— 7 min read
How to Write a Construction Safety Report
Last Updated Sep 1, 2024
Bob Hanes
Founder
14 articles
Bob Hanes is a professional writer and entrepreneur. He previously worked as a military sales and applications engineer for an aerospace firm, and cofounded a biotech company that creates drug screening solutions for the pharmaceutical industry. Bob has an MBA from the University of Buffalo in Logistics, Materials, and Supply Chain Management, and a BE in Mechanical Engineering. He is an avid Buffalo Bills fan.
Anthresia McWashington
Content Manager
19 articles
Anthresia McWashington is a Content Manager at Procore. She previously worked as an editor and reporter for Gulf Energy Information and Houston Media Group. She earned her BA in Communications and Journalism from the University of Houston. Anthresia loves track & field and practicing her French. She lives in Houston.
Justin Bogoyevac
Justin Bogoyevac brings 11 years of prior experience working as a Safety Specialist for an electrical subcontractor, and an EHS Specialist at Amazon to his role as Global EHS Specialist role at Procore. Additionally, Justin proudly served 10 years as a U.S. Army combat medic, completing two tours in Afghanistan. His expertise in OSHA and industry standards was developed through various positions in federal, general industry, and construction safety. Justin holds an M.S. in Emergency Services Management from Columbia Southern University.
Last Updated Sep 1, 2024
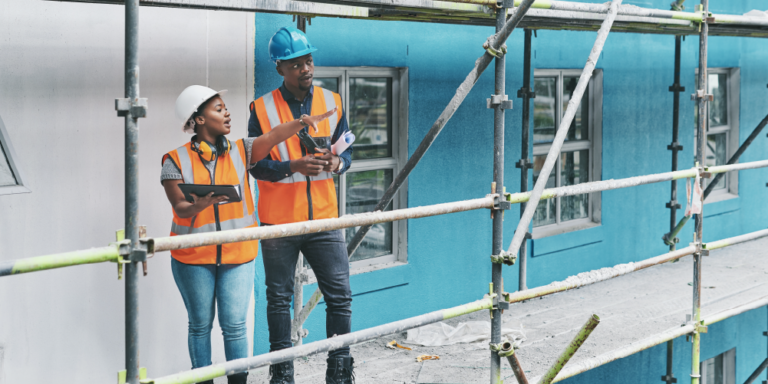
As the construction industry continues to grow and evolve, the importance of ensuring worksite safety has become increasingly important. Construction safety reports are an essential tool for safety managers to monitor and maintain a secure work environment.
Safety managers are responsible for identifying potential hazards, drafting safety plans, and regularly conducting safety audits to ensure that the onsite personnel are taking proper safety precautions. With the amount of documentation construction safety professionals have to keep track of for onsite projects, digital reporting, and construction software are invaluable assets in keeping relevant information and safety changes up to date.
In this article, we will discuss construction safety reports in greater detail, including what they are, what to include in them, and how digitizing the reporting process may help improve safety on construction sites.
Table of contents
What is a construction safety report?
A construction safety report is used by contractors during jobsite inspections to identify potential safety hazards or instances of non-compliance with safety measures. These reports serve as a preventive tool, helping to address hazards before they lead to accidents, injuries, or fatalities.
Because construction projects are constantly evolving, with new hazards emerging at any time, safety managers are constantly adjusting and documenting safety plans. For example, a newly excavated trench or removal of guardrails on elevated structures pose new risks that onsite workers may not be privy to.
By conducting regular safety reports, contractors can take a snapshot of the jobsite, evaluate the work environment, and identify any existing or potential hazards.
Safety reports differ from job hazard analyses (JHAs), which focus on specific tasks and their associated risks. While JHAs aim to mitigate risks by outlining a plan for each task, safety reports provide a broader overview of the job site's safety status at a given time.
These reports can be conducted daily, weekly, or monthly, depending on the project's size and complexity. A safety professional typically will carry out routine safety inspections, but multiple individuals may also be involved in the process. Safety inspections are typically performed by the safety team or site manager, but they can also be conducted by construction workers who are trained in safety protocols.
Safety reports can be prepared either in handwritten or digital format, though digital reports are preferred due to their real-time nature and ease of tracking. Digital reports offer greater visibility, ensuring that open safety action items are promptly addressed and resolved. This capability improves efficiency by streamlining the process, storing historical data, and organizing documentation. Accuracy is also improved with digital tools as they reduce the potential for human error in manual reporting.
During site safety walks, safety managers collaborate with subcontractors to identify and address any onsite hazards. After identifying potential risks or dangers, they may need to update their site specific safety plan, daily logs, or other reports and develop an action plan to remove these hazard. If substantial hazards for onsite workers are present, safety and site leadership may shut down an area to prevent accidents.
Courses about construction.
For construction.
Unlock your career potential with our free educational courses on Health & Safety, Data in Construction, and more.
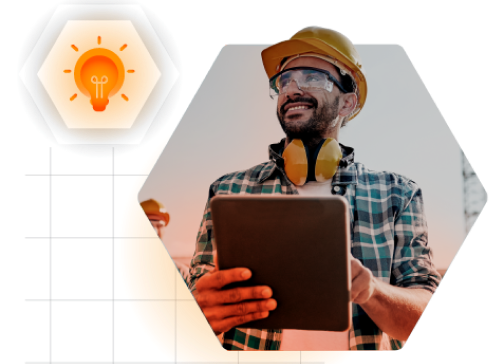
What to include in a safety report
Safety reports also help construction safety directors monitor the work site and ensure compliance with industry regulations, such as those mandated by the Occupational Safety and Health Administration (OSHA). Construction companies may have varying safety report structures, but they commonly include the following items:
- Personal protective equipment (PPE): This section of the report should identify the PPE required for the particular construction project and detail how often it is inspected and used.
- First aid: All job sites must have first aid kits, and the report should document their location, contents, inspection frequency, and date of the last refill.
- Fire prevention: Identify any fire risks at the site, and document the measures taken to mitigate those risks. These may include fire extinguishers, hydrants, and emergency exits.
- Fall prevention: This section of the report should identify all the fall protection measures in place, such as harnesses and netting, and document how often they are inspected and used.
- Scaffolding: Document who erected the scaffolding, when they erected it, and how long it will be in place, as it is a high-risk area.
- Heavy equipment: Include a section in the report for cranes, as they have specific OSHA standards to adhere to. The report should detail their use and inspection frequency, including daily inspections.
- Electrical safety: Verifying the proper use and maintenance of electrical equipment, including regular inspection of extension cords and adherence to color-coding protocols.
More on electrical safety: An Electrician's Guide to PPE on the Jobsite
Variables may change depending on the type of construction project. For instance, identify in the report that high-rise buildings require new perimeters with guardrails as each level is constructed. There are also specific OSHA requirements for fall protection, which might need to be monitored more closely in such projects.
Other items commonly included in a safety report are electrical power tools, barricades, housekeeping, and extension cords. Having a safety report can be helpful in case of any OSHA complaints. Safety reports give a record to show the details of what’s happening onsite to increase safety measures. Moreover, if an injury occurs on the job, a safety report can provide strong evidence of due diligence in protecting workers.
Assessing risk probability & impact
A risk matrix is a tool that helps assess the probability and impact of safety issues on a construction site. It helps to identify the severity of risks and the likelihood of their occurrence. By using a risk matrix, safety professionals can better prioritize hazards and allocate resources for mitigation.
The risk matrix chart works by combining the probability of a hazard occurring with its potential impact. This results in a risk rating that can range from low to catastrophic. Use the risk rating to prioritize safety measures and allocate resources accordingly.
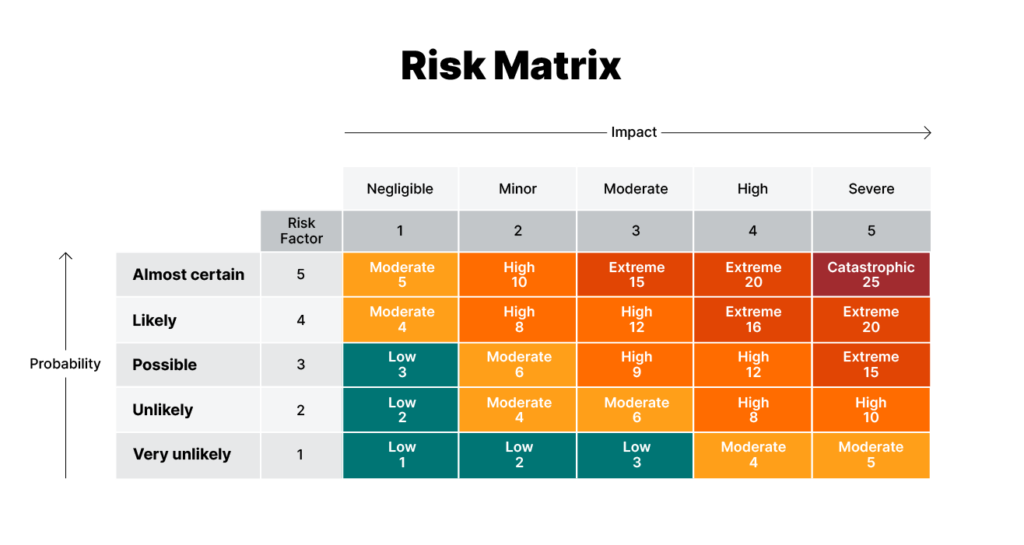
Examples of items that would fall into the broad categories of the risk matrix include:
Negligible: If a worker handles metal studs without wearing gloves, they may sustain a minor cut that can be treated with a bandage. This type of injury is generally not reported and has a low impact on safety records.
Minor: An injury that requires stitches or medication would be considered a minor incident. These incidents are important to address, as they count as first-aid injuries and can affect the company's safety record.
Moderate: Injuries that require stitches, prescription medication, or urgent care would fall into the moderate category. These incidents often involve additional paperwork, drug screenings, and involvement from subcontractors and their safety personnel. Conduct root cause analysis and after-action reviews following a moderate incident.
High: Lost time incidents, such as those resulting in time off work, are considered high risk. Report these incidents to OSHA, as they can significantly affect a company's safety performance and compliance.
Severe: Injuries that result in the loss of a limb or eyesight are classified as extreme risks. These incidents are highly impactful and require immediate attention from safety personnel. Fatal incidents are considered severe risks. Dedicate the highest level of attention and resources to preventing such incidents and report them to OSHA.
It is important to note that risk assessment can be subjective, and different safety professionals may assign different risk ratings to the same hazard. However, using a risk matrix provides a common language and framework for assessing risks across different teams and organizations.
Safety reporting with construction software
Safety reports must be kept up to date every day. Safety managers are responsible for ensuring documentation reflects any changes or updates to plans, and that these plans and safety messaging are communicated across project stakeholders. But updating these reports manually is a tedious and time-consuming process.
Paper documents can be easily lost or damaged which can cause lapses in communication about new hazards or safety incidents that occur onsite. With digital construction tools, safety personnel can easily track and document reports, site changes, and communication with contractors and site leaders. This may encourage and enable project teams to collaborate and address safety concerns in real time.
By digitizing safety reports and making them accessible to all stakeholders, construction software helps site leadership and workers prioritize safety more efficiently, maintain compliance with industry regulations, and create a safer workplace for employees.
Learn more about reporting – Construction Reporting: Key Report Types & Best Practices
this is part of the series
Construction Safety Basics
Was this article helpful?
Thank you for your submission.
100%
0%
You voted that this article was . Was this a mistake? If so, change your vote here.
Scroll less, learn more about construction.
Subscribe to The Blueprint, Procore’s construction newsletter, to get content from industry experts delivered straight to your inbox.
By clicking this button, you agree to our Privacy Notice and Terms of Service.
Thank you!
You’re signed up to receive The Blueprint newsletter from Procore. You can unsubscribe at any time.
Categories:
Tags:
Written by
Bob Hanes
Founder | Resonant Lab
14 articles
Bob Hanes is a professional writer and entrepreneur. He previously worked as a military sales and applications engineer for an aerospace firm, and cofounded a biotech company that creates drug screening solutions for the pharmaceutical industry. Bob has an MBA from the University of Buffalo in Logistics, Materials, and Supply Chain Management, and a BE in Mechanical Engineering. He is an avid Buffalo Bills fan.
View profileAnthresia McWashington
Content Manager | Procore
19 articles
Anthresia McWashington is a Content Manager at Procore. She previously worked as an editor and reporter for Gulf Energy Information and Houston Media Group. She earned her BA in Communications and Journalism from the University of Houston. Anthresia loves track & field and practicing her French. She lives in Houston.
View profileReviewed by
Justin Bogoyevac
Justin Bogoyevac brings 11 years of prior experience working as a Safety Specialist for an electrical subcontractor, and an EHS Specialist at Amazon to his role as Global EHS Specialist role at Procore. Additionally, Justin proudly served 10 years as a U.S. Army combat medic, completing two tours in Afghanistan. His expertise in OSHA and industry standards was developed through various positions in federal, general industry, and construction safety. Justin holds an M.S. in Emergency Services Management from Columbia Southern University.
Explore more helpful resources
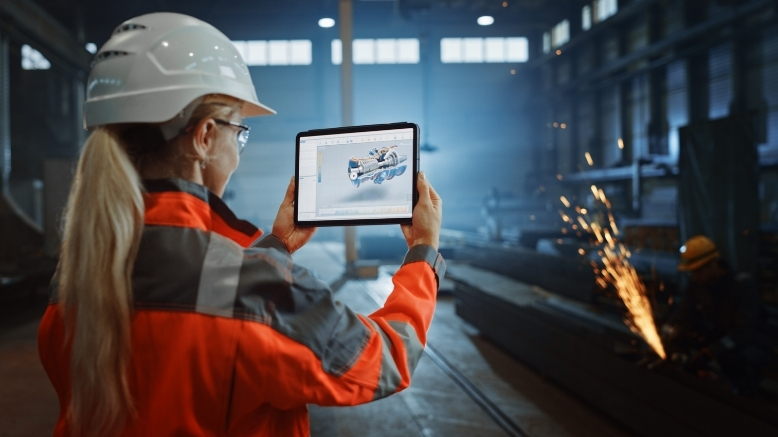
Gain Without Pain: Leveraging Technology for Strategic Safety Programs
In safety, there is always room for improvement, and technology creates the ability to scale safety programs that drive risk mitigation, operational efficiencies and competitive advantage. In fact, builders who...
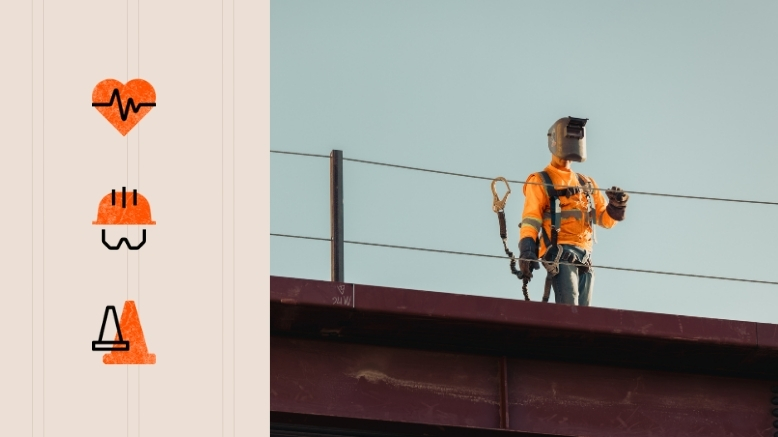
The S#*! That Can Kill You: Rethinking Safety on the Jobsite
Construction sites are full of risk — but not all risks are equal. The industry has long celebrated falling recordable injury rates, yet fatality numbers haven’t budged since around 2007....
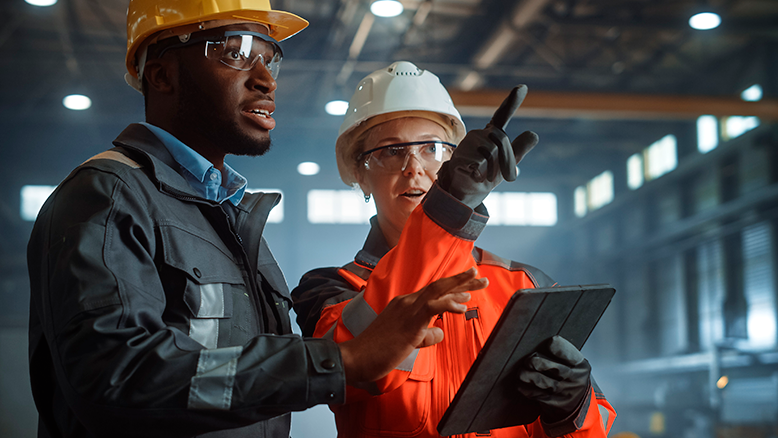
On the Safe Side: Using Data to Boost Subcontractor Safety
Capturing data to mitigate the safety risks incurred by subcontractors as well as in-house workers demands proactive risk management measures, transparent change management and methodical strategy. Applying data to safety...
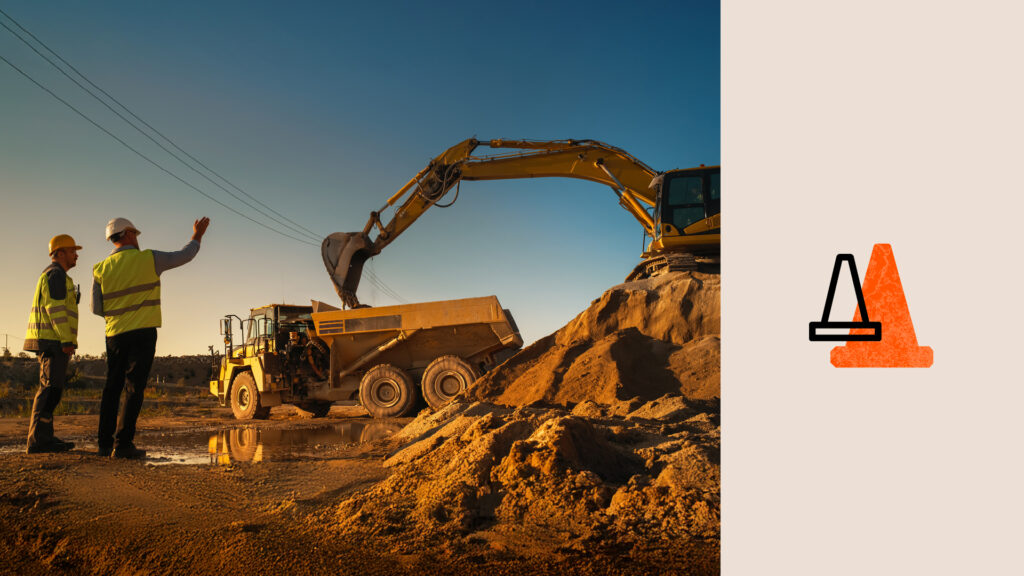
Top Techniques for Heavy Equipment Safety & Operations
Nearly 1 of every 5 workplace fatalities occurs in the construction industry. It is increasingly important to create a culture of safety and reduce the risk of workplace accidents, and...
Free Tools
Calculators
Use our calculators to estimate the cost of construction materials for your next project.
Templates
Find a template to help you with your construction project tasks.
Material Price Tracker
Get the latest U.S. retail prices and view historical trends for common building materials.
Glossary
Explore key terms and phrases used in the industry.