— 5 min read
On the Safe Side: Using Data to Boost Subcontractor Safety
Last Updated Jun 20, 2025
Anthony Verdiglione
Senior Strategic Product Consultant
Anthony Verdiglione is a seasoned construction professional and accomplished project manager with more than two decades of solid experience. Well-versed in nearly every construction discipline, Anthony adds immediate value to any transaction, leveraging his vast base of knowledge to drive projects, profits, and the industry. A true champion of construction, he works tirelessly to stay abreast of the latest trends while passing that value on to the customers he dutifully services.
Diane McCormick
Writer
24 articles
Diane McCormick is a freelance journalist covering construction, packaging, manufacturing, natural gas distribution, and waste oil recycling. A proud resident of Harrisburg, PA, Diane is well-versed in several types of digital and print media. Recognized as one of the premier voices in her region, she was recognized as the Keystone Media Freelance Journalist of the Year in 2022 and again in 2023.
Last Updated Jun 20, 2025

Capturing data to mitigate the safety risks incurred by subcontractors as well as in-house workers demands proactive risk management measures, transparent change management and methodical strategy.
Applying data to safety generates the power to reveal root causes of hazards, infuse safety-oriented cultures from front offices to jobsites, mitigate the risks that drive up costs and cause delays — and even win jobs from increasingly safety-conscious project owners.
A plan to build capabilities is the key to data-driven decisions that encourage subcontractors and employees alike to participate in a uniform, fair and effective safety culture.
Table of contents
Different Teams, Different Risks
GCs that self-perform and also hire specialty contractors now have new means for enforcing safety rules consistently, across sites and across teams. However, each team requires a different approach for assessing risk:
Self-performers: Weigh the costs — in every sense — of jobsite accidents. For self-performing GCs, especially, incidents can take manpower off the job, trigger higher insurance rates and even disqualify the firm from bidding for jobs issued with prerequisite safety thresholds.
Hired Subcontractors: When subcontractors are needed, data opens a window into historical safety performance. If they are past partners, history shows whether they consistently follow or flout site-specific safety rules. If they are new, their safety rates disclose how closely they adhere to standard safety procedures.
During bid review, a specialty contractor’s excess safety incidents and violations can signal higher costs ahead in labor hours, project delays and time diverted from the daily duties of superintendents and safety supervisors.
Making Data Work for Safety
Start by collecting data consistently in a construction management platform. In time, adding tools such as 360 Reporting helps gather viewpoints from multiple stakeholders, but the job is still half-done because 360 Reporting is exactly that — reporting, without the benefit of insights.
Building information modeling (BIM) platforms that generate 3D models and automate clash detection also offer a wealth of information for mitigating safety risks among varied teams.
More keys to successfully using data to boost safety include the following.
Proper Documentation
The verbal, unrecorded safety warnings of the past were deniable and disputable. Today’s software allows superintendents to make simple voice memos or entries in preestablished fields to memorialize every warning and observed infraction. A documented record of who, what, when and where provides clarity for dispute-free analysis and resolution.
Documentation also dispels any perceived unfairness that comes from inconsistent enforcement. Instead of relying on the superintendent’s hazy recollections of warnings given, a documented number of violations can trigger enforcement and discipline that team members recognize as fairly administered.
Number one, you want consistency in data. Things are getting put in the same way every time. We're not missing fields that could then create data holes when reviewing the report. I want consistency. Once I have consistency, then it becomes about what I need to make this more customizable.
Anthony Verdiglione
Senior Strategic Product Consultant
Procore Technologies
Customized Solutions
Giving superintendents software preloaded with fields for recording observations gives a number to violations but not a cause — but further customization with additional fields digs down to the reasons.
Are the violations universal or only practiced by certain people? Are incidents associated with PPE infractions or failure to tie off? As company culture becomes accustomed to using data as a safety tool, custom fields help fill knowledge gaps and generate actionable, targeted insights.
Focus on Sharing
Be transparent with data. In subcontractor meetings, review safety observations and ask for explanations. If troubling trends start emerging, work on action steps to improve the numbers.
Schedule regular reviews to keep action steps timely, instead of letting problems fester. Be sure to assign responsibility and use construction management platforms to establish multidisciplinary accountability in-house and among subcontractors.
People Power
Data can capture the daily onslaught of safety incidents and near-misses, but it’s the people behind the data who make it actionable.
Proactive change management can nudge subcontracted and in-house personnel toward new mindsets, where they contribute to safety cultures that make every workplace safer, every day.
An effective approach drives change management through all stakeholders in a project:
Management
Superintendents and supervisors might balk at adding violation documentation to their daily tasks, until they learn the whys and the positive outcomes. Explain that accumulating data makes their jobs easier by giving them a third eye on the scene. As patterns emerge, the solutions can reduce jobsite hazards by eliminating the underlying causes. Plus, documentation in words and pictures provides verification if their observations are disputed or disregarded.
Tradespeople
A good catch is that moment when someone’s keen observation prevents trouble. A jobsite “good catch” program incentivizes in-house workers to report hazards and help their subcontracted teammates adhere to safety standards. Rewards could include company merchandise or pizza parties. The best catch of the year might win a cherished vacation day for the eagle-eyed worker. An effective “good catch” program also helps everyone understand how data supports their safety and the safety of their buddies. It gives them the satisfaction of being part of the solution, instead of the problem.
Leadership
“Do as I say, not as I do” has never been a prime motivator. On the jobsite and in the office, leadership must demonstrate their own willingness to abide by safety rules, go through safety training and use data as a tool to make people safer.
Overall, consistent use of data creates a firm foundation of safety rules and risk mitigation for in-house teams to adopt and subcontractors to follow for fewer incidents and greater operational efficiencies.
Be legit. Be honest. Be forthright with what is there. That way, you have good data. Good data in, good data out. Garbage in is garbage out.
Anthony Verdiglione
Senior Strategic Product Consultant
Procore Technologies
Was this article helpful?
Thank you for your submission.
0%
0%
You voted that this article was . Was this a mistake? If so, change your vote here.
Scroll less, learn more about construction.
Subscribe to The Blueprint, Procore’s construction newsletter, to get content from industry experts delivered straight to your inbox.
By clicking this button, you agree to our Privacy Notice and Terms of Service.
Thank you!
You’re signed up to receive The Blueprint newsletter from Procore. You can unsubscribe at any time.
Categories:
Tags:
Written by
Anthony Verdiglione
Senior Strategic Product Consultant | Procore Technologies
Anthony Verdiglione is a seasoned construction professional and accomplished project manager with more than two decades of solid experience. Well-versed in nearly every construction discipline, Anthony adds immediate value to any transaction, leveraging his vast base of knowledge to drive projects, profits, and the industry. A true champion of construction, he works tirelessly to stay abreast of the latest trends while passing that value on to the customers he dutifully services.
View profileDiane McCormick
Writer | Procore Technologies
24 articles
Diane McCormick is a freelance journalist covering construction, packaging, manufacturing, natural gas distribution, and waste oil recycling. A proud resident of Harrisburg, PA, Diane is well-versed in several types of digital and print media. Recognized as one of the premier voices in her region, she was recognized as the Keystone Media Freelance Journalist of the Year in 2022 and again in 2023.
View profileExplore more helpful resources
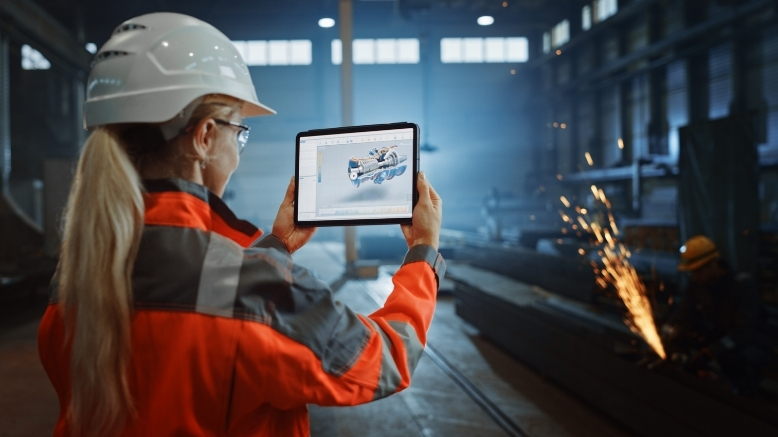
Gain Without Pain: Leveraging Technology for Strategic Safety Programs
In safety, there is always room for improvement, and technology creates the ability to scale safety programs that drive risk mitigation, operational efficiencies and competitive advantage. In fact, builders who...
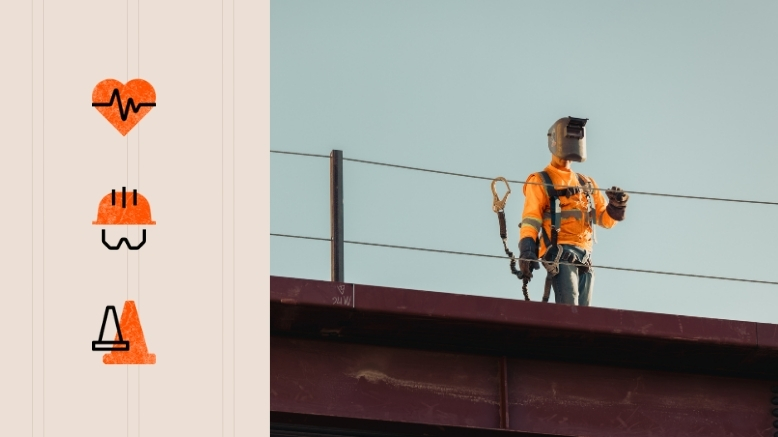
The S#*! That Can Kill You: Rethinking Safety on the Jobsite
Construction sites are full of risk — but not all risks are equal. The industry has long celebrated falling recordable injury rates, yet fatality numbers haven’t budged since around 2007....
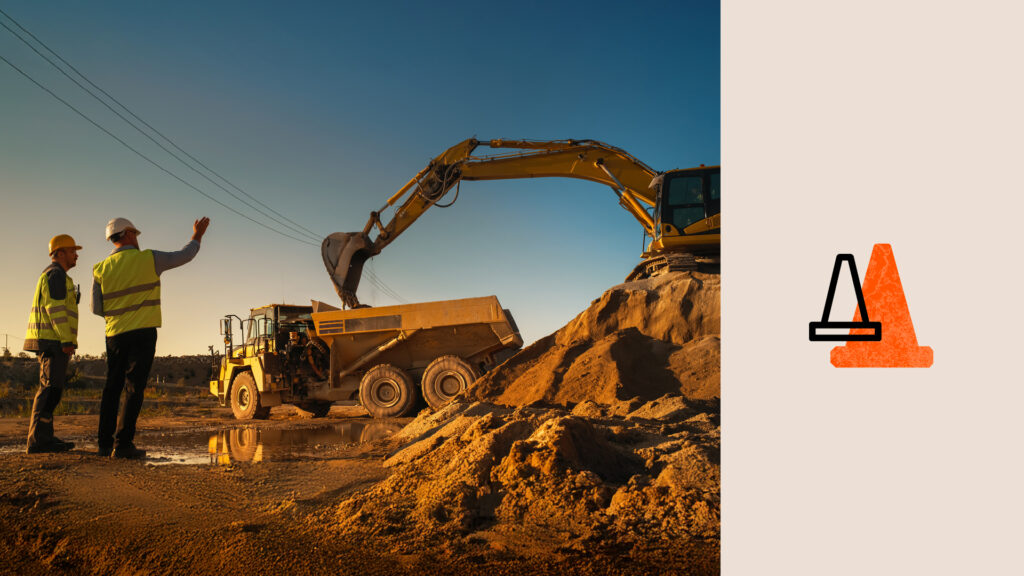
Top Techniques for Heavy Equipment Safety & Operations
Nearly 1 of every 5 workplace fatalities occurs in the construction industry. It is increasingly important to create a culture of safety and reduce the risk of workplace accidents, and...

Preconstruction Partnerships: How Safety Pros Can Collaborate with Estimating & Proposal Teams
Construction leaders and safety professionals are developing a strong understanding of how safety programs positively impact project outcomes. When safety is woven into every aspect of operations from pre-construction to...
Free Tools
Calculators
Use our calculators to estimate the cost of construction materials for your next project.
Templates
Find a template to help you with your construction project tasks.
Material Price Tracker
Get the latest U.S. retail prices and view historical trends for common building materials.
Glossary
Explore key terms and phrases used in the industry.