— 10 min read
Mitigating Subcontractor Risk: Pro Tips for General Contractors
Last Updated Aug 20, 2024
David Farino
Technical Brokerage Officer
David Farino is a Technical Brokerage Officer at Procore Technologies. He brings over a decade of experience in the construction and insurance sector to his position, including roles as Assistant VP and Vice President of Construction and Infrastructure at NFP and Senior Underwriter at Arch Insurance Group, Inc. David received his BBA in Business Administration and Management from Hofstra University. He is based in New York City.
Julia Tell
Contributing Writer
55 articles
Julia Tell is a freelance writer covering education, construction, healthcare, and digital transformation. She holds a Ph.D. in Media & Communications and has written for publications including Business Insider, GoodRx, and EdSurge, as well as nonprofits, international businesses, and educational institutions.
Last Updated Aug 20, 2024
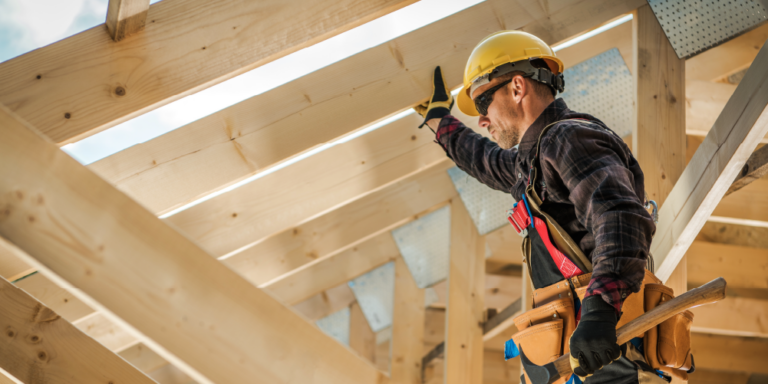
Every construction project comes with unique risks, and assessing and mitigating subcontractor risks is necessary for general contractors (GCs) to maintain profitability and smooth operations. Effectively planning for and managing the risks inherent in hiring trade partners can prevent problems down the line.
While surety bonds and subcontractor default insurance can mitigate the risks, using these solutions can add costs. Careful planning, clear contracts and communication and intentional oversight of subcontractors can minimize the financial, operational and reputational risks that can arise when working with subcontractors.
Learn more about risk management: 5 Steps to Reduce & Mitigate Risk
Table of contents
Key Types of Subcontractor Risk
The categories of risk that subcontractors pose are interrelated. A quality issue likely impacts the budget and schedule and potentially ends up as a contractual problem. GCs should use strategies to minimize the probability of each type of risk, as subcontractor difficulties can cause serious reputational damage.
Default
A subcontractor might default for many underlying reasons, but no matter the reason, it can cause a cascade of problems. Subcontractors can go out of business for financial reasons, have difficulty scheduling their crews as promised, or fail to deliver the required quality or scope of work.
Any failure to fulfill contractual obligations by the subcontractor will add cost, complication and potential reputational damage for the GC.
Financial
If the subcontractor defaults and doesn’t deliver the contracted work, the general contractor will need to find a way to complete the job, which will likely be more costly. If the subcontractor provides poor quality or faulty work, hiring a different sub to remove the faulty workmanship and rectify the problems also adds costs.
Any subcontractor default can cause delays to other trades, impacting the overall project schedule and budget.
Performance and Quality
If the subcontractor delivers faulty work that doesn’t meet standards or conform to the scope of work, the general contractor will have to take additional steps to either get the sub to rectify the problems or find another sub to fix the problems. In addition, shoddy work in one trade could adversely affect other aspects of the build or necessitate tearing out other work to access the area to address the problems.
The subcontractor's work culture and behavior impact the workflow and perceptions of the project for owners and, in some cases, the general public. If the subcontractor’s workers don’t follow safety practices, they pose a risk to themselves and others, and if they are challenging to work with, they can make life on-site difficult for other workers and trades. This is something that is seldom discussed yet very impactful to project teams.
Schedule Adherence
If one subcontractor falls behind on the schedule, it could have a domino effect on other work that depends on this trade’s completion to begin. The subcontractor may have difficulty scheduling their crews, as they are likely working on multiple projects, and hiring and keeping qualified workers can be a challenge for any construction company.
There could also be supply chain issues with necessary materials for their work, which could impact the whole construction schedule.
Reputation and Relationships
If a subcontractor fails to deliver quality work on time, the general contractor may not be able to fulfill its obligation to the owner to complete the project on time. A GC's reputation for successful project delivery is crucial. Even if the project finishes on time, difficulty with a sub can make the construction process challenging for all parties, which can impact a GC’s relationship with the owner.
General contractors must also maintain a good reputation for harmoniously working with their subcontractors. Even if the problems encountered during a project were the subcontractor’s fault, the rockiness of the process could reflect poorly on the general contractor, making it harder for them to attract the best-in-class subcontractors for the next project.
Contractual
Contract disputes arise when there are incomplete or incorrect scopes of work, cost estimation shortfalls, or unclear contract provisions. Clearly defined business terms such as payment arrangements, liability and indemnification and scopes of work can mitigate problems. With the complex construction process for large projects, changes and change orders are bound to arise, and conflicts can result in legal disputes that can be costly for general contractors, both in money and time lost.
5 Best Practices to Minimize and Mitigate Subcontractor Risks
General contractors, project managers, general counsel, risk managers, CFO/controllers, site superintendents and others play crucial roles in selecting and managing trade subcontractors to minimize risks.
GCs can incorporate the following tips to mitigate the disruptions that subcontractor problems can bring to the construction process.
1. Thorough Subcontractor Selection
General contractors should choose subcontractors based on a thorough preconstruction planning process. Construction management software manages the details and communication, allowing GCs to work in tandem with subcontractors from preconstruction meetings through mobilization, construction, and handover of the completed project.
Below are tips for GCs to vet the right contractors for their projects.
Build a trusted pool of prequalified subs.
Establish a pool of prequalified subcontractors and start there when inviting companies to bid.
When prequalifying a subcontractor, the GC should carefully comb through the subcontractor’s finances, project experience, work quality, and reputation. The subcontractor needs to have the cash on hand to pay workers and purchase materials, while also having the proven experience with similar scopes of work they are being solicited to perform.
Develop clear metrics for subcontractor review.
A general contractor should develop a set of metrics and protocols for reviewing every aspect of the subcontractor’s previous experience before awarding the contract. Companies should establish specific financial ratios that subcontractors need to meet.
Track even minor subcontractor details.
Details are what separate the top contractors from the rest, and tracking things as minor as a trade contractors’ reputation for maintaining a clean worksite and the potential impact when contemplating including them in a request for proposal for a job in which the public can see into the site, such as during a hospital renovation, or when stray materials can cause safety hazards; can make the difference durring project delivery.
Use value engineering.
Take advantage of value engineering to choose the best subcontractor capable of delivering the work at the lowest price. Paying a fair price for quality work requires balancing these two opposing objectives.
If a subcontractor is outside cash flow guidelines, the CFO or general counsel should sign off on the deviation from standard practice. The same is true for safety records, where the general contractor’s safety director should be consulted if a subcontractor doesn't meet standards. Standard operating procedures for vetting subcontractors provide checklists that can help GCs understand and mitigate any weaknesses in the planning and contractual arrangements in the contracts.
If a subcontractor is in a weaker financial position, with working capital below the tolerances established by the GC’s metrics, the GC can mitigate that risk by paying directly or with joint checks for materials or labor when they draw up the contract terms.
2. Airtight Contracts
Ensure that contracts contain the correct legal language and scopes of work for each subcontractor.
Liability should transfer down to subcontractors, and indemnification should transfer up to the general contractor and then to the owner. This contractual risk transfer makes the appropriate parties responsible for their work and acts as a risk-sharing mechanism for general contractors. The language in the contract needs to comply with relevant laws and specify the mechanisms that trigger indemnification or liability.
The scope of work in subcontracts should exactly match the main contract so that the subcontractor will deliver precisely what the owner expects. However, when soliciting bids from subcontractors, their expertise can cause changes in the scope that should transfer back up to the main contract.
For example, a plumbing contractor may notice a 3-inch main in the spec with an expectation of 20 psi of pressure on the 15th floor, yet that contractor knows a 4-inch main will be required to get the desired water pressure.
This may mean changing the architectural plans, as there will need to be more clearance in the walls to accommodate the larger main. Making this change in the scope at the contract stage will save rework and extra costs later.
3. Insurance and Bonds
Insurance and surety bonds can help mitigate risk, but the details matter.
Ensure that the subcontractor’s insurance aligns with the limits and scope of work required by the contract. Experts should vet the language in the insurance and the contract to ensure that both are appropriate. For instance, a roofing contractor with insurance containing a height exclusion for work done above 8 feet would be problematic.
The general contractor can require the subcontractor to obtain performance or payment bonds. Another option is for the GC to purchase subcontractor default insurance. Not all owners are willing to cover these expenses.
4. Managing Performance
Just as in vetting the subcontractor, the general contractor needs a system and standard operating procedures to monitor every phase of the project to manage subcontractors to ensure fulfillment of the contract terms.
- Establish a process with a system of record that keeps both GC and subcontractor employees on the same page throughout the process, from bidding through closeout.
- During preconstruction, schedule realistically rather than optimistically so there is some wiggle room to account for minor hitches during construction.
- Once in the construction phase, the superintendent should perform two or more daily jobsite walks, keep daily logs with checklists, and have a notification tree ready to keep project managers, executives and subcontractors in the loop about any changes or issues.
- Tracked communication can keep the overall project on schedule even if issues onsite necessitate schedule changes. If one trade gets behind or material deliveries get delayed, schedulers can find ways to expedite specific trades at relatively lower costs to make up for lost time.
5. Focusing on Collaboration
Subcontractors are vital partners for general contractors on any construction project. Experienced trade partners' expertise can help avoid more significant problems, and working collaboratively will produce a smoother process.
Technology that includes detailed scheduling and specifications can facilitate internal and external open communication, keeping all stakeholders informed. Developing good working relationships with subcontractors and using them on multiple projects provides familiarity and fosters stronger collaboration.
Consider contract terms for payment of subcontractors that avoid a moral hazard. While general contractors are responsible for negotiating payment from the owner, the subcontractor may have long since completed their work.
Pay-when-paid clauses incentivize subcontractors to shift their focus to a different project with faster payment terms. General contractors who pay when the subcontractor has completed their work have an advantage in attracting and retaining capable subcontractors.
Treating subcontractors with respect, providing fair payment, and providing feedback in honest discussions with the subcontractor’s principals allows a GC to maintain positive relationships with quality subcontractors who can become partners on future projects.
Combining Insurance and Oversight to Manage Risk
Insurance and surety bonds can mitigate financial risks, but managing subcontractor risks with oversight can help general contractors avoid the need to file a claim. Standard operating procedures, clear communication, and follow-through by all stakeholders can keep subcontractor performance on track and minimize the risks involved in partnerships with multiple trades to complete a project.
Keeping all the components of subcontractor relationships functioning smoothly supports successful project completion and protects the general contractor’s reputation.
Was this article helpful?
Thank you for your submission.
100%
0%
You voted that this article was . Was this a mistake? If so, change your vote here.
Scroll less, learn more about construction.
Subscribe to The Blueprint, Procore’s construction newsletter, to get content from industry experts delivered straight to your inbox.
By clicking this button, you agree to our Privacy Notice and Terms of Service.
Thank you!
You’re signed up to receive The Blueprint newsletter from Procore. You can unsubscribe at any time.
Categories:
Tags:
Written by
David Farino
Technical Brokerage Officer | Procore
David Farino is a Technical Brokerage Officer at Procore Technologies. He brings over a decade of experience in the construction and insurance sector to his position, including roles as Assistant VP and Vice President of Construction and Infrastructure at NFP and Senior Underwriter at Arch Insurance Group, Inc. David received his BBA in Business Administration and Management from Hofstra University. He is based in New York City.
View profileJulia Tell
Contributing Writer
55 articles
Julia Tell is a freelance writer covering education, construction, healthcare, and digital transformation. She holds a Ph.D. in Media & Communications and has written for publications including Business Insider, GoodRx, and EdSurge, as well as nonprofits, international businesses, and educational institutions.
View profileExplore more helpful resources
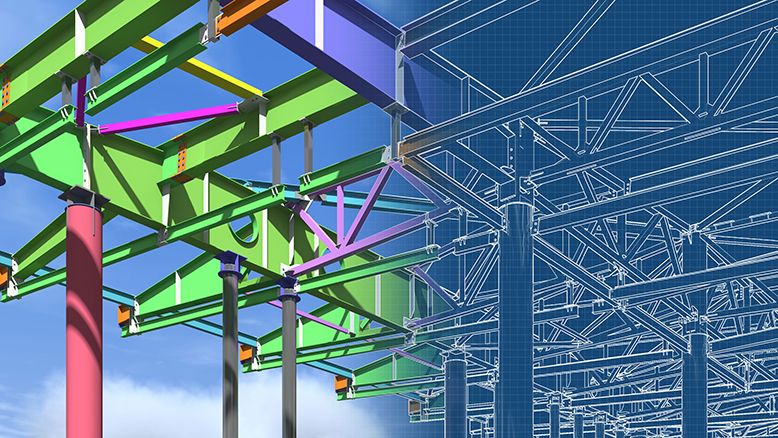
BIM’s Role in Risk Mitigation: Strategies for Success
Building information modeling (BIM), has been touted as a way to deliver a broad range of wins on any construction project. It supports stronger planning and smoother collaboration. It provides...
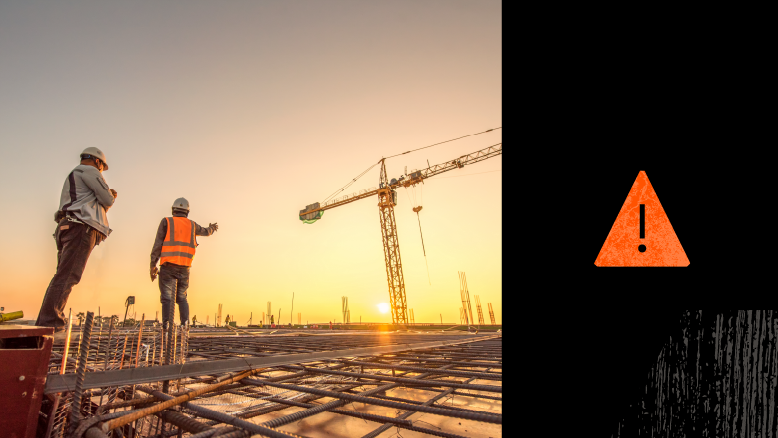
Risky Business: Transforming Risk Mitigation into Risk Prevention
Risk burrows into every aspect of construction — costs, safety, labor, scheduling, profitability and even market leadership. In an inherently dangerous industry, risk is inevitable, but truly powerful risk mitigation doesn’t...
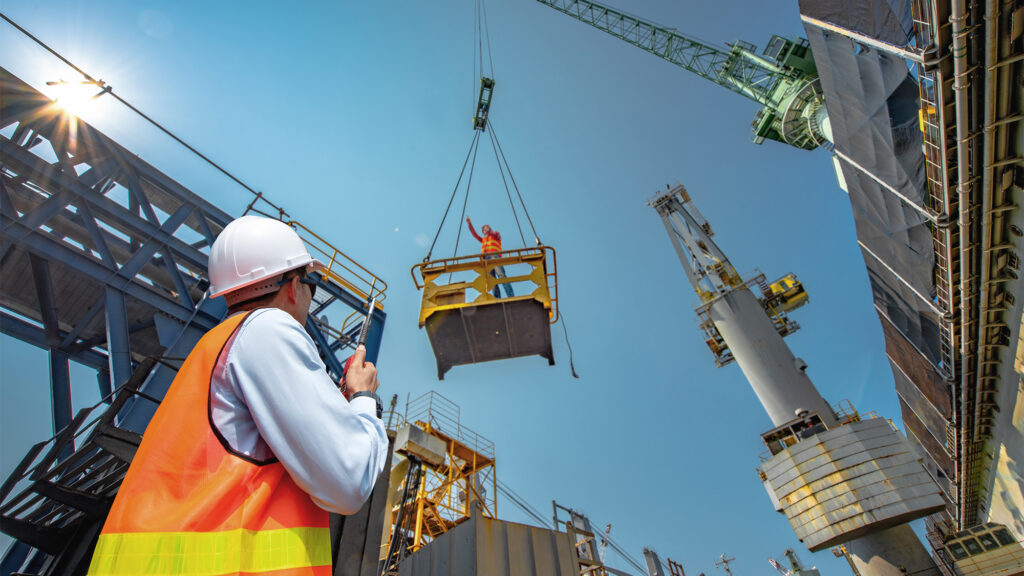
Using AI to Manage Risk in Construction
Since the day construction became an industry, many people have been trying to manage the risks of building things — to identify and mitigate potential conditions that might impact a project’s...
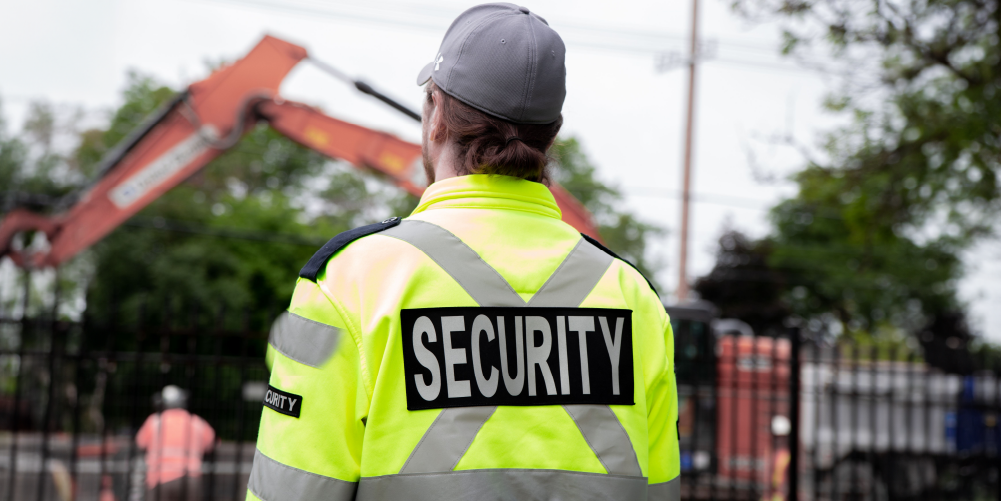
Jobsite Security: Assessing and Minimizing Construction Site Risks
Assessing security needs for a construction site early can save time and money and avert potential complications later on the project. Security on a jobsite mitigates risks by protecting the area...
Free Tools
Calculators
Use our calculators to estimate the cost of construction materials for your next project.
Templates
Find a template to help you with your construction project tasks.
Material Price Tracker
Get the latest U.S. retail prices and view historical trends for common building materials.
Glossary
Explore key terms and phrases used in the industry.