— 5 min read
Construction Punch Lists Explained
Last Updated Jul 31, 2025
Alex Benarroche
Associate Counsel
26 articles
Alex Benarroche serves as Associate Counsel for Procore. His legal expertise includes construction, contracts, business, and intellectual property. Alex is bilingual in English and Spanish. He earned a J.D. from Loyola University College of Law and an M.S. in Intellectual Property and Internet Law from the University of Alicante in Spain. Originally from South Florida, Alex has called New Orleans home since 2003.
Kristen Frisa
Contributing Writer
100 articles
Kristen Frisa is a contributing writer for Procore. She also contributes to a variety of industry publications as a freelance writer focused on finance and construction technology. Kristen holds a Bachelor of Arts in Philosophy and History from Western University, with a post-graduate certificate in journalism from Sheridan College. She lives in Ontario, Canada.
Last Updated Jul 31, 2025
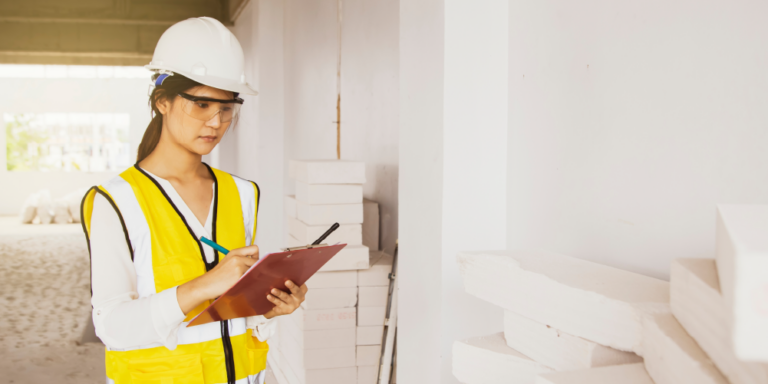
In the final stages of a construction project, contractors are often left with a handful of mostly finished tasks that still require attention. GCs and subs use punch lists to document and keep track of these items that still need finishing before they can hand off the project to the owner.
Understanding punch lists is important for making work is completed to specification — as well as getting paid for that work. Keep reading to learn what punch lists are used for and what to include in one.
Table of contents
What is a punch list in construction?
A punch list is a document that lists the final work items remaining before a construction project is considered complete. Contractors add all work that does not conform to the specifications in the construction contract to the punch list. Items on a punch list typically include minor corrections, alterations, or repairs that are required before the release of final payment.
How Punch Lists Are Used
The punch list is typically the last step in the project in order to double-check that everything has been completed according to the owner’s specifications. It’s called a “punch list” because historically contractors would manually punch out holes next to each item on a paper list to show that a task was complete.
A well-formulated punch list outlines all the tasks that need to be addressed before the structure is ready for occupancy. Punch work items are usually minor fixes, which can include any incomplete or incorrect installations, as well as incidental damage on existing finishes or structures.
Examples of Punch List Items
A punch list will typically include a variety of items to test, add, fix, or remove – the items on the list are called “punch work” or “punch out work.” Punch list items will vary widely depending on the type of project. Punch work on an industrial or infrastructure project will look very different from that of a residential or retail project.
Items to Test
Testing is done to verify that all installed work, materials, and equipment function as expected. Punch work often includes testing of:
- Appliances
- Equipment
- Doors & windows
- Plumbing fixtures
- Mechanical elements
- Communication systems
- HVAC systems
- Etc.
Items to Add
Punch work frequently includes items that were left off, whether intentionally or not. This includes items like:
- Light covers
- Hardware
- Paint touch-ups
- Coating/sealant
- Etc.
Items to Fix
While contractors and equipment remain on the jobsite, there is always the risk of damage to materials, equipment, or systems that needs to be corrected. Punch work can include fixing:
- Leaks
- Damaged materials
- Improper installation
- Cracks
- Defective equipment
- Etc.
Items to Remove
Any items, equipment, or materials not included in the project delivery need to be removed before handover. A punch list often includes the removal of items such as:
- Trash
- Equipment
- Extra materials
- Tools
- Protective covers
- Etc.
Using a Punch List Template
Contractors can use a template for their punch lists to maintain a consistent look and completion process. The template can include numbered rows, as well as columns for the location, description, person responsible, status and date completed for each of the tasks.
Free Download
Construction Punch List Template
Download a free fully customizable punch list template to stay organized and track responsibilities of punch work during closeout.
- Free customizable template
- Ready-to-use
- Designed specifically for construction
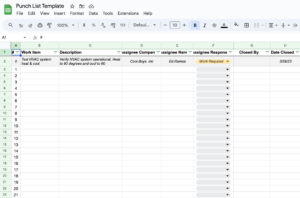
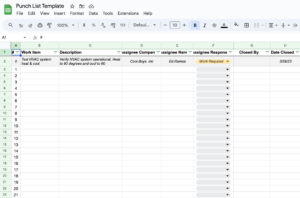
Responsibility for Punch List Items
Everyone on a construction project has a role to play in the execution of a punch list, including the general contractor, and subcontractors on the project, the owner, and the architect.
Typically, it’s the responsibility of the general contractor to make sure all these line items are taken care of before a final completion certificate can be issued on the project. The GC may assign punch work to the subcontractors responsible for particular areas of work.
Generally, the GC will do a walkthrough with the owner to identify any incomplete or non-conforming work and create the initial punch list. Depending on what issues remain, certain subcontractors may be called back to the project to correct outstanding issues. For many projects, that’s as far as the punch list goes.
If the project has one, the architect also plays an important role in reviewing the punch list to approve final payments. The GC will send their punch list to the architect, who will then conduct their own walkthrough to determine what has been completed to their design specifications and what hasn’t.
The architect will then update the punch list and send it back down to the owner and GC. The GC is then in charge of sending out the punch list to the subcontractors and making sure they complete all the work.
Subcontractors have a lot of work during the punch list process: They are the ones who are performing much of the punch work and gathering all the necessary change orders and documentation that the GC must pass on to the owner. The best practice here is to start organizing these documents as soon as possible rather than waiting until the end of the project.
Stay updated on what’s happening in construction.
Subscribe to Blueprint, Procore’s free construction newsletter, to get content from industry experts delivered straight to your inbox.
Gain industry expertise, stay ahead of the curve
Explore valuable insights into the latest construction trends and project management best practices.
Subscribe to the newsletterGain industry expertise, stay ahead of the curve
Explore valuable insights into the latest construction trends and project management best practices, and learn how Procore's platform can optimize your projects.
Subscribe to the newsletterRequest a demo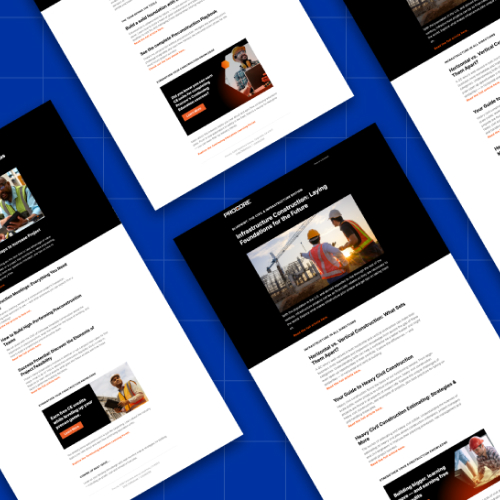
Completing the Punch List
Everyone on a project should focus on the punch list because it makes sure the building is ready for occupancy, but also because it’s a key step before final payment. An owner will typically be holding onto retainage payments until the punch list items are completed.
When the contractor believes that they have reached substantial completion, they can request a “pre-final” inspection of the project. Hopefully, the punch work needed will be a light lift, and the final completion and payment will not be far away.
In most construction contracts, the final payment is released when the punch list items have been completed to meet the contract specifications. Once “punched,” the list is then typically attached to the Certificate of Substantial Completion.
Each project faces its own unique challenges, but preparing a complete and accurate punch list will give everyone on the project a clear understanding of what needs to be done in order to finish the project.
Was this article helpful?
Thank you for your submission.
94%
6%
You voted that this article was . Was this a mistake? If so, change your vote here.
Scroll less, learn more about construction.
Subscribe to The Blueprint, Procore’s construction newsletter, to get content from industry experts delivered straight to your inbox.
By clicking this button, you agree to our Privacy Notice and Terms of Service.
Thank you!
You’re signed up to receive The Blueprint newsletter from Procore. You can unsubscribe at any time.
Categories:
Tags:
Written by
Alex Benarroche
Associate Counsel | Procore
26 articles
Alex Benarroche serves as Associate Counsel for Procore. His legal expertise includes construction, contracts, business, and intellectual property. Alex is bilingual in English and Spanish. He earned a J.D. from Loyola University College of Law and an M.S. in Intellectual Property and Internet Law from the University of Alicante in Spain. Originally from South Florida, Alex has called New Orleans home since 2003.
View profileKristen Frisa
Contributing Writer | Procore
100 articles
Kristen Frisa is a contributing writer for Procore. She also contributes to a variety of industry publications as a freelance writer focused on finance and construction technology. Kristen holds a Bachelor of Arts in Philosophy and History from Western University, with a post-graduate certificate in journalism from Sheridan College. She lives in Ontario, Canada.
View profileExplore more helpful resources
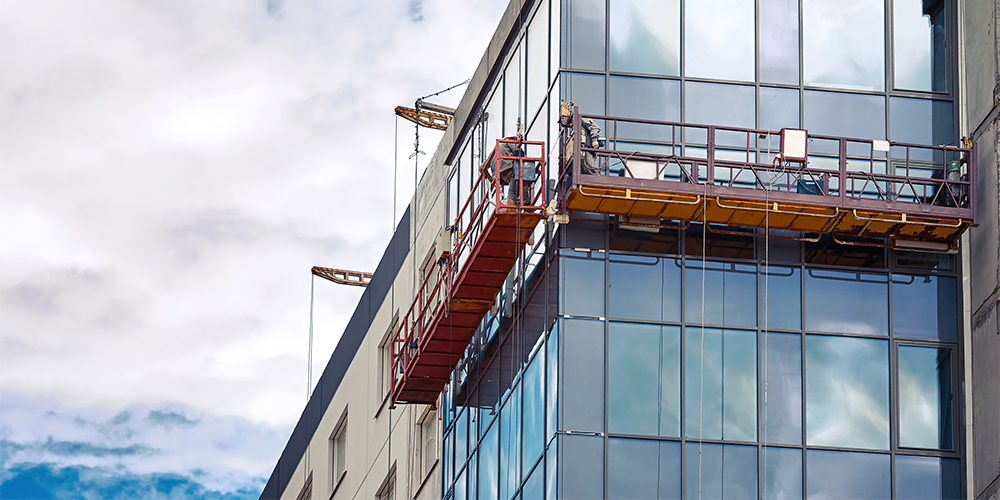
Preparing for Post-Construction: A Guide to the Final Phase of a Project
Large construction projects often take years to plan, more years to design, and even more years to build. From the groundbreak point of view, it’s often difficult to see the...

A Guide to Construction Commissioning
During project closeout, an owner wants to receive any documents, training and warranties needed to take over the management and maintenance of their building. But they also want assurance that...
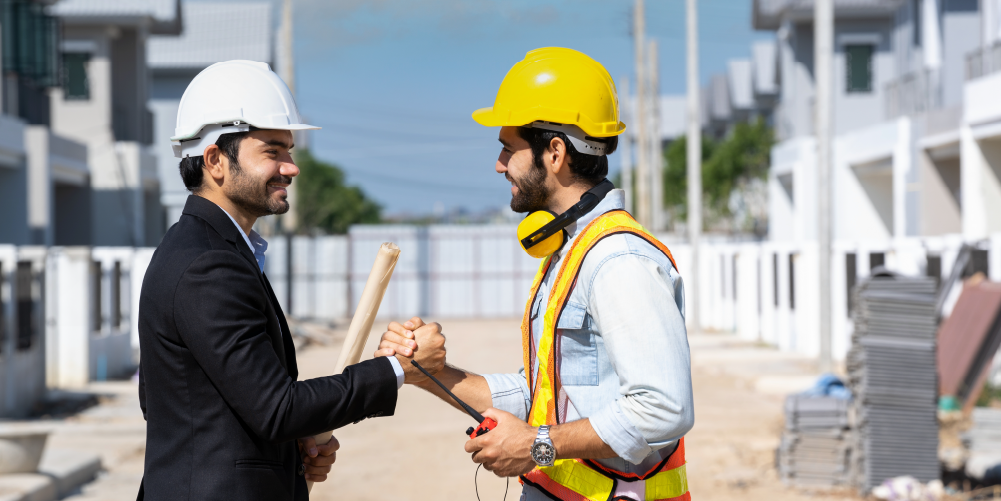
Construction Handover: Keys to an Efficient Process
After the months or years it takes to complete a construction project, the handover process begins. Project handover is the final part of the construction process, where a project, along...

Construction Closeout Documents: What’s Included & Why
Few parts of the building process can feel as stressful and as complicated as closeout: the multi-step, final phase of construction in which a project is prepared to be handed...
Free Tools
Calculators
Use our calculators to estimate the cost of construction materials for your next project.
Templates
Find a template to help you with your construction project tasks.
Material Price Tracker
Get the latest U.S. retail prices and view historical trends for common building materials.
Glossary
Explore key terms and phrases used in the industry.