— 14 min read
QC in Construction: How Builders Manage Quality Control
Last Updated Nov 15, 2024
Bianca Holtier Coury
Education Audience Marketing
18 articles
Bianca Holtier Coury spent 15+ years in various roles managing construction projects, such as Preconstruction Team Lead, Purchasing Agent, and Project Manager. She has a wealth of experience in all project phases, including managing project schedules and budgets, bid management, and coordinating vendors and subcontractors. Bianca is an Associate Member of AIA and a LEED Green Associate. She currently serves as Director of Partnerships for the Construction Progress Coalition. Bianca holds a BA in Urban Design and Architecture Studies from NYU. She lives in Cleveland, OH.
Bob Hanes
Founder
14 articles
Bob Hanes is a professional writer and entrepreneur. He previously worked as a military sales and applications engineer for an aerospace firm, and cofounded a biotech company that creates drug screening solutions for the pharmaceutical industry. Bob has an MBA from the University of Buffalo in Logistics, Materials, and Supply Chain Management, and a BE in Mechanical Engineering. He is an avid Buffalo Bills fan.
Last Updated Nov 15, 2024
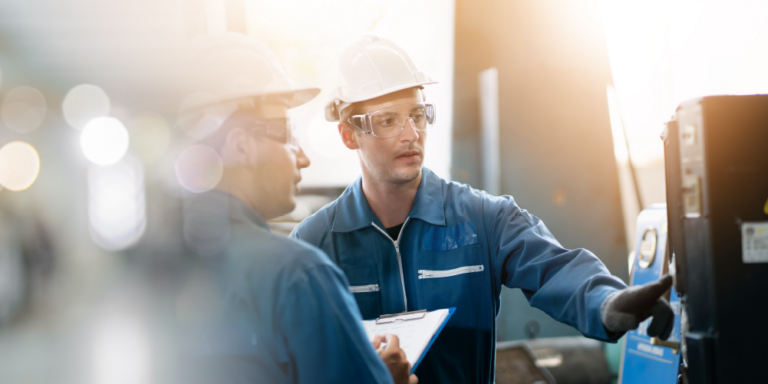
In construction, quality control (QC) refers to the procedures and activities to directly monitor, regulate, and correct deficiencies in the quality of materials, methods, and the final product. The aim of QC is to ensure that the end product meets the specified quality standards, conforms to the design specifications, and complies with regulatory requirements. In essence, QC answers the question, "Is the work done correctly?"
Every construction project begins with the owner's vision, which is translated into drawings and specifications by the design team. A diverse team of contractors, subcontractors, vendors and suppliers provide materials, equipment and labor to bring the vision to life. With so many moving pieces and stakeholders involved, ensuring that the end result matches the design — and complies with regulatory requirements — can be a significant challenge.
In this article, we explain the various ways quality control is managed in construction, address solutions to common challenges in identifying and correcting non-conforming work, and provide a guide to creating a quality control plan.
Table of contents
Construction Quality Control: The Basics
Quality control is managed on a construction project through a series of processes and activities that are designed to identify and correct deficiencies, non-conformance, or omissions in the construction materials, equipment, or methods.
Though “quality control” and “quality assurance” are often used interchangeably, the two approaches differ in their area of focus: correction vs. prevention. Quality control is a reactive process, with activities designed to catch and correct quality issues before they impact the project. Quality assurance, on the other hand, is a more proactive process that focuses on improving and optimizing the construction processes to prevent defects or mistakes.
Management of quality control involves a wide variety of activities both on the jobsite and in the office, from specifications and submittals to inspections and rework.
Learn more: The Importance of Minimizing Construction Rework
Specifications
Specifications are the backbone of quality control in construction. They provide detailed guidelines for every aspect of the construction process, ensuring that all stakeholders have a clear understanding of the expected outcomes. These specifications are often developed during the predevelopment phase of a project, laying out the groundwork for the entire construction process.
The design team — consisting of architects, engineers, and consultants — plays a pivotal role in creating these specifications. Their expertise ensures that the designs are not only aesthetically pleasing but also functional and safe. Their involvement ensures that the final product aligns with the vision of the project owner and adheres to all safety and quality standards.
In the U.S., the Construction Specifications Institute (CSI) uses MasterFormat, which is recognized as the gold standard for organizing construction specifications. It provides a structured format, ensuring that all details are systematically categorized.
The three-part spec for each material or work item, combined with the drawings, equips subcontractors with every detail they need to meet the project's quality requirements. During inspections, the work and materials can be easily compared to the specifications to identify errors, omissions, or other quality issues.
Submittals
One of the key aspects of quality control is the submittals system, which ensures that all materials and workmanship meet the specified standards. The submittal process involves the submission of shop drawings, material samples, and other relevant documents by trade partners or subcontractors. These documents provide detailed information about the materials and methods proposed for use in the construction project.
Once these documents are received, they are reviewed by the general contractor, who then forwards them to the architect and engineer for approval. This process ensures that the proposed materials and methods align with the project's design specifications. Any discrepancies or deviations from the original design are identified, allowing for corrections before the actual construction begins. This proactive approach helps in preventing potential quality issues down the line. By reviewing and approving submittals, designers can ensure that their design intent is accurately translated into the built environment.
Effective communication is key during this phase. The general contractor(GC) acts as a quarterback, coordinating between the design team and the trade partners to ensure that everyone is on the same page regarding quality requirements. In cases where there are discrepancies or potential quality issues, the involved parties collaborate to find solutions. This might involve revising the design, sourcing alternative materials, or adjusting construction methods.
The shared responsibility between architects, engineers, and contractors ensures that quality standards are consistently maintained. For instance, when a defect or deficiency is identified, there's a structured process in place to log the occurrence, go through checks and balances, and reorder materials if necessary.
Inspections
Regular jobsite inspections and daily logs are pivotal in ensuring the quality of construction projects. These processes not only help in identifying and quickly fixing potential issues but also play a significant role in ensuring that the project adheres to the set standards and specifications.
Inspections are not just about the final check before project closeout. They are a continuous process that takes place at various stages of construction to ensure that every aspect and phase of the project is executed correctly. For instance, inspections can uncover MEP (Mechanical, Electrical, and Plumbing) clashes, where some piping might not have aligned properly. Identifying such issues early on can prevent costly rectifications later.
Addressing quality issues promptly is essential to prevent delays and additional costs. For example, if a structural element is found to be out of alignment, the issue is documented, relevant teams are immediately notified, and corrective action, such as repositioning or reinforcing the element, is taken to bring it into compliance with design specifications. Effective communication is key in this process. The general contractor, architects, engineers, and other stakeholders collaborate to find solutions to any identified quality issues.
Communication
Effective communication is incredibly important in quality control. Coordination and communication between all parties ensure that everyone is on the same page, reducing the chances of errors or misunderstandings.
Technology plays an increasingly important role in streamlining communication. Centralized systems allow for real-time communication of plan changes, inspection reports, and quality issues, keeping everyone on the jobsite in the know.
Quality Control vs Cost Control: A Balancing Act
Quality control and cost control are two critical pillars of a construction project. While ensuring the highest standards of quality is paramount, managing costs effectively is equally crucial for the success of a project. Balancing these two aspects can often be a challenging endeavor.
Meeting quality standards within a budget
Owners and developers have a vision for their projects, and they want them executed to perfection. However, they also have budget constraints. Ensuring that a project meets the desired quality standards without overshooting the budget is a significant challenge.
Unforeseen challenges, such as unexpected occurrences like floods or material defects, can lead to additional costs that were not initially accounted for. These unexpected costs can strain the budget and necessitate adjustments in other areas to maintain the overall financial health of the project. This is where contingency funds come into play.
When crafting the project budget, it's wise—and often considered a "win"—for all parties involved to negotiate and allocate a contingency reserve. This reserve serves as a financial cushion that can be accessed to cover unexpected costs without derailing the entire budget. By doing so, stakeholders can maintain the overall financial health of the project while still adhering to the desired quality standards.
Project delivery methods to balance design and cost considerations
Different project delivery methods can help strike a balance between design aspirations and cost considerations. For instance, methods like design-build or integrated project delivery can offer more flexibility and collaboration, allowing for adjustments in design to meet budget constraints. In contrast, traditional methods like Design-Bid-Build (DBB) might be more rigid, making it challenging to adapt when faced with unforeseen costs.
Owners also frequently encourage value engineering to solicit input from contractors on materials or methods to find more cost-effective alternatives without compromising quality. This process ensures that the project remains within budget while still meeting the desired quality standards.
Roles And Responsibilities In Quality Control
Quality control is not the duty of a single person or company. Instead, it is a shared responsibility that involves various participants, each playing a crucial role in ensuring the project meets the highest standards of quality. From the initial design phase to the final construction, every stakeholder has a part to play in ensuring the project's quality. Architects and engineers, for instance, set the standard when they sign off on drawings, establishing the benchmark for quality. Let’s talk about the role that each party plays in the quality control process.
Owners
Owners set the expectations and establish standards for the project. Through prequalification and procurement, they aim to select a main contractor that can effectively manage their quality and safety programs with their subcontractors or trade partners. During construction, the owner or an owner’s representative may be involved in quality and safety inspections.
Design Team
The design team — a group of architects, engineers, and other design professionals — is responsible for creating drawings, plans, detailed specifications, and scope of work packages that clearly define the quality standards and installation methods of the materials on the project. They are deeply involved during the submittals process, reviewing materials and equipment to ensure they meet the design requirements. Their design expertise ensures that the designs are functional, safe, and aligned with the owner's vision.
General Contractor
The prime or general contractor bears the ultimate responsibility for ensuring the project is built and delivered according to the quality standards established by the design team and regulatory bodies. They select a team of subcontractors based on their ability to produce quality work, and they coordinate their activities during the project to ensure that the construction process adheres to the set specifications. It's essential to note that any deviations from the original plan or change orders typically require the explicit approval of the owner.
This step is crucial to ensure that any alterations align with the owner's vision and standards, and also to maintain transparency in quality control and budget management. Obtaining owner approval for change orders serves as an additional layer of checks and balances, reinforcing the collaborative nature of quality control in construction projects. For large or complex projects, the general contractor will often employ a Quality Control Manager who is responsible for coordinating all QC activities, like submittals, inspections, rework, etc.
Specialty contractors and suppliers
These stakeholders are responsible for specific parts of the construction process. They must adhere to the quality standards set in the project specifications. For instance, if electrical components arrive on-site and are found to be non-compliant with safety standards, the issue is promptly recorded, key stakeholders are notified, and replacement parts that meet the required guidelines are ordered.
Individual Roles: CM, PM & Superintendent
Depending on the construction manager’s role and their contractual relationship with the owner, a construction manager can be heavily involved in QC activities. The CM typically oversees the entire construction process, operating as the owner’s eyes and ears to ensure that all activities align with the set specifications and quality standards. In their capacity as an owner’s rep, they will provide the owner with inspection reports and manage the resolution of quality issues with the responsible contractors.
A project manager's role in quality control is holistic — they touch almost every part of the QC process. They establish a jobsite culture and environment where quality is prioritized, ensuring that the right processes, resources, and communication lines are in place to meet or exceed the project's quality standards. The PM typically works hand-in-hand with the superintendent.
As someone who walks the jobsite daily, the site superintendent is one of the most hands-on participants in QC. They verify work as it happens and act as the first line of defense to identify any deviations or issues. The superintendent works closely and communicates frequently with the project manager, ensuring that the construction materials and methods adhere to the project specifications.
Creating a Quality Control Plan
A robust quality control plan (QCP) is essential for ensuring that construction projects meet the desired standards and specifications. It serves as a roadmap, guiding all stakeholders in their roles and responsibilities related to quality assurance and control.
The Key Elements of a QCP
Section | Details |
Introduction | Provides a project overview, including a description of the project, scope, objectives, and the purpose of the QCP. |
Definitions | List of terms, acronyms, and definitions for clarity. |
Roles & Responsibilities | Outline of key personnel responsible for quality control, their specific duties, and contact information. |
Quality Standards & References | Specific quality standards and benchmarks, including reference to industry standards, codes, regulations, or client specifications. |
Inspection and Testing | List of inspections, tests, and verification activities. Details on timing, personnel, and acceptance criteria. |
Documentation and Record Keeping | Procedures for maintaining and storing QC documentation. Defines types of records: inspection reports, test results, etc. |
Control of Non-Conforming Work | Procedure for identifying, documenting, and rectifying non-conforming work.Describes how decisions are made on repair, rework, or rejection. |
Training | Details on training programs, workshops, or external programs. |
Resources | List of tools, equipment, and facilities for QC.List of external agencies, labs, or service providers as needed. |
Performance Monitoring & Continuous Improvement | Procedures for monitoring the QCP's effectiveness, including strategies for reviewing and updating the QCP based on feedback..Report types, reporting frequency, and recipients. |
Other Information | Supporting documents, forms, checklists, etc. |
Establishing protocols, procedures, and documentation requirements
Having a site-specific quality control plan in place sets up the project for success. When unforeseen challenges arise, a robust plan ensures that there are procedures to address them promptly. Documentation is crucial. Whether it's logging defects, recording inspection results, or noting changes to the original plan, maintaining accurate records ensures transparency and accountability.
Technology can play a role in streamlining this process. Centralized systems or construction management software can make it easy for contractors and owners to identify quality issues quickly and take action to correct them before more expensive rework is required.
A well-structured quality control plan is the foundation for ensuring that construction projects meet the highest standards of quality. By defining objectives, assigning roles, and establishing clear protocols, all stakeholders can work collaboratively to achieve the desired outcomes.
Stay updated on what’s happening in construction.
Subscribe to Blueprint, Procore’s free construction newsletter, to get content from industry experts delivered straight to your inbox.
Gain industry expertise, stay ahead of the curve
Explore valuable insights into the latest construction trends and project management best practices.
Subscribe to the newsletterGain industry expertise, stay ahead of the curve
Explore valuable insights into the latest construction trends and project management best practices, and learn how Procore's platform can optimize your projects.
Subscribe to the newsletterRequest a demo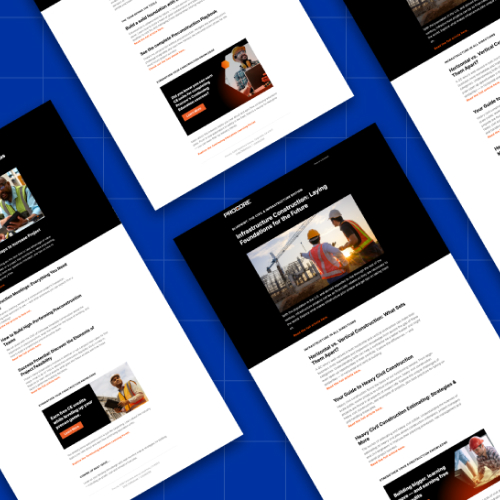
Quality Control Checklist
A quality control checklist is a vital tool in the construction industry, ensuring that projects meet the desired standards and specifications. Tailoring this checklist to the unique requirements of each project is essential for its effectiveness.
Tailoring the checklist to specific projects
There is no one-size-fits-all quality checklist for construction projects. Different projects, such as a commercial office building or a road construction project, will have distinct quality standards and concerns. The checklist should be based on the spec book for an individual project.
However, merely relisting the entire spec book is not practical. A seasoned construction manager or general contractor with experience in the specific type of project should utilize historical project data to identify the most common quality issues to monitor.
As a project progresses through its various phases, the QC checklist should evolve to address the specific quality concerns relevant to each phase. For instance, the checklist for the foundation phase of a building will differ from the checklist for the finishing phase. Adapting the checklist ensures that quality standards are maintained consistently from start to finish.
Safety and risk mitigation
Quality control is intrinsically linked to safety and risk mitigation. A robust quality control system serves as a foundation for ensuring the safety of all stakeholders involved in a project.
Quality control as a foundation for safety
Quality control and safety are deeply intertwined. A strong quality control program is often a mechanism through which safety standards are upheld on a construction site. Quality control is the foundation for how construction professionals engage with safety teams. It provides a systematic approach to identifying potential risks and addressing them proactively.
For instance, ensuring that materials used meet quality standards can prevent accidents related to material failures. Similarly, ensuring that work is done according to specifications can prevent structural issues that might pose safety risks.
The role of technology in quality control
With the advancement of technology, construction management software has become an invaluable tool for quality control. Software can streamline the process of identifying and addressing quality issues.
Forward-thinking companies are also adopting emerging technologies on the job site, which can offer advantages for quality control. By utilizing tools like Building Information Modeling (BIM), Virtual Design and Construction (VDC), and even augmented reality (AR) and virtual reality (VR), these companies are expanding their toolkit for quality control.
These digital applications transition the quality control process from being manual to more streamlined and efficient. For instance, using AR/VR or digital twins can help visualize potential issues before they become real problems, allowing for proactive mitigation.
Quality control in construction is more than a procedural obligation — rather, it is a necessary investment in the project’s longevity and safety, and the reputation of all construction firms involved. It is essential for industry professionals to prioritize and continuously refine quality control processes and technologies, ensuring that every construction project stands as a testament to excellence, safety, and durability.
Was this article helpful?
Thank you for your submission.
97%
3%
You voted that this article was . Was this a mistake? If so, change your vote here.
Scroll less, learn more about construction.
Subscribe to The Blueprint, Procore’s construction newsletter, to get content from industry experts delivered straight to your inbox.
By clicking this button, you agree to our Privacy Notice and Terms of Service.
Thank you!
You’re signed up to receive The Blueprint newsletter from Procore. You can unsubscribe at any time.
Categories:
Tags:
Written by
Bianca Holtier Coury
Education Audience Marketing | Autodesk
18 articles
Bianca Holtier Coury spent 15+ years in various roles managing construction projects, such as Preconstruction Team Lead, Purchasing Agent, and Project Manager. She has a wealth of experience in all project phases, including managing project schedules and budgets, bid management, and coordinating vendors and subcontractors. Bianca is an Associate Member of AIA and a LEED Green Associate. She currently serves as Director of Partnerships for the Construction Progress Coalition. Bianca holds a BA in Urban Design and Architecture Studies from NYU. She lives in Cleveland, OH.
View profileBob Hanes
Founder | Resonant Lab
14 articles
Bob Hanes is a professional writer and entrepreneur. He previously worked as a military sales and applications engineer for an aerospace firm, and cofounded a biotech company that creates drug screening solutions for the pharmaceutical industry. Bob has an MBA from the University of Buffalo in Logistics, Materials, and Supply Chain Management, and a BE in Mechanical Engineering. He is an avid Buffalo Bills fan.
View profileExplore more helpful resources
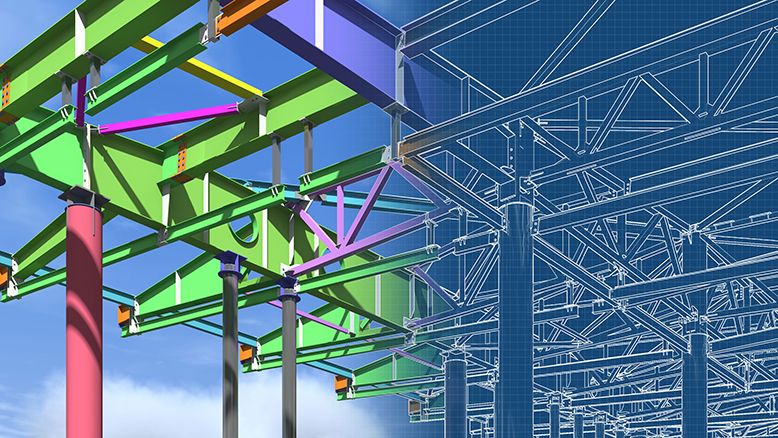
BIM’s Role in Risk Mitigation: Strategies for Success
Building information modeling (BIM), has been touted as a way to deliver a broad range of wins on any construction project. It supports stronger planning and smoother collaboration. It provides...
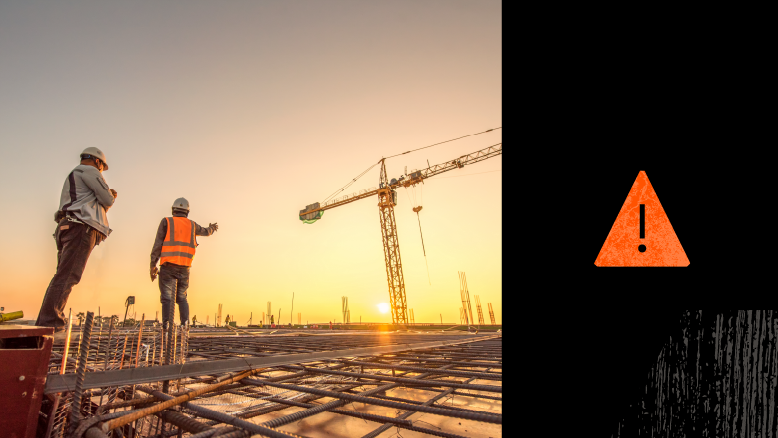
Risky Business: Transforming Risk Mitigation into Risk Prevention
Risk burrows into every aspect of construction — costs, safety, labor, scheduling, profitability and even market leadership. In an inherently dangerous industry, risk is inevitable, but truly powerful risk mitigation doesn’t...
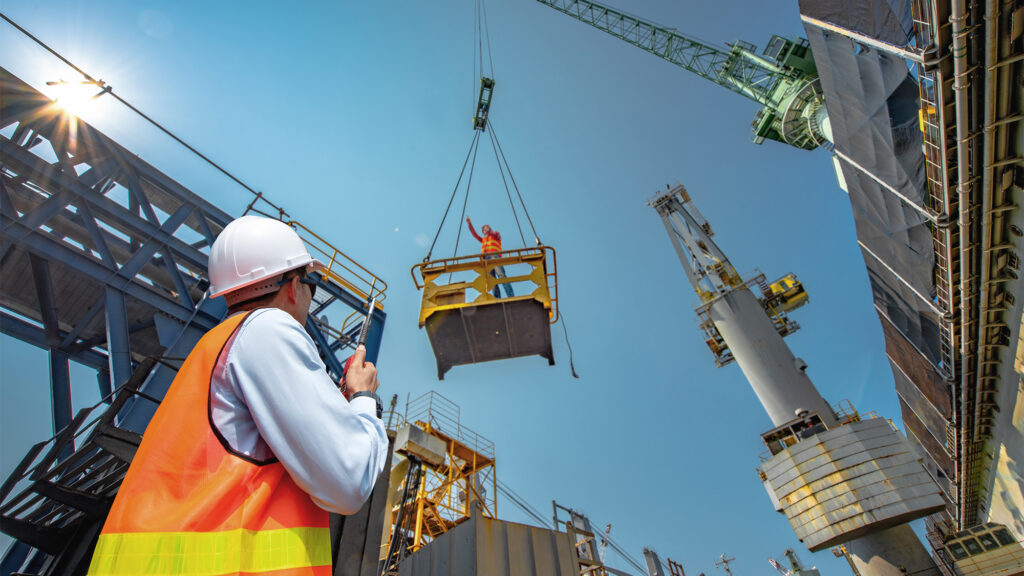
Using AI to Manage Risk in Construction
Since the day construction became an industry, many people have been trying to manage the risks of building things — to identify and mitigate potential conditions that might impact a project’s...
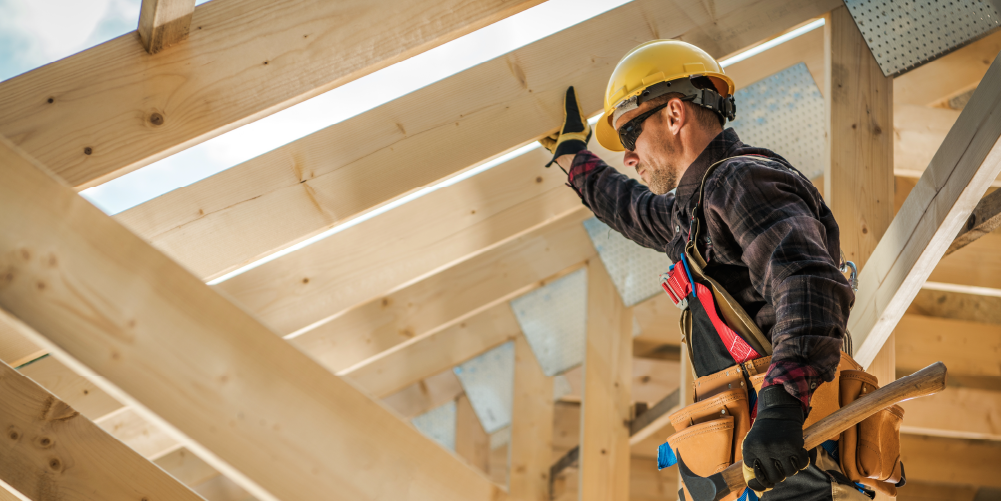
Mitigating Subcontractor Risk: Pro Tips for General Contractors
Every construction project comes with unique risks, and assessing and mitigating subcontractor risks is necessary for general contractors (GCs) to maintain profitability and smooth operations. Effectively planning for and managing...
Free Tools
Calculators
Use our calculators to estimate the cost of construction materials for your next project.
Templates
Find a template to help you with your construction project tasks.
Material Price Tracker
Get the latest U.S. retail prices and view historical trends for common building materials.
Glossary
Explore key terms and phrases used in the industry.