Related Articles
— 10 min read
Construction Specifications: The Foundation for Project Clarity
Last Updated May 20, 2025
Bianca Holtier Coury
Education Audience Marketing
18 articles
Bianca Holtier Coury spent 15+ years in various roles managing construction projects, such as Preconstruction Team Lead, Purchasing Agent, and Project Manager. She has a wealth of experience in all project phases, including managing project schedules and budgets, bid management, and coordinating vendors and subcontractors. Bianca is an Associate Member of AIA and a LEED Green Associate. She currently serves as Director of Partnerships for the Construction Progress Coalition. Bianca holds a BA in Urban Design and Architecture Studies from NYU. She lives in Cleveland, OH.
Kacie Goff
Contributing Writer
78 articles
Kacie Goff is a construction writer who grew up in a construction family — her dad owned a concrete company. Over the last decade, she’s blended that experience with her writing expertise to create content for the Construction Progress Coalition, Newsweek, CNET, and others. She founded and runs her own agency, Jot Content, from her home in Ventura, California.
Last Updated May 20, 2025
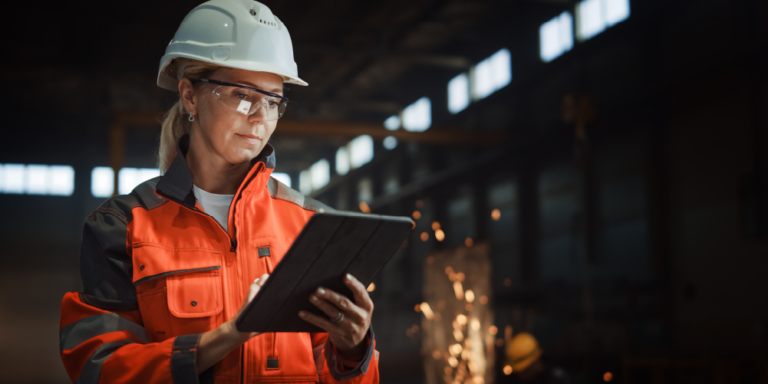
When people hear the term “construction documents,” their minds often go straight to the applicable drawings. Those visual representations of what will be built provide a huge measure of guidance — but they’re not the only source of clarity. While drawings represent things visually, projects need a way to capture and communicate guidance that can’t be represented in the drawings. For that, anyone involved in the project can turn to construction specifications.
Construction specifications — or specs, for short — add supplemental detail to guide the build. The blueprint, for example, might show where doors go and how big they should be, while the specifications say what type of material should be used for those doors and whether they need to be fire-rated.
In this article, we’ll explore construction specifications — how they’re created, the different types and best practices for getting the most out of specs.
Table of contents
The Basics of Construction Specifications
Construction specifications are a detailed set of instructions that describe the materials and methods required to construct each component of the project. The design team produces the specification document or “spec book” — usually formatted as a digital and/or hard-copy binder — that outlines a project’s requirements. The specs provide explicit instructions to guide the contractors’ work, and parameters that stakeholders can reference to check built work against during inspections.
In other words, specifications help to connect design and construction, bridging the gap between what the architects and engineers have envisioned and what gets erected and installed. Good specs build in quality for every work package on a project by including information like:
- Which materials should be used (sometimes down to the manufacturer of the material)
- Installation methods
- Timelines for project milestones
- Testing requirements
- Applicable design and safety standards
Consider the construction of a bathroom. Drawings will show where things fit, but the construction specifications communicate what the drawings can’t. The blueprint might show a tradesperson where to install a cabinet, for example, but the specs will call out what kind of cabinet it should be — detailing the product number for cabinets, hinges, paint color, etc.
Similarly, where the electrical drawing guides a subcontractor on where to place the wiring for a light fixture, the specifications detail that this fixture should be equipped with LED lighting.
Clearly, then, specifications in construction capture a wide range of information. Fortunately, organizational standards are available to ensure the appropriate stakeholders can find the details they need in a spec book that can often grow to hundreds of pages or more.
How Construction Specs Are Created & Organized
Architects and engineers are usually the ones who create construction specifications. They collaborate during the design phase to develop this guiding document. Depending on the company and the project, other parties may also contribute to the specs (if the company uses integrated project delivery, for example, field teams might weigh in).
As the specs are created, MasterFormat often serves as a guiding template to help organize the information. The spec book usually gets broken down into something akin to chapters, with each section corresponding to a MasterFormat division laid out by the Construction Specifications Institute (CSI).
The spec book may contain one section on masonry, for example, and another on finishes. Because many construction professionals are familiar with MasterFormat divisions, using this framework for specs makes it easier for them to find the information they need.
Once the construction specifications have been created and finalized, the spec book is used heavily throughout the project:
- During bidding: The spec goes out to contractors and trade partners who want to bid on the project. They might receive either the specifications in their entirety or the section applicable to the type of work they do. A plumbing subcontractor, for example, might only receive the plumbing section of the specifications.
- For scheduling: The construction specifications get handed over to the general contractor (GC) to guide their scheduling. If the specs call for an Italian marble that takes six weeks to procure, for example, the GC needs to plan the installation schedule for that marble accordingly.
- During construction: After groundbreak, construction specifications serve as a guiding document. Between the drawings and the specs, most people on the jobsite should have access to the information they need to do the work for which they were hired.
- As a hard copy: While a lot of construction professionals access the specifications digitally in 2024, many projects still keep a hard copy of the specs in the job trailer.
- As part of the as-built: The owner may get a copy of the specifications upon project completion. They can use this to crosscheck the work and answer any questions that might arise later (e.g., which types of materials were used if they need to be replaced in the future).
Build a Strong Foundation with our Preconstruction Course
With 20+ years of experience, Ben Ashburn teaches you how to streamline planning, bidding, and procurement for better outcomes.
Master preconstruction, elevate your project planning
Expand your preconstruction knowledge with our comprehensive preconstruction course.
Enroll in the courseMaster preconstruction, elevate your project planning
Expand your preconstruction knowledge with our comprehensive preconstruction course, and discover how Procore's platform can streamline and enhance your project workflows.
Enroll in the courseRequest a demo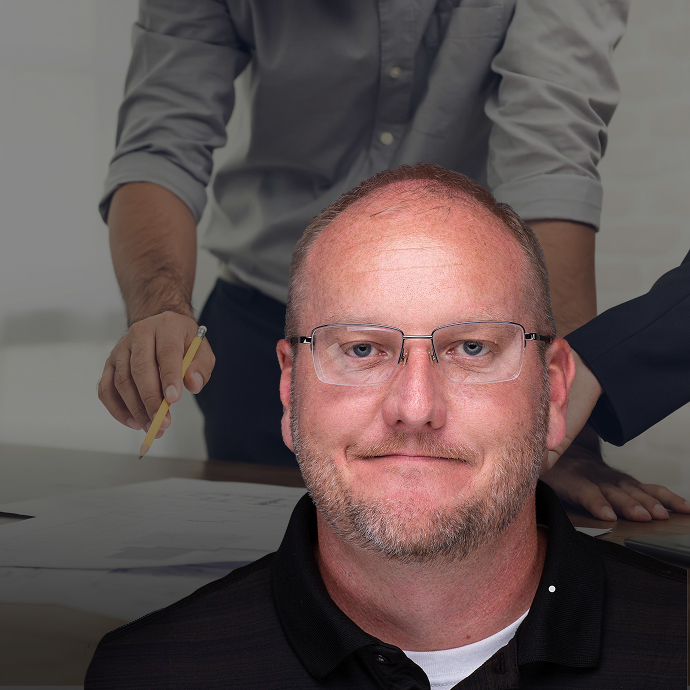
Types of Specifications in Construction
Most specs come in one of three forms: Prescriptive, Performance or Proprietary.
Prescriptive Specifications
Prescriptive specs prescribe (as the name suggests) specific materials, finishes, installation methods and more. Essentially, they tell everyone involved in a construction project what’s required to achieve the final product. Prescriptive construction specifications might call out national or international safety standards that need to be adhered to, for example.
Performance Specifications
Performance specs focus on the final outcome rather than how various teams get there. Rather than teeing up details about how to get to completion, performance specifications outline how the final product needs to perform (hence the name). They often include details about how that performance will be confirmed, like testing the building will undergo upon completion.
Proprietary Specifications
Proprietary specs provide a way to spec in specific brands, models, colors and other defined details. While they were historically less frequently used, proprietary specifications are gaining popularity as owners and other decision-makers more frequently want a way to specify granular details like light fixture models or paint colors. In fact, many manufacturers now provide a spec sheet for inclusion in the specifications book.
Construction professionals might also come across proprietary specs when making improvements to an existing building rather than erecting a new one. These provide the detail needed to ensure that new construction matches what’s already in place, like which manufacturer to source plumbing fixtures from or what type of siding to use.
Proprietary specs can drive up project costs by eliminating opportunities to shop around.
Choosing the Right Specs
The right type of spec to use for the specific project depends on the question: What are the specifications trying to communicate?
If architects and engineers want to provide detail to guide various teams, prescriptive specs give them a way to communicate that information. If they care less about how a project gets built and more about the final outcome — when they already have an established relationship with a GC they trust, for example — they might use performance specs. These provide a way to ensure quality without requiring granular details. And if the project requires matching new work to an existing building, proprietary specs become useful.
Why Construction Specifications Matter
While technology helps to make creating construction specs less onerous, developing these guiding documents is still no easy feat. Why, then, do engineers and architects go to all the trouble?
Because specs deliver a wide range of significant project benefits, including:
- Efficiencies on the job: If a subcontractor has a question, they might need to pause, contact the right person, wait for a response, and then finally resume work. But if they have access to the specs and those specs can clarify the matter, a quick check of this document keeps them on track.
- Expectation-setting: Because various parties see the specs before a project goes to bid, everyone knows what’s expected. If a subcontractor does submit a bid, for example, the construction specifications make it clear what will be required of them should they win that bid.
- Improved communication for improved relationships: Working with specifications in construction projects ensures that what’s developed during the design phase gets clearly communicated to the GC, and that the GC can pass that information neatly along to the appropriate tradespeople. This helps everyone to stay on the same page, streamlining the project and eliminating relationship challenges due to miscommunication.
- Quality assurance: Effective construction specifications provide enough detail to inform everyone about the outcome that’s required. It also clearly lays out the project's benchmarks, from international design standards to the relevant municipal safety codes. Giving everyone involved in a project this information on the front end can prevent shortcuts, oversights and other issues that could interfere with the quality of a finished build. It also provides boundaries and guidelines against which to crosscheck work as it gets completed.
- Change order minimization: Detailed specs should deliver the information required to do things correctly the first time around, minimizing change orders and keeping projects on time and on budget.
- Informed procurement and purchasing: Construction specifications give various teams the information they need to buy out the project with the right materials, finishes, etc. The specs lay out the requirements, driving a project’s schedule of values.
Best Practices and Next Steps for Specifications in Construction
At their best, specifications in construction projects connect architects, engineers, construction teams, and owners. They should provide a single source of truth that can answer a multitude of questions as the project moves forward, keeping everyone on the same page. They have the potential to eliminate rework and ensure quality.
So, how do stakeholders realize all of these benefits? The answer, to a large extent, comes down to training and education.
Teaching Teams to Access and Use Specifications
Teams in the field need to understand how specifications function, where to find them, and how to reference them. An estimator, for example, should get trained on how specs are organized so they can create the necessary bid packages. The project manager in the field needs to know how to read specs to ensure that what was bought for the project actually gets used.
At the same time, as technology drives advancements in cloud accessibility, most team members should be able to access specs with just a few clicks on their mobile device.
Pairing training with accessibility can make construction specifications a powerful tool for any construction team. Engineers and architects are already putting in the work required to gather up the details of a project and put them in one place. The more people who know how to reference and leverage those details, the better.
Up-Leveling to Read Specs More Effectively
For additional education around referencing specifications, consider CSI’s Construction Document Technologist certification. This gives construction professionals the opportunity to dive into MasterFormat, familiarizing themselves with the outline template most frequently used to organize specs.
Don’t stop with that certification, though. Specs are evolving, and people who want to stay on the leading edge need to keep up.
As technology advances, creating and accessing construction specifications will likely get easier. AI tools might integrate specs with drawings so stakeholders can access everything with just a few clicks on their tablet. While it’s important to feel comfortable with specifications in construction in their current form, the future of specs — similar to just about every other aspect of construction — will adapt and change alongside technological advances.
Was this article helpful?
Thank you for your submission.
96%
4%
You voted that this article was . Was this a mistake? If so, change your vote here.
Scroll less, learn more about construction.
Subscribe to The Blueprint, Procore’s construction newsletter, to get content from industry experts delivered straight to your inbox.
By clicking this button, you agree to our Privacy Notice and Terms of Service.
Thank you!
You’re signed up to receive The Blueprint newsletter from Procore. You can unsubscribe at any time.
Categories:
Tags:
Written by
Bianca Holtier Coury
Education Audience Marketing | Autodesk
18 articles
Bianca Holtier Coury spent 15+ years in various roles managing construction projects, such as Preconstruction Team Lead, Purchasing Agent, and Project Manager. She has a wealth of experience in all project phases, including managing project schedules and budgets, bid management, and coordinating vendors and subcontractors. Bianca is an Associate Member of AIA and a LEED Green Associate. She currently serves as Director of Partnerships for the Construction Progress Coalition. Bianca holds a BA in Urban Design and Architecture Studies from NYU. She lives in Cleveland, OH.
View profileKacie Goff
Contributing Writer
78 articles
Kacie Goff is a construction writer who grew up in a construction family — her dad owned a concrete company. Over the last decade, she’s blended that experience with her writing expertise to create content for the Construction Progress Coalition, Newsweek, CNET, and others. She founded and runs her own agency, Jot Content, from her home in Ventura, California.
View profileExplore more helpful resources

Project Visibility with Real-Time Dashboards: How Construction Teams Stay on Track
Productivity in construction depends on more than just hitting daily targets in the field. It also requires quick decision-making and alignment between the office and the jobsite. Real-time dashboards centralize...
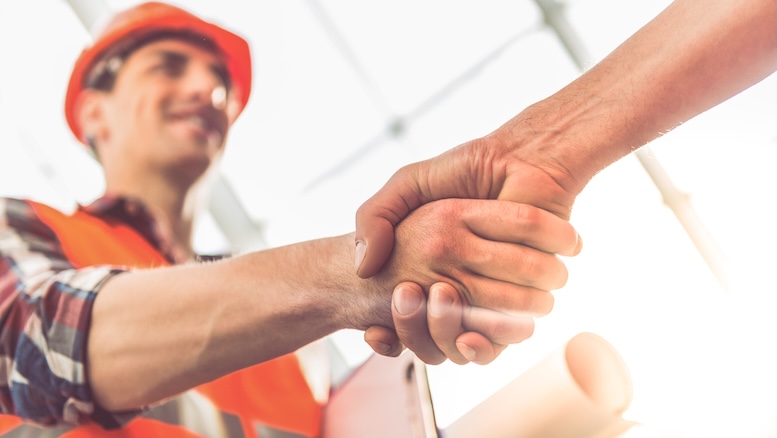
Using Standard Operating Procedures for Better Contract Management
Every construction project is different, meaning that GCs have to be continually agile and strategic about applying their experience. Major categories change from project to project, from the owner to...
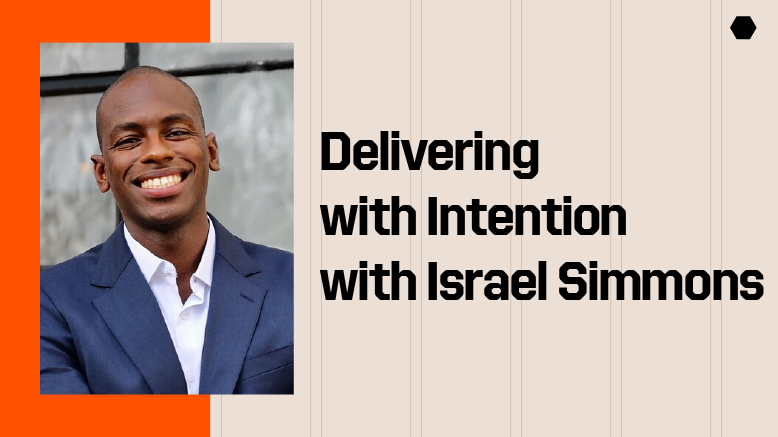
Delivering with Intention: Leadership Lessons from Israel Simmons on Mega Projects and Human Impact
When Israel Simmons reflects on his 15-year career in construction, one theme rises above the rest: leadership is built, not appointed. From his early days as a preteen working alongside...
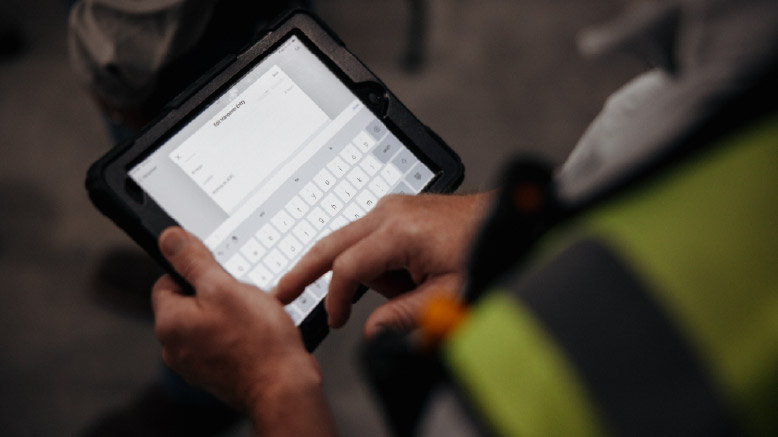
From Whiteboards to Workflows: Building a Data-Driven Project Pipeline
In civil construction, the term “pipeline” typically brings to mind physical conduits carrying water, gas or sewage, which is understandable. But in project management, a “project pipeline” is a metaphorical...
Free Tools
Calculators
Use our calculators to estimate the cost of construction materials for your next project.
Templates
Find a template to help you with your construction project tasks.
Material Price Tracker
Get the latest U.S. retail prices and view historical trends for common building materials.
Glossary
Explore key terms and phrases used in the industry.