— 10 min read
From Concept to Reality: Prefabricating a Breakthrough in Construction
Last Updated Jul 17, 2025
Will Cotten
RNGD Prefab Leader
Will Cotten is the leader of RNGD Prefab, a subsidiary of RNGD, which exists to advance the construction industry forward. RNGD Prefab is a team of fabricators and craftsman who adhere to a True Builder philosophy and are implementing prefabrication deliveries, building in-house data analytics, and adopting innovative technologies. Previously as RNGD's Innovation Leader, Will Cotten incubated emerging teams, lead technology strategy, and augmented the company’s capabilities — implementing new technology and supporting the development of in-house construction analytics and prefabrication capabilities. In all his roles, Will enables RNGD to find and apply innovative solutions that advance the company’s overall mission of “building a better world.” Drawn to the firm's unparalleled drive, exemplified by a values-oriented band of team members, Will joined RNGD in 2018 as a Commercial Operations Intern. Since then, his ingenuity and unique insight have enabled him to rise to the occasion in new positions and deliver on strategic initiatives. A native of Prairieville, Louisiana, William earned his degree in Construction Management from Louisiana State University. His work ethic has revolved around the ethos of “actions not words.” He applies that same mentality as a board member for the Palmisano Foundation. He was also recognized as 2022 BuiltWorlds Leader of Tech Adoption. Aside from spending time with family and friends, William indulges in a love for nature and the human experience. He indulges in content on evolutionary biology, human psychology, philosophy, spirituality, and has a soft spot for New Orleans history. And when he’s not in the office, you’ll likely find him outdoors — on a long walk, golfing, hiking, camping, even gardening and cutting the grass. Will was named to the 2022 BuiltWorlds Adoption Top 50 List. The people within this list are all leading the way towards innovation for their companies and the industry overall.
James Hamilton
Writer & Producer
75 articles
James Hamilton is a writer based in Brooklyn, New York with experience in television, documentaries, journalism, comedy, and podcasts. His work has been featured on VICE TV and on The Moth. James was a writer and narrator for the show, VICE News Tonight, where he won an Emmy Award and was nominated for a Peabody Award.
Last Updated Jul 17, 2025
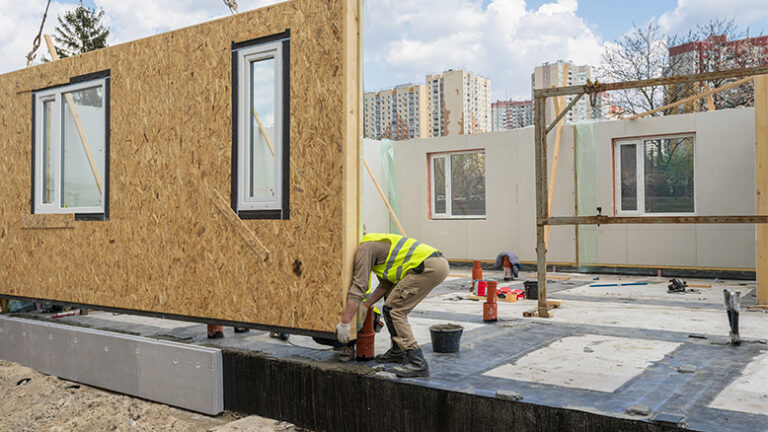
It’s been said countless times that a construction project can deliver on two — but rarely all three — of the following: high quality, speed and low cost. RNGD, a contractor with offices in Louisiana, Tennessee and Alabama, recognized that breaking this tradeoff would require a fundamentally different approach.
Determined to challenge the status quo, RNGD embarked on a journey of research, industry engagement, data analysis, and creative problem-solving. That journey led them to offsite fabrication — and eventually, to a broader, more ambitious vision: reimagining prefabrication as a pathway to delivering buildings as a product.
This article explores operational efficiency through the lens of how prefabrication became a cornerstone of a strategy for RNGD, designed to achieve speed, quality and cost control simultaneously.
Table of contents
Prefab: The Basics
Since its founding in New Orleans, LA 12 years ago, RNGD has been committed to becoming a true builder, capable of self-performing scopes of work and creating more value for clients/projects than just managing trade risk. It was built with the mission to challenge industry norms to improve construction practices. This ethos is what originally led RNGD to prefabrication (prefab), the practice of manufacturing and assembling components at a separate location and then bringing them onsite, where minimal work is required before installation.
RNGD was drawn to prefabrication because it aligned with the values and commitments the company had already embraced. For instance, the contractor had been actively working to reduce transactional waste — estimated to account for 30–40 percent of total project costs. In parallel, RNGD was committed to simplifying the construction process for all stakeholders involved. Prefabrication emerged as a natural solution, offering a practical path toward greater efficiency and clarity across the project lifecycle.
Some of the benefits of manufacturing and assembling components offsite include:
Controlled Work Environment
Providing controlled work environments can lead to increased worker safety and decreased work interruptions.
Fewer Labor Hurdles
Offsite construction of certain elements can help overcome labor issues by creating more predictable, stable amounts of work and decreasing the need for specialization.
Enhanced Precision
Precise material fabrication using advanced manufacturing principles, automation & CNC technology can reduce material waste and environmental impact.
Simplified Planning
Prefab can aid in construction planning through just-in-time delivery and increased control over resource production.
Boosted Speed
Offsite fabrication can help increase project speed, drive down costs and improve quality reliability, through increased control over resources and planning.
More Independence
Using more prefabricated elements can help decrease reliance on complex supply chains, which in turn can reduce costs and help avoid delays.
Like many contractors who turn to prefab, RNGD initially began by partnering with external manufacturers that prefabricated various components they needed. Early on, these external relationships are common, because creating a successful prefabrication operation requires:
- Significant financial investment
- Appropriate leadership
- Enough space for a full manufacturing facility
- Enough business and demand to ensure consistent throughput
But over time, RNGD saw that solely partnering with prefab manufacturers wasn’t going to be enough to achieve its mission of challenging industry practices.
For true transformation, it needed to double down into being what it calls a “true builder,” a contractor that controls as many aspects of its construction process as possible.
'Doing It Yourself' With Prefabrication
About two years ago, RNGD established a production facility in Metairie, Louisiana, where it manufactures structural steel and cold-form steel elements, which serve as the structural backbone of its productized delivery.
Structural steel is used to create buildings’ superstructures, including load-bearing elements of the core framework. Cold-form steel can also be used for load-bearing superstructures; however, it is also used to produce panelized components, such as interior and exterior wall panels.
By producing these critical elements in-house, RNGD positioned itself to construct and dry-in entire superstructures independently. Standardizing these processes has enabled greater control over efficiency, cost, and quality across its projects.
RNGD faced a strategic decision between two common approaches to prefabrication:
- Kit of parts: This involves designing buildings with standardized components that can be flat packed and assembled on-site. Components are often panelized, such as wall panels or floor systems. Panelized components are usually easier to ship and allow for greater design flexibility and customization.
- Volumetric modular approach: This method involves building entire modules or building sections. Modules are fully constructed in a factory setting and are then transported to the site for installation. This approach can be very efficient in terms of time and labor, as modules require minimal on-site work. However, the trade-off is reduced design flexibility due to the high degree of standardization. Additionally, this method demands substantial factory space to fabricate and store the completed modules.
In the end, RNGD chose the kit-of-parts approach. This decision reflected the contractor’s desire to maintain autonomy over operational efficiency while still allowing each building to be uniquely tailored to its site and client.
By standardizing the production of the structural framework and certain façade elements, RNGD could drive consistency and efficiency while controlling costs — all without sacrificing the ability to deliver distinctive architectural details and high-quality interior and exterior finishes that elevate the final product.
A Commitment to Great Data
If creating prefabrication capabilities is about improving operational efficiency, RNGD needed to consistently and reliably measure how the process was impacting timelines, budgets and quality. Data needs to be gathered and analyzed to identify bottlenecks, optimize processes and make informed decisions.
RNGD’s approach to data was comprehensive and required a commitment from every team member and stakeholder, including people working the prefab facility floor, teams working in the field and leadership.
In order to truly weave data-driven decision making and execution into every part of its operation, RNGD got creative with how it used, analyzed and displayed data, which included:
Leveraging QR Code and Location Features
RNGD attached QR codes to individual components, such as a wall panel or a window system, and tracked its movement through the workflow and between locations. This created data that detailed cycle times down to seconds and minutes. RNGD was able to see how long elements took to create, how the process could be improved and exactly the point that breakdowns occurred.
Using the Inspection Feature to Create QC Checklists
Checklists require sign-off from the shop foreman with timestamps of when the product moves from one station to the next. This meant every component was tracked for quality, providing data on breakdowns and potential issues.
Creating Dashboards
The team leveraged data features to create dashboards that tracked key performance indicators (KPIs) in almost real-time.
Integrating Data Analysis
RNGD integrated data analysis into morning team huddles and other team meetings as a way to constantly engage with performance and cultivate a culture of continuous improvement, open feedback, curiosity and enthusiasm.
Courses about construction.
For construction.
Unlock your career potential with our free educational courses on Health & Safety, Data in Construction, and more.
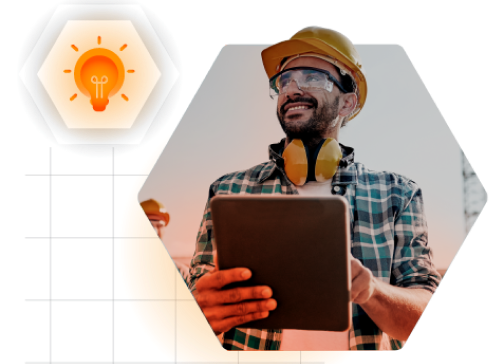
Realizing the Potential of Prefabrication
While RNGD is still in the early stages of its journey into prefabrication and productized building delivery, the impact on operational efficiency is already becoming clear.
- Project timelines have decreased by 30%, due to the increased speed of onsite installations as well as higher quality work reducing the need for rework.
- Data suggests cost savings will be in the range of 5 to 10%.
When we produce a cold-form steel or structural steel component or product, we are maximally reducing, to fully eliminating, any waste associated with that product. So for an exterior wall panel, for instance, we’re going to precision CNC (Computer Numerical Control) roll and cut every cold form steel metal stud in that panel to where there’s no waste associated with it. We’re decoiling it, rolling it, punching it, dimpling it and then it’s coming out of the end pre-cut to link, pre-dimpled and ready to be attached as that panel product.
You compare that to conventional methodology where the trade partner will get that product from a supplier who will get that from a manufacturer who is not cutting everything exactly to length. Not only do you have the added trucking from manufacturer to supplier, transactional fees from supplier to trade partner and then to the jobsite, but then you also have the added waste of material drops and debris on site.
Will Cotten
RNGD Prefab Leader
RNGD
RNGD is seeing its investment pay off in other ways, as well.
The clarity and regularity of data has allowed RNGD to identify and solve problems with a precision that was previously impossible.
For example, the contractor discovered that a waterproofing station for wall panels was a bottleneck because it required additional coats of a waterproofing solution to meet standards. This led RNGD to find a product that integrated waterproofing into the sheathing board, which addressed the bottleneck and sped up the production process.
That single change transformed our workflow. What was once our biggest bottleneck is now the fastest-moving station in the shop. We’ve gone from producing 3.5 to 4 fully finished panels per day to nearly 8 — a dramatic increase in output driven by a simple but strategic observation.
Will Cotten
RNGD Prefab Leader
RNGD
RNGD’s approach to data allows it to be extremely pointed in analyzing performance. It can measure the production of something as small as fastening components, ensuring each part is completed as effectively as possible. It’s also able to precisely measure cycle times which helps to improve performance and identify problems.
Additionally, RNGD’s prefab facilities mean it can offer a work environment that is safer, more consistent and more predictable than a traditional construction jobsite. This has helped it attract a broader range of workers that might not have otherwise been drawn to construction, such as recent high school graduates or military veterans.
Overcoming Common Challenges in Prefab
Pro Tip
If you want to take a building and standardize its core components and deliver faster at a higher quality and a better price point, you have to make that decision from day one. Early integration—especially at the conceptual design stage—not only enables you to capture the full benefits of prefabrication, but also preserves the freedom to customize architectural features.
Transitioning to prefabrication brings a unique set of challenges. One of the most pressing is the need for consistent production throughput — essential for maintaining profitability and labor continuity in a prefab facility.
To address this, RNGD continually works to build a steady pipeline of future projects, which often includes reintroducing clients and partners to the true potential of prefabrication.
Many still associate prefab with bland, repetitive design, so part of RNGD’s mission is to demonstrate that prefab can be both highly efficient and architecturally compelling.
Another key strategy for maintaining throughput has been developing in-house projects. By acting as both builder and developer, RNGD can stabilize production demand while also using these projects as incubators for new assemblies, processes, and ideas — testing them in real-world conditions before bringing them to market with external partners.
Success in prefabrication also requires rethinking the entire construction process. Projects must be planned with prefab in mind from the very beginning — ideally during the conceptual or schematic design phase.
For RNGD, launching its prefab operations meant shifting toward an Integrated Project Delivery (IPD) model. IPD promotes early and ongoing collaboration by aligning incentives, risks and rewards across all stakeholders.
An Even Brighter, Prefabricated Future
RNGD has gained valuable insight into the benefits of prefabrication from both the contractor’s and owner’s perspectives. One of the first buildings constructed using RNGD’s prefabricated components was its own campus headquarters — a testament to the company’s confidence in its evolving processes.
The key to RNGD’s success so far has been a steadfast commitment to continuous learning, adaptation and improvement. This commitment fuels a virtuous cycle of innovation: data drives smarter decisions, which generate better data, enabling ongoing refinement and growth.
RNGD has also created strong relationships with other prefab manufacturers to supplement its offerings with elements it does produce in-house. Meanwhile, RNGD’s meticulous, thoughtful approach has created exciting opportunities to expand its prefabrication capabilities.
Currently, RNGD’s prefab model is proven and optimized for corporate office buildings, but the company is actively working to expand its product portfolio. This includes developing additional components and exploring new building types — such as living and lodging spaces — that continue to deliver on its three core pillars: cost-effectiveness, timeliness and uncompromising quality.
Was this article helpful?
Thank you for your submission.
0%
0%
You voted that this article was . Was this a mistake? If so, change your vote here.
Scroll less, learn more about construction.
Subscribe to The Blueprint, Procore’s construction newsletter, to get content from industry experts delivered straight to your inbox.
By clicking this button, you agree to our Privacy Notice and Terms of Service.
Thank you!
You’re signed up to receive The Blueprint newsletter from Procore. You can unsubscribe at any time.
Categories:
Tags:
Written by
Will Cotten
RNGD Prefab Leader | RNGD
Will Cotten is the leader of RNGD Prefab, a subsidiary of RNGD, which exists to advance the construction industry forward. RNGD Prefab is a team of fabricators and craftsman who adhere to a True Builder philosophy and are implementing prefabrication deliveries, building in-house data analytics, and adopting innovative technologies. Previously as RNGD's Innovation Leader, Will Cotten incubated emerging teams, lead technology strategy, and augmented the company’s capabilities — implementing new technology and supporting the development of in-house construction analytics and prefabrication capabilities. In all his roles, Will enables RNGD to find and apply innovative solutions that advance the company’s overall mission of “building a better world.” Drawn to the firm's unparalleled drive, exemplified by a values-oriented band of team members, Will joined RNGD in 2018 as a Commercial Operations Intern. Since then, his ingenuity and unique insight have enabled him to rise to the occasion in new positions and deliver on strategic initiatives. A native of Prairieville, Louisiana, William earned his degree in Construction Management from Louisiana State University. His work ethic has revolved around the ethos of “actions not words.” He applies that same mentality as a board member for the Palmisano Foundation. He was also recognized as 2022 BuiltWorlds Leader of Tech Adoption. Aside from spending time with family and friends, William indulges in a love for nature and the human experience. He indulges in content on evolutionary biology, human psychology, philosophy, spirituality, and has a soft spot for New Orleans history. And when he’s not in the office, you’ll likely find him outdoors — on a long walk, golfing, hiking, camping, even gardening and cutting the grass. Will was named to the 2022 BuiltWorlds Adoption Top 50 List. The people within this list are all leading the way towards innovation for their companies and the industry overall.
View profileJames Hamilton
Writer & Producer
75 articles
James Hamilton is a writer based in Brooklyn, New York with experience in television, documentaries, journalism, comedy, and podcasts. His work has been featured on VICE TV and on The Moth. James was a writer and narrator for the show, VICE News Tonight, where he won an Emmy Award and was nominated for a Peabody Award.
View profileExplore more helpful resources
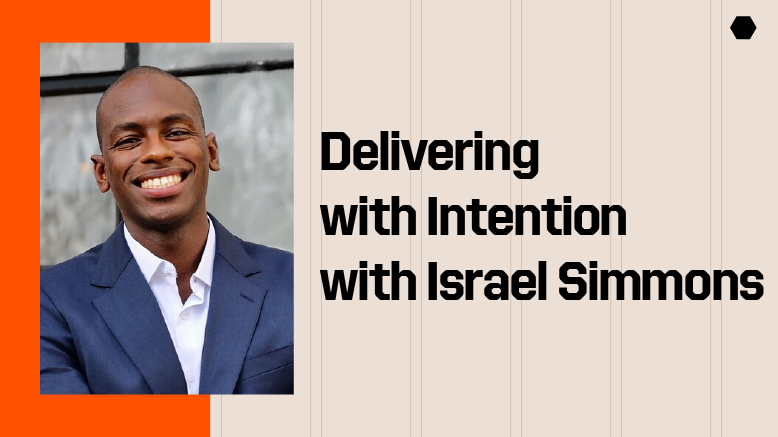
Delivering with Intention: Leadership Lessons from Israel Simmons on Mega Projects and Human Impact
When Israel Simmons reflects on his 15-year career in construction, one theme rises above the rest: leadership is built, not appointed. From his early days as a preteen working alongside...
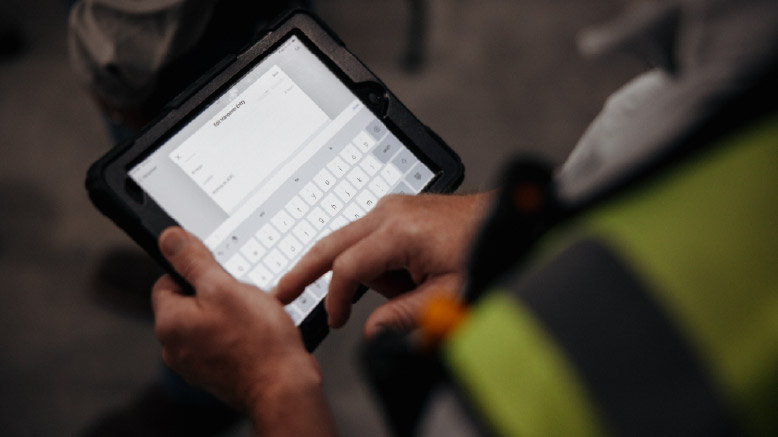
From Whiteboards to Workflows: Building a Data-Driven Project Pipeline
In civil construction, the term “pipeline” typically brings to mind physical conduits carrying water, gas or sewage, which is understandable. But in project management, a “project pipeline” is a metaphorical...

Low-voltage Systems: A New Frontier for MEP Contractors
From design through commissioning, low-voltage system designers and the MEP trades are colleagues. They work together to provide the systems that make buildings safe, comfortable, efficient and equipped for modern...

Making the Most of Construction Meetings
If there’s one thing that most construction professionals dislike more than paperwork, it’s meetings. But like paperwork, meetings are a key part of the construction process. While they can take...
Free Tools
Calculators
Use our calculators to estimate the cost of construction materials for your next project.
Templates
Find a template to help you with your construction project tasks.
Material Price Tracker
Get the latest U.S. retail prices and view historical trends for common building materials.
Glossary
Explore key terms and phrases used in the industry.