— 10 min read
Prefab Construction: The Risks and Rewards of Prefabrication
Last Updated Aug 13, 2024
Makenna Ryan
Civil & Infrastructure Solutions Engineer
Makenna Ryan is a Solutions Engineer at Procore. Prior to joining Procore, he spent seven years at McDermott International Inc. as a construction Manager and Senior Equipment Engineer. He also spent three years as a Project Engineer at Subsea7. Makenna received his B.S. in Mechanical Engineering and Technology from Texas Tech University. He is based in the Houston area.
Cait Bladt
13 articles
Cait Bladt is a multi-award winning freelance writer and producer. Her work has appeared at Vice, ABC News and Rolling Stone among others. She currently lives in Brooklyn with her cat Patricia.
Last Updated Aug 13, 2024
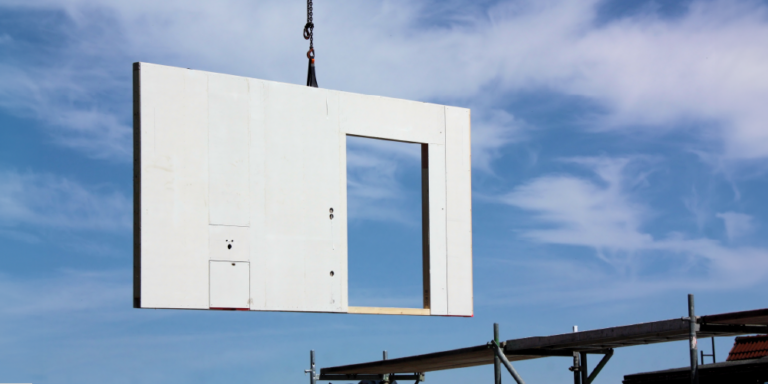
Prefabricated or “prefab” construction is similar to assembling a set of Lego blocks: Components are manufactured or assembled at a separate location and then assembled on-site. Compared with the traditional building approach, where raw construction materials are delivered to the jobsite and assembled piece by piece, prefabrication can offer substantial advantages.
Embracing prefab technology can mitigate risk and diminish uncertainties within any given construction project. By adopting this approach, contractors can reduce the impact of inclement weather conditions and other factors that delay the project timeline.
In this article, we’ll explore common use cases for prefabrication on different project types and how prefab construction offers contractors increased reassurance and control over their schedules.
Table of contents
The Basics of Prefabrication
On a traditional build, materials are delivered to the jobsite, where they are cut, formed and fastened according to the specifications and site conditions. Consider a wood-framed building: Framing is often one of the most time-consuming phases of the build. A material supplier delivers a pallet of 8-foot-long 2-by-4s to the jobsite (which must be stored and protected from excess moisture until the framing contractor is ready to begin work).
After the foundation cures, they begin assembling wall frames, one stick at a time, and securing them to the pad and each other. They will often need to trim 3 inches off of each stud to account for the top and bottom plate of the wall frame.
Prefabricating wall frames and installing them on-site can shave weeks or months off of the schedule. A fabricating contractor can build the wall frames to match every detail in the designs and specs. On the day the concrete pad is ready, the fabricator can deliver the pre-built frames to the jobsite, and the GC or their subcontractor can put the pieces together. Depending on the size of the project and the crew, this can be accomplished in as little as a half day.
Common Prefab Components
The construction industry has long used prefabricated components to build a variety of project types, including healthcare, commercial, and industrial projects.. Homebuilders and heavy civil contractors alike use prefab materials to simplify and streamline project delivery. These are some of the most common prefabricated components:
- Roof and floor trusses: On residential and commercial projects, roof and floor trusses must be engineered to ensure they provide adequate structural support. These can be designed for specific load-bearing requirements and are ready to install upon delivery.
- Wall panels: Including interior and exterior walls, these panels can come pre-insulated. Fabricators can even pre-install windows and doors, and deliver the panel with finishes applied.
- Staircases and railings: Pre-constructed to fit specific building codes and design specifications, prefab stairs are ready to be anchored in place upon arrival.
- Bridge components: On bridge projects, common prefabricated components include beams, girders, deck segments, and pier caps, which are manufactured offsite and transported to the bridge location for assembly.
- Culverts and drainage systems: Prefab items in water and wastewater projects include concrete pipes, boxes, and other drainage structures that are essential for managing water flow around highways and other infrastructure.
- Steel framing: Prefabricated steel structures for use in buildings and infrastructure can be bolted or welded at the construction site.
- Modular pavement systems: On road and highway projects, refabricated sections of pavement can be quickly assembled to create durable driving surfaces.
Advantages of Prefab Construction
While prefabrication offers a clear advantage when it comes to schedule management, it offers an array of other benefits to both the contractor and the owner.
1. Logistics
Prefabrication significantly enhances site logistics by streamlining the construction process, particularly on jobsites with limited space. Since prefabricated components are manufactured in controlled factory environments, the need for on-site storage of raw materials is drastically reduced. These components can be delivered just in time for installation, thus minimizing the duration and extent of on-site material handling and storage.
This just-in-time delivery model is particularly beneficial for urban construction sites, where space is at a premium and the storage of excess materials can impede traffic flow and increase safety hazards.
Furthermore, the immediate installation of prefabricated elements upon arrival not only accelerates the overall construction timeline but also reduces the environmental impact of material waste. The reduction in on-site activity correlates with fewer disruptions to the surrounding community and a more organized and efficient jobsite.
2. Precision
Prefabrication generally improves the precision of both the manufactured item and the installation. Building elements in a factory with finely-tuned equipment allows for greater control over measurements and tolerances, ensuring each component is produced to exact specifications and with uniform quality.
Design tools (e.g. CAD and BIM) and manufacturing technologies further enhance this accuracy, reducing human error and material discrepancies. This meticulous attention to detail guarantees that the components fit together seamlessly during installation.
On the jobsite, prefabrication frequently translates to quicker and more accurate installation processes, as all parts are designed to connect perfectly. This means that not only are the elements built with superior precision, but they are also installed with a level of accuracy that traditional on-site construction methods struggle to achieve. The result is an overall increase in the quality of the finished structure, with reduced need for adjustments and rework.
3. Risk Management
In construction, risk management often boils down to controlling variables — and prefabrication offers the ability to control nearly every variable in the construction of the element being fabricated. By shifting the construction of components — such as pipes, joints, or entire modules — from the often unpredictable job site to the predictable confines of a factory or warehouse, prefabrication allows for a more methodical approach.
Notably, the timeline for component construction becomes more reliable, and quality checks can be conducted more thoroughly in a dedicated facility. With prefabrication, most of the construction risks associated with weather, site conditions, and labor variables are mitigated well before the components reach the building site. These proactive measures ensure that potential problems are identified and resolved in advance, reducing the likelihood of costly and time-consuming issues arising during the crucial stages of on-site assembly.
4. Speed
Prefab construction can greatly accelerate the construction process, virtually eliminating delays caused by adverse weather conditions or the need for specific environmental settings for materials like concrete. Moreover, the ability to conduct comprehensive testing and refine aesthetic details within a factory setting ensures that components arrive on-site in a state of near perfection, ready for immediate assembly.
By front-loading the production and quality assurance phases, prefabrication also allows for parallel site preparation, further expediting the overall build time. The culmination of these factors is a streamlined construction process where speed is matched by an uncompromised commitment to quality.
5. Labor Efficiency
One of the most significant benefits of prefab construction is the ability to maximize labor efficiency. By bringing together specialized labor in a controlled setting, construction teams can focus on precision and quality without the distractions and variables found at traditional construction sites. This not only improves the quality of work but also enhances safety and reduces overall project costs, allowing specialists to focus on their craft.
Stay updated on what’s happening in construction.
Subscribe to Blueprint, Procore’s free construction newsletter, to get content from industry experts delivered straight to your inbox.
Gain industry expertise, stay ahead of the curve
Explore valuable insights into the latest construction trends and project management best practices.
Subscribe to the newsletterGain industry expertise, stay ahead of the curve
Explore valuable insights into the latest construction trends and project management best practices, and learn how Procore's platform can optimize your projects.
Subscribe to the newsletterRequest a demo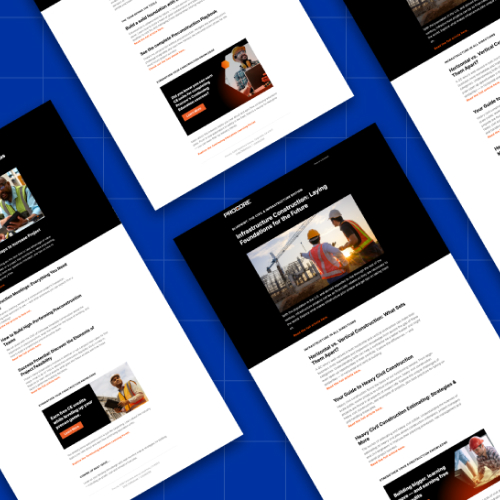
The Risks of Prefab Construction
While prefab construction offers a number of advantages to a more traditional building approach, it is not without risk. Prefabrication requires careful planning and consideration of all risks to fully realize the benefits.
1. Interface Management
One of the critical aspects of prefab construction is interface management — the process of ensuring that prefabricated components from different production sites fit together perfectly upon assembly. A reusable water bottle is a simple example: The plastic lid and aluminum body are manufactured in different locations, but must screw together precisely to form a watertight seal.
Some materials are more forgiving when it comes to misaligned connection points (e.g. wood vs. steel). Regardless of the material, prefabrication requires meticulous planning and precision engineering to avoid costly on-site adjustments. Successful interface management eliminates potential errors in manufacturing and is pivotal in maintaining project timelines and budgets.
2. Liability
Determining liability can be a challenge in prefab construction, particularly when issues arise from interface management discrepancies. The responsibility for components that do not seamlessly integrate — whether due to fabrication flaws or misalignment on the jobsite — should be clearly defined by the contractual agreements. It is important for all parties involved, from the general contractor to the modular fabricator, to understand where liability rests for each element of the project.
Contracts must clearly outline responsibility for defects or mismatches, ensuring that parties are aware of their obligations and potential liabilities from the outset. In industries such as oil and gas, it is common for the general contractor to assume the bulk of the risk. This centralized liability model ensures accountability but also empowers the contractor to factor this risk into their pricing structure.
By proactively managing contracts and liabilities, prefab construction can maintain its efficiency advantage while assuring equitable risk distribution among stakeholders.
3. Transportation & Storage
The transportation and storage of project components is often the greatest limitation to prefab construction. Virtually anything can be prefabricated with the right equipment, sufficient space and adequate infrastructure to transport it.
Addressing the unique challenges of transporting oversized components, such as wind turbine blades or bridge sections, requires careful planning and coordination. Whether it's navigating through urban areas or ensuring marine vessels are adequately sized, the success of a prefab project can be credited to logistics as much as the actual construction.
For example, the average prefabricated blade for a wind turbine is about 120 feet long. That is more than double the length of a typical tractor tailor, which is already difficult to navigate through turns in many suburban areas. Transporting an item of this size requires specialized route planning, considering the increased turning radius and weight of the item.
Often, the limitations of prefabrication are due to restraints in both manufacturing and transportation. In the oil and gas industry, prefabrication for an oil rig is limited by the size of the ship, which is limited by the size of the port.
If an item is being carried across a bridge, will it support the weight? If it has to be hoisted into place, is the crane powerful enough to get it there? These are the types of questions that need to be answered before committing to a specific prefab project.
4. Design Changes
If there’s one thing that is virtually guaranteed on any construction project, it’s change. Whether due to differing site conditions, material availability or design considerations, even small changes can render prefabricated components unusable.
Prefabricated components are manufactured based on design specifications and site assessments. As a result, any discrepancies between the expected and actual site conditions can lead to complications. For instance, unusual soil characteristics or subterranean obstructions may require on-the-fly adjustments to prefabricated foundation elements. Similarly, design changes made after the commencement of prefab production can lead to costly rework or even render existing components unusable if they no longer align with the revised design.
To mitigate these risks, stringent design freeze policies are often implemented, alongside thorough and regular site evaluations before production begins. In addition, modular construction offers some flexibility to accommodate minor alterations through standardized connection points.
Despite these challenges, the key to successful prefab construction lies in diligently managing the design phase and ensuring comprehensive site analysis to prevent expensive and time-consuming setbacks.
Improving Coordination in Prefab Construction
Prefab construction requires a high degree of coordination and close communication between the design, fabrication, and construction teams. The use of construction management software on prefab projects can be a game-changer for project managers, from logistics planning to on-site execution.
A digital platform provides a centralized hub for all project data and communication, from managing drawings and coordinating with contractors to tracking critical milestones. By leveraging technology, project managers can better mitigate the risks and take full advantage of the benefits prefabrication has to offer.
Was this article helpful?
Thank you for your submission.
67%
33%
You voted that this article was . Was this a mistake? If so, change your vote here.
Scroll less, learn more about construction.
Subscribe to The Blueprint, Procore’s construction newsletter, to get content from industry experts delivered straight to your inbox.
By clicking this button, you agree to our Privacy Notice and Terms of Service.
Thank you!
You’re signed up to receive The Blueprint newsletter from Procore. You can unsubscribe at any time.
Categories:
Written by
Makenna Ryan
Civil & Infrastructure Solutions Engineer | Procore
Makenna Ryan is a Solutions Engineer at Procore. Prior to joining Procore, he spent seven years at McDermott International Inc. as a construction Manager and Senior Equipment Engineer. He also spent three years as a Project Engineer at Subsea7. Makenna received his B.S. in Mechanical Engineering and Technology from Texas Tech University. He is based in the Houston area.
View profileCait Bladt
13 articles
Cait Bladt is a multi-award winning freelance writer and producer. Her work has appeared at Vice, ABC News and Rolling Stone among others. She currently lives in Brooklyn with her cat Patricia.
View profileExplore more helpful resources
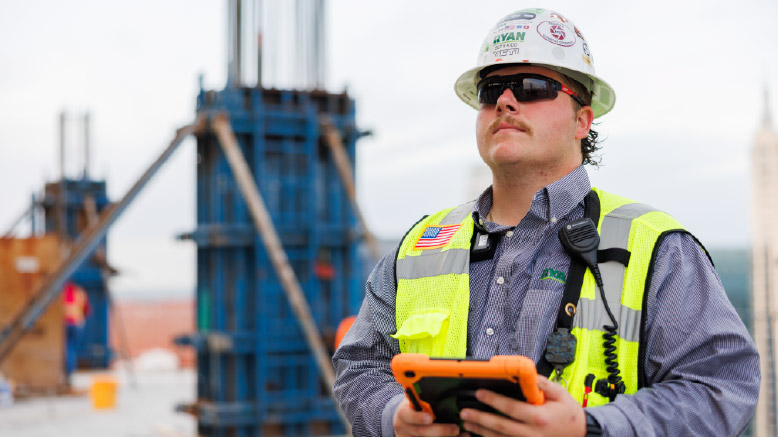
What Does a Construction Manager Do? A Guide to Roles and Responsibilities
A construction manager is central to the success of any building project. This professional oversees all on-site operations to make sure the jobsite runs safely and efficiently. Construction managers guide...
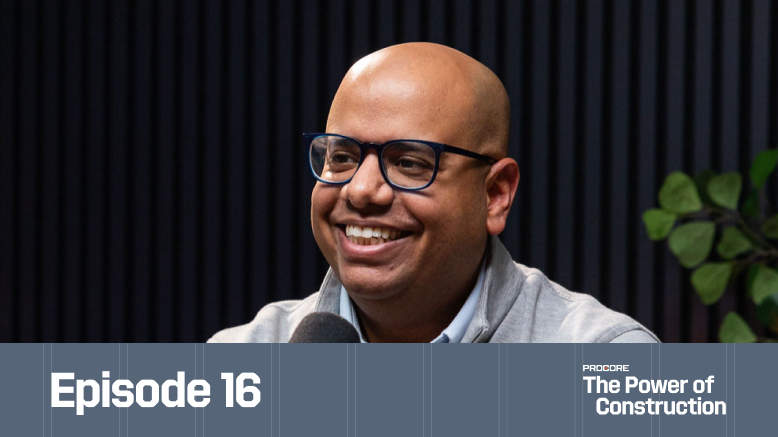
Will AI Replace ‘Paperless Builders’—or Redefine Them?
How can artificial intelligence enhance rather than replace human expertise in construction? In Episode 16, Hamzah Shanbari, Director of Innovation at Haskell and author of “The Paperless Builders,” reveals how...
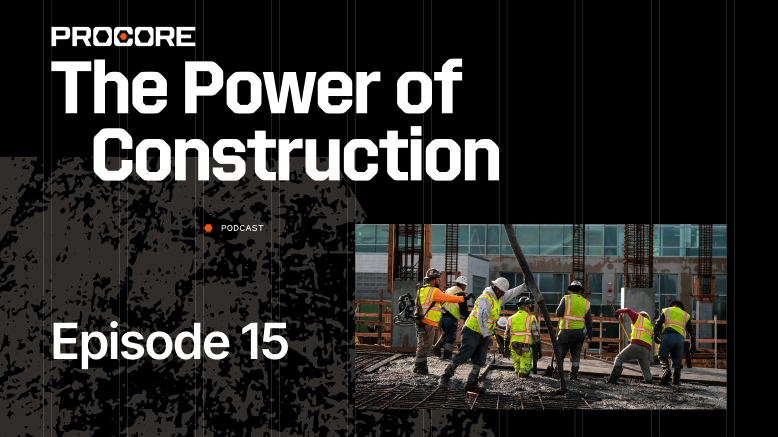
Has Construction Tech Failed its Most Important Customer?
In episode 15 of The Power of Construction, we tackle a provocative question: Has construction technology actually failed building owners? Despite billions in investment, owners report that BIM automation and...
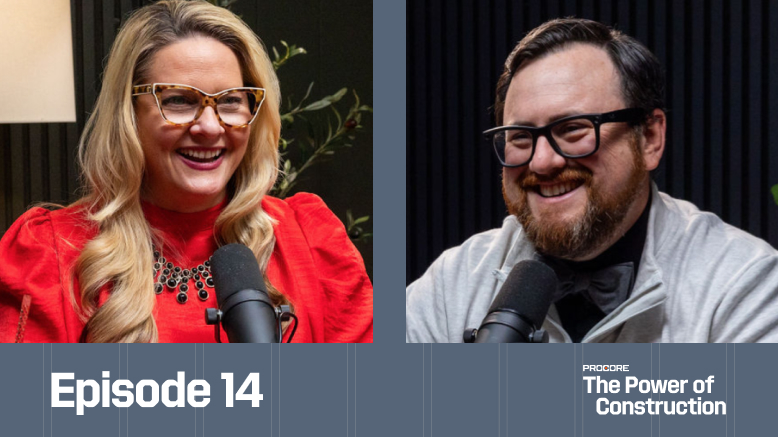
Is Construction Ready for the Future?
In episode 14 of The Power of Construction, we ask a critical question: Can an industry tasked with building our future truly meet the demand to double its growth by...
Free Tools
Calculators
Use our calculators to estimate the cost of construction materials for your next project.
Templates
Find a template to help you with your construction project tasks.
Material Price Tracker
Get the latest U.S. retail prices and view historical trends for common building materials.
Glossary
Explore key terms and phrases used in the industry.