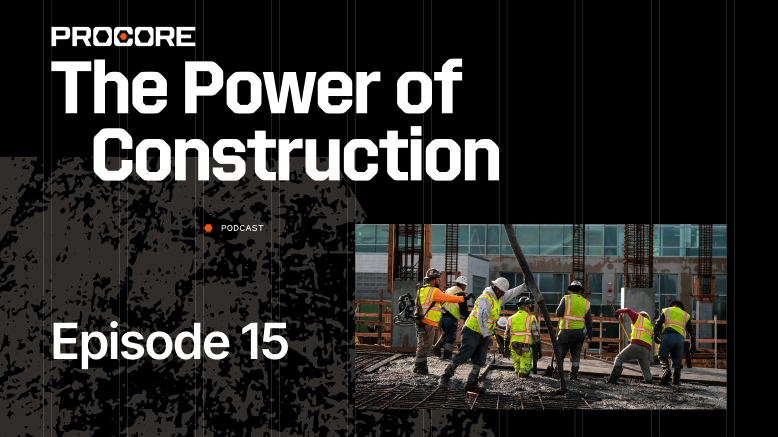
Has Construction Tech Failed its Most Important Customer?
In episode 15 of The Power of Construction, we tackle a provocative question: Has construction technology actually failed building owners? Despite billions in investment, owners report that BIM automation and...
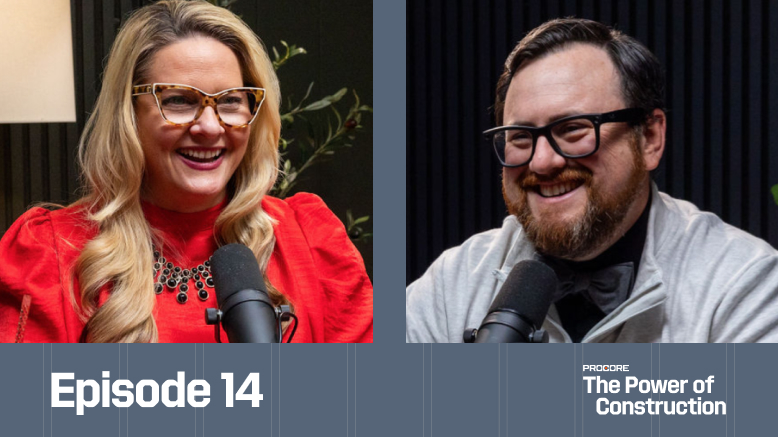
Is Construction Ready for the Future?
In episode 14 of The Power of Construction, we ask a critical question: Can an industry tasked with building our future truly meet the demand to double its growth by...
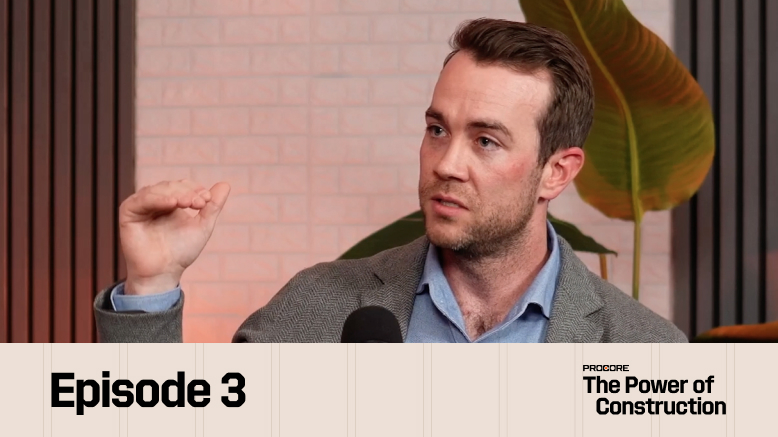
How Can We Bridge the Data Gap in Construction?
In Episode 3 of The Power of Construction, Eric Whobrey, ARCO Murray’s VP of Innovation and Managing Partner joins hosts Sasha Reed and Kris Lengieza to explore the data gap...
Free Tools
Calculators
Use our calculators to estimate the cost of construction materials for your next project.
Templates
Find a template to help you with your construction project tasks.
Material Price Tracker
Get the latest U.S. retail prices and view historical trends for common building materials.
Glossary
Explore key terms and phrases used in the industry.