— 11 min read
Construction Inventory Management: A Guide to Mastering the Process
Last Updated Feb 13, 2025
Daren Duhon
Daren Duhon is the Warehouse Logistics Manager at RNGD, where he oversees the procurement and distribution of all jobsite materials, tools, and equipment. Previously, he spent over 30 years in the world of automotive inventory as Store Manager and District Sales Manager for NAPA Auto Parts. Daren lives in New Orleans.
Kristen Frisa
Contributing Writer
100 articles
Kristen Frisa is a contributing writer for Procore. She also contributes to a variety of industry publications as a freelance writer focused on finance and construction technology. Kristen holds a Bachelor of Arts in Philosophy and History from Western University, with a post-graduate certificate in journalism from Sheridan College. She lives in Ontario, Canada.
Last Updated Feb 13, 2025
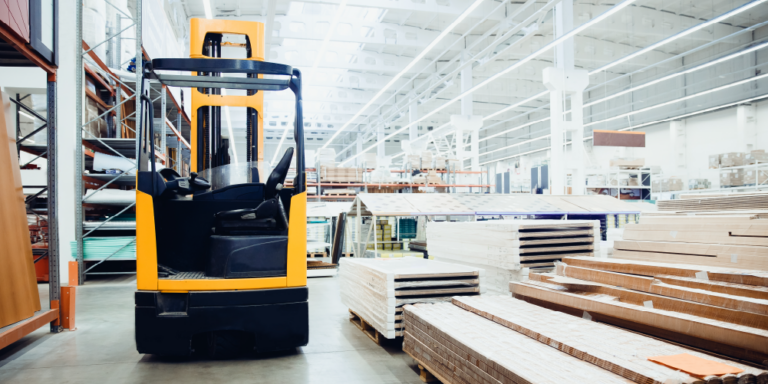
Contractors put a lot of money into the supplies, materials and equipment they need on each project jobsite. Construction inventory management – the process of ordering, storing, and distributing those products – has an enormous impact on a construction project's budget and schedule adherence.
As construction crews build out a project, their work depends on the timely availability of everything from fuel to lighting fixtures. The ultimate goal of construction inventory management is to help workers be as productive as possible by making sure they have the tools, equipment and materials they need, while controlling costs and limiting waste. For this article, we teamed up with experts at RNGD, a full-service general contractor based in New Orleans.
Table of contents
Types of inventory in construction
Broadly, there are three main categories of inventory that contractors need to manage:
- Consumables
- Building materials
- Tools and equipment
Of course, the items within each category can vary widely in cost, frequency of use, delivery time and storage space required.
Consumables
Consumables include items that are either single-use or wear out quickly and need to be replaced. Inventory managers need to identify the fastest-moving items and maintain an adequate stock to ensure rapid resupply. Water bottles are consistently one of the most popular inventory items on any project. But other items will be in higher demand depending on the work being performed.
On heavy civil projects, work gloves and safety vests are often treated like single-use items. After working underground, in mud or with hot asphalt all day, even an expensive pair of gloves often goes right into the dumpster.
On commercial or residential projects, rolls of floor protection are frequently among the heaviest-used items, especially as project closeout approaches.
Building materials
Building materials are the items actually incorporated into the finished project — these products become necessary according to project scheduling and work progress. Strategic procurement and delivery of materials involve many moving parts, including availability, price, storage and timing.
Many construction materials — particularly bulky, heavy, or custom fabricated items – are typically delivered directly to the jobsite by the supplier or distributor. A contractor may keep smaller, more frequently used items like fasteners, caulk, sealants, or hardware on hand in their inventory warehouse for on-demand delivery.
Tools & equipment
For each job, tools and equipment must be tracked, shared, and distributed between project locations.
Even within this category, inventory isn’t uniform. The difference between power tools and yellow steel is enormous. A construction company will need significantly more storage space for an excavator than a drill – and actually transporting it to the jobsite requires a heavy-duty trailer and truck.
An inventory management program for heavy equipment will also need to consider maintenance and service. These types of assets will also require regular inspections and upkeep to ensure they are operating safely and efficiently.
Each of these types of inventory requires a different approach, and every aspect demands more than just counting items on a shelf. Inventory managers need a broad understanding of all the elements at play in order to keep jobs within time and budget constraints.
Contractors need not only to manage each of these elements but also to closely coordinate between office, field, and warehouse for effective inventory management.
Stay updated on what’s happening in construction.
Subscribe to Blueprint, Procore’s free construction newsletter, to get content from industry experts delivered straight to your inbox.
Gain industry expertise, stay ahead of the curve
Explore valuable insights into the latest construction trends and project management best practices.
Subscribe to the newsletterGain industry expertise, stay ahead of the curve
Explore valuable insights into the latest construction trends and project management best practices, and learn how Procore's platform can optimize your projects.
Subscribe to the newsletterRequest a demo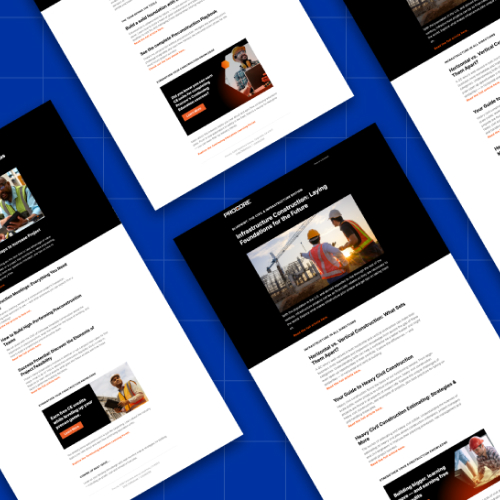
The Challenges of Managing Construction Inventory
Construction businesses face unique challenges when it comes to effectively managing inventory. More than other industries, construction firms order, track, and distribute a vast array of items for each job. And because construction work is decentralized – with crews often working simultaneously across jobsites in different locations – distribution and tracking of the inventory they need is a particular challenge for contractors.
Consider managing inventory in a retail store compared to a construction business. In a retail store, inventory is the stock or merchandise that they are selling. It is packaged uniformly to make shipment and storage easier. And it is generally kept all in one place, either on the sales floor or in storage in the back.
In construction, “inventory” means something very different. It includes all of the materials required to build the project, but it also includes the tools and equipment that the contractor owns or rents, as well as consumables like PPE or water bottles that the company provides to workers.
Construction inventory isn’t a standard size or shape, making storage and delivery more difficult. Inventory managers have to make decisions about what to store based on their storage capacity, their suppliers’ ability to fulfill orders on time, supply chains and material availability.
Accurate Tracking
A contractor’s material needs extend far beyond nuts and bolts. Not only do jobsites need wood, rebar, screws, and caulking, but also toilet paper, safety vests, printers, and coffee creamer. Thousands of items need to be purchased, cataloged, and stored for easy accessibility. The scale of this operation can be overwhelming unless contracting companies use precise organization and tracking methods.
Accountability and waste reduction
Jobsite managers need access to required materials to maintain consistent workflow on a construction project. However, contractors should hold site managers accountable for the items they use to ensure their usage is reasonable for the work at hand. Good inventory management requires a close watch on exactly how many of each item the site uses to ensure items are used responsibly to prevent overbuying and waste.
Theft
Construction jobsites are frequent targets of theft. Preventing loss – including theft by strangers and crew members alike – is an important part of managing inventory. Ideally the entire jobsite would be fenced and locked every night, but this isn’t always practical.
Contractors should ensure their employees know – and follow – the protocol for any equipment, tools, or materials kept on site, especially overnight.
Extended lead times
The construction supply chain is a complex, global system that is sensitive to a wide variety of factors. Volatile cost markets and limited availability of inputs have created long lead times for many common building materials and other inventory items.
Inventory managers need to stay informed on lead times for every item they stock, and watch for global events that could interrupt their supply chain in the near future.
Predicting needs
Optimal inventory management means having everything on hand the moment a jobsite needs it – predicting the equipment, tools, or PPE that a jobsite will require over a given period and keeping enough in stock to supply everyone.
That becomes difficult when multiple jobsites are involved and employees make last-minute requests. Hunting down items for an unexpected request can be time-consuming and throw off the normal inventory flow.
5 Keys to Good Inventory Management in Construction
Clearly, there's a lot of care and organization involved in managing all the resources on site, and every contractor will approach inventory management a little differently. However, there are some best practices that help contractors keep a firm grip on the flow of supplies and materials into and out of their businesses to ensure timely availability of critical items and less waste on their jobsites.
Recognizing the benefits of inventory management and the challenges to doing it well, what can managers do to optimize the flow of supplies into jobsites?
1. Anticipate needs — and expect the unexpected
Plan ahead to have as many items as possible on hand so workers don't have to take time and the company credit card to the hardware store. Last-minute purchases are hard to track, allow for no price control, and lack accountability. Past projects, the specs on current projects, and experience will help dictate many of the resources each jobsite will need, and how much.
RNGD Insight
You can have full control, with everything all planned in a nice system, but you will never be able to predict inventory needs every minute of the day. For example, recently one crew member called to ask for 300 1x4x16 boards by the following morning. So we had to start calling suppliers to find one that had them in stock and could deliver the next day. We got it done, but fires like that pop up all the time.
As an inventory manager, you just need to figure out the best plan to make it happen and move on. I'm here to provide accountability for the jobsites. We try to have everything our crews need in one place so we can deliver a product as quickly as possible and minimize the downtime searching for it. Every minute a superintendent, carpenter or project engineer spends searching for an item or running to the store is downtime, and downtime is expensive.
2. Keep some hands on deck
While anticipation is the gold standard of inventory management, a good backup plan is also critical. Unless a crystal ball is in play, there will be items the inventory team needs to source at the last minute. Keep enough hands on deck to service those eleventh-hour requests while maintaining the regular flow of goods.
RNGD Insight:
A lot of times at six in the morning you might get everybody calling in at one time. It's hard to keep a routine in the field to order everything in advance – I get it. So I always try to be ready for the unexpected and just learn how to adjust and move on and keep going.
3. Manage delays wisely
Good inventory management means never turning site staff away when they make a request. However, sometimes a request isn't actually urgent, and material delivery to a site can be pushed back a day without causing too much chaos at the jobsite. When things get hectic, strategize which deliveries could wait.
RNGD Insight:
Sometimes you’ve got to push somebody back a little bit. I'm a firm believer in calling them and saying, “Hey, we were on our way and something came up, I’ve got to push you back a little bit and you're okay.” And a lot of times in this business, they can wait until the next day.
4. Put technology to work
A shared inventory management solution can make it easy for jobsite staff to order what they need, see previous orders, and track the progress of ongoing orders. QR codes or RFID chips can help identify materials once they arrive at a site's laydown space, so site teams never have to hunt for what they need. GPS and geofencing can help to simplify equipment tracking and recover assets quickly in the event of theft.
Importantly, software and technology solutions enable an inventory manager to analyze past jobs to predict inventory requirements and timing on future projects.
RNGD Insight:
We operate like a hardware store and equipment rental company. The only difference is our company is our only customer. We are effectively a profit center within the bigger business.
Each crew orders items through our warehouse, and we charge them for it. We use our profit on equipment and facility maintenance, as well as monitoring and control systems. Of course, we’re all part of the same company. It all contributes to the same bottom line that every other department pays into.
5. Run inventory like a business
Every time a crew member swipes the company credit card at a hardware store or rents a piece of machinery, the company is paying someone else to manage inventory for them. Running a successful inventory management program can effectively create a profit center within the company.
Inventory items can be purchased in bulk and charged to each jobsite. Equipment rental can operate as if it were an independent company. The profit earned can be reinvested in maintenance or new inventory.
Maintaining Control & Accountability
The ultimate goal of a construction inventory manager is to improve productivity by ensuring work crews have everything they need on the jobsite. This can be assured by making sure they have the tools, equipment and materials they need.
When site employees run to the hardware store at the last minute to buy the supplies they need using the company credit card, it can cost a contractor a lot of money. The process leads to lost time, first as the employee loses productive time, and then as building progress may be delayed until the materials arrive on site.
Bulk buying power is lost on individual purchases, meaning the employee may pay more per item in-store than the contractor would spend buying many things at one time and keeping them in stock. Controlling costs on single purchases is far more difficult than with bulk purchases.
Finally, contractors lose accountability for in-the-moment employee purchases. There's no way for the contractor to confirm the need for the materials, the amount required, or where those materials wind up once they arrive on site. Thorough inventory management tracks materials usage to avoid waste and hold employees accountable for their equipment.
Was this article helpful?
Thank you for your submission.
82%
18%
You voted that this article was . Was this a mistake? If so, change your vote here.
Scroll less, learn more about construction.
Subscribe to The Blueprint, Procore’s construction newsletter, to get content from industry experts delivered straight to your inbox.
By clicking this button, you agree to our Privacy Notice and Terms of Service.
Thank you!
You’re signed up to receive The Blueprint newsletter from Procore. You can unsubscribe at any time.
Categories:
Written by
Daren Duhon
Daren Duhon is the Warehouse Logistics Manager at RNGD, where he oversees the procurement and distribution of all jobsite materials, tools, and equipment. Previously, he spent over 30 years in the world of automotive inventory as Store Manager and District Sales Manager for NAPA Auto Parts. Daren lives in New Orleans.
View profileKristen Frisa
Contributing Writer | Procore
100 articles
Kristen Frisa is a contributing writer for Procore. She also contributes to a variety of industry publications as a freelance writer focused on finance and construction technology. Kristen holds a Bachelor of Arts in Philosophy and History from Western University, with a post-graduate certificate in journalism from Sheridan College. She lives in Ontario, Canada.
View profileExplore more helpful resources
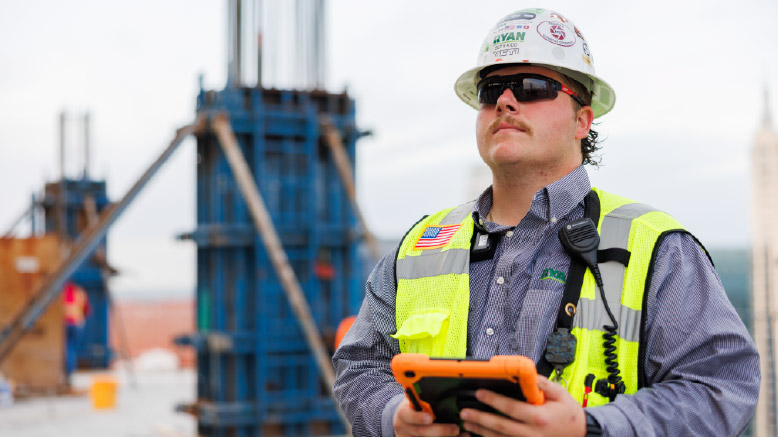
What Does a Construction Manager Do? A Guide to Roles and Responsibilities
A construction manager is central to the success of any building project. This professional oversees all on-site operations to make sure the jobsite runs safely and efficiently. Construction managers guide...
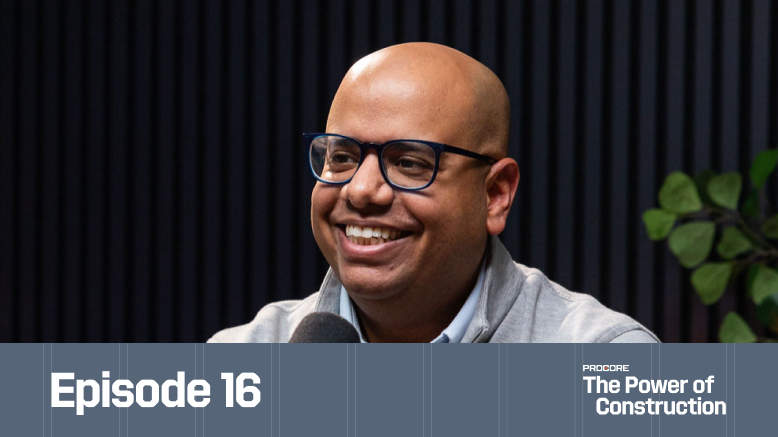
Will AI Replace ‘Paperless Builders’—or Redefine Them?
How can artificial intelligence enhance rather than replace human expertise in construction? In Episode 16, Hamzah Shanbari, Director of Innovation at Haskell and author of “The Paperless Builders,” reveals how...
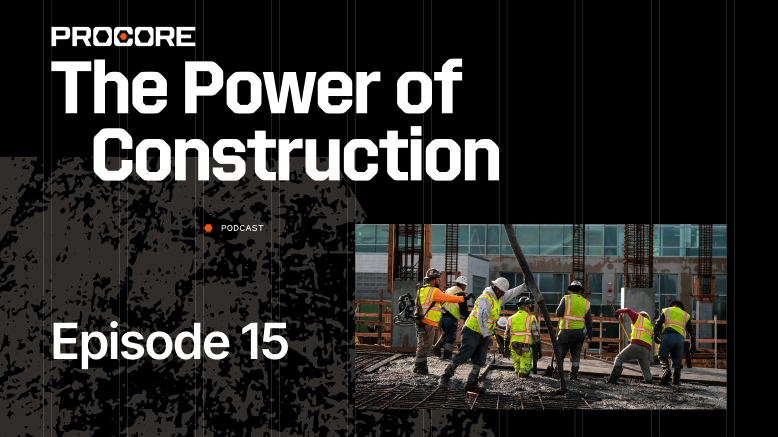
Has Construction Tech Failed its Most Important Customer?
In episode 15 of The Power of Construction, we tackle a provocative question: Has construction technology actually failed building owners? Despite billions in investment, owners report that BIM automation and...
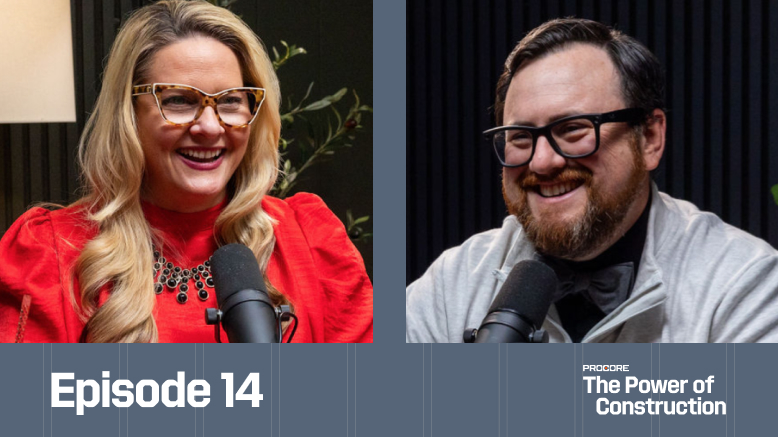
Is Construction Ready for the Future?
In episode 14 of The Power of Construction, we ask a critical question: Can an industry tasked with building our future truly meet the demand to double its growth by...
Free Tools
Calculators
Use our calculators to estimate the cost of construction materials for your next project.
Templates
Find a template to help you with your construction project tasks.
Material Price Tracker
Get the latest U.S. retail prices and view historical trends for common building materials.
Glossary
Explore key terms and phrases used in the industry.