— 8 min read
Protecting MEP Systems Against the Effects of Climate Change
Last Updated Jun 6, 2025
Michael Spano
Solutions Engineer, Public Sector
Michael Spano is a Procore Solutions Engineer who partners with Public Sector agencies to deliver tailored technical solutions for their project management and construction processes. Michael brings a strong background in the construction and engineering industries, having spent time focusing on HVAC, plumbing design and managing a wide range of construction projects.
Diane McCormick
Writer
26 articles
Diane McCormick is a freelance journalist covering construction, packaging, manufacturing, natural gas distribution, and waste oil recycling. A proud resident of Harrisburg, PA, Diane is well-versed in several types of digital and print media. Recognized as one of the premier voices in her region, she was recognized as the Keystone Media Freelance Journalist of the Year in 2022 and again in 2023.
Last Updated Jun 6, 2025
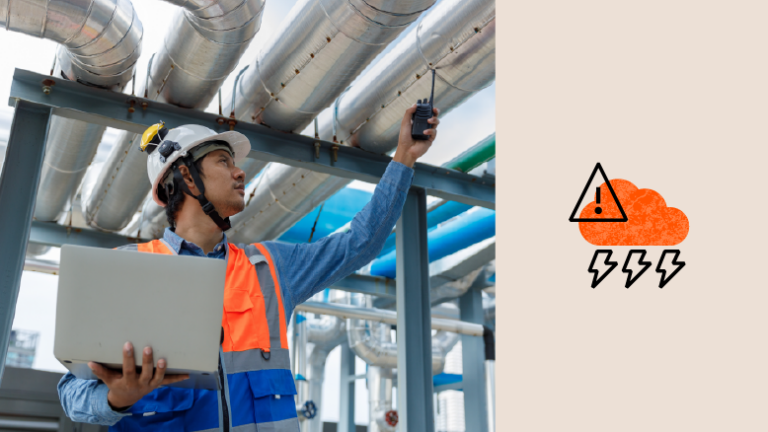
In the race to harden structures against extreme weather, mechanical, electrical and plumbing (MEP) systems play an important role. Contractors who anticipate the impact of climate change and offer adaptations protect the investments of project owners while mitigating their own risk and driving efficiencies.
In this article, we'll explore the ways strategic use of technology, data and standards facilitates scalable solutions that elevate MEP systems to new heights in performance, sustainability and cost-effectiveness and protect structures against environmental challenges.
Table of contents
Building for Extreme Weather Resilience
Balancing safety, efficiency, cost and environmental impact continues to be a key challenge for MEP design and construction. For centuries, builders have done their best to equip their projects to withstand the earthquakes, hurricanes, monsoons, tsunamis, floods and tornadoes endemic to their regions.
Climate change adds a new layer of complexity, introducing natural and manmade events that strike with ferocity, and often in unexpected places. Today’s built environment demands the durability to survive superstorms, uncontrollable wildfires, raging floods, prolonged droughts and temperature extremes.
To mitigate the risks, governments are intensifying their building codes, and project owners are adopting net-zero goals that optimize building efficiency and advance sustainability. Builders are playing their part by employing greener processes, operational efficiencies and materials and practices that stand up to extremes.
The Effects of Climate Change on MEP
Extreme events related to climate change can take a direct hit on MEP systems. While builders perfect their techniques to address the risks, manufacturers are developing innovative materials that balance safety, environmental impact and cost-effectiveness.
Mechanical
Challenges: Rising temperatures and humidity put a strain on mechanical systems, causing higher energy consumption, higher operational costs and shortened lifespans. While the COVID-19 pandemic accelerated advancements in commercial air filtration systems, infiltration of wildfire smoke and pollutants remains a persistent threat to occupant comfort and health.
Solutions: Available adaptations to minimize heat gain and optimize energy and operational efficiency include passive cooling, advanced insulation, high-performance heat pumps and geothermal installations that leverage the earth’s stable temperatures to sustain heating and cooling capabilities. Advanced air filtration systems that guard against the consequences of wildfires, humidity and air-quality alert days can remove particulate matter, control moisture and prevent mold growth and adjust ventilation rates according to occupancy and air-quality sensor readings.
Electrical
Challenges: When disaster strikes, power outages follow. As a result, building occupants can be endangered, systems fail and downtime accrues. Power failures to the mission-critical projects that dominate today’s construction landscape can jeopardize the health and safety of countless people who rely on data centers, hospitals, banking and communications networks to survive and recover from disasters.
Solutions: Redundancy and resilience add protective layers that keep the lights on and essential systems operating. Microgrids, backup generators and battery storage — a necessity for energy generated by local renewable sources — can power a site independently when the centralized grid fails.
Plumbing
Challenges: Floodwater can overwhelm plumbing as well as compromise electrical and mechanical systems. Building design is changing to accommodate stress on water management systems.
Solutions: Protections against water damage and backflow can include flood-resistant building materials, elevating MEP equipment above extreme flood levels, and creating redundant backup systems in case of failure. Stormwater management can incorporate natural assets, such as rain gardens, that control and absorb excess water. Graywater recycling systems can lessen reliance on municipal water systems and provide independent water supplies during drought.
The Role of MEP Contractors
Protecting against the effects of climate change begins with the power to peer into the future. Good relationships with design teams can arm contractors with timely information on innovations under development that can then be incorporated into future projects.
The earlier that MEP contractors are involved, especially through design-assist and design-build projects, the more power they have to futureproof a project. At the early stages, the climate considerations impacting MEP systems can get a full review, generating strategic, scalable and cost-effective approaches that anticipate all eventualities and avert the small missteps that snowball into big miscalculations.
When extreme events occur, the most severely impacted buildings and infrastructures are the outdated ones, built to older codes and never updated. When called upon, the construction industry can retrofit current infrastructure with durable, modern materials known to hold out against extremes.
Every contractor should keep in mind that codes and standards are there for a reason. Many exist to protect lives. When it comes to sustainability and environmental regulations, it’s important to see these as part of a bigger picture to create a safe and sustainable future, rather than simply fulfilling the minimum requirements.
Michael Spano
Solutions Engineer, Public Sector
Procore Technologies
The inadequacy of yesterday’s built environment explains why today’s stricter codes, standards and net-zero goals are imperative. For builders, they are not just compliance checklists. They also serve as evolving guides for cogent, timely conversations and action plans on building climate-resilient projects — efficiently and cost-effectively.
However, it’s important to keep in mind that code development can precede construction by several years. By the time ground is broken on a project, codes could lag behind the realities of actual climate-change impact.
Leaders in construction and design can pursue two objectives that help close the gap:
- Engage with policymakers and industry organizations on standards development. Input from the ground level, where the effects of climate change-related events are immediate and no longer theoretical, can carry industry standards and governmental codes closer to real-world effectiveness and relevance, for fewer check-the-box tasks.
- Overshoot the target. Select practices and equipment that exceed current standards and can withstand ever-harsher conditions. Find the probabilities in data from the National Oceanic and Atmospheric Administration’s Climate Explorer, which predicts long-term ranges of temperatures, precipitation and heating and cooling use by locality throughout the U.S.
Educating workers on the “why” behind strict codes and standards, for tradespeople who understand the lifesaving and environmentally sustainable purposes behind exacting specifications. Their knowledge-based adherence can increase compliance and prevent costly do-overs.
Courses about construction.
For construction.
Unlock your career potential with our free educational courses on Health & Safety, Data in Construction, and more.
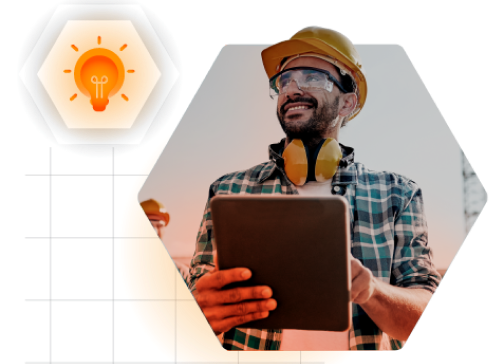
Harnessing Technology and Efficiency
The advent of building information modeling (BIM), project management software and other transformative practices increases the efficiency of builds and enhances climate-change resiliency and sustainability on several fronts.
Streamlining Construction
Streamlining construction advances internal sustainability and operational-efficiency goals. Better collection and dissemination of information reduces the need to over-order materials, for less waste and fewer resources needed to power jobsites and transport supplies.
Harnessing AI
AI integrated into project management tools draws logical conclusions from reams of data and generates insights that support perceptive decisions.
Building with BIM
Advanced BIM modeling — including "6D" BIM that incorporates sustainability into builds — simulates climate change-related extremes and creates opportunities to uncover and correct performance vulnerabilities.
Using Prefabricated Elements
Modular construction and prefabrication can increase efficiency, accelerate timelines and reduce onsite waste.
Balancing the Costs of Sustainability
As always, project owners, designers and contractors finalizing their decisions on equipment and practices must strike a balance, weighing a range of factors that can be in harmony or in conflict.
In the climate change equation, highly efficient systems can be costly, and resilience demands redundancy that adds to the budget. An advanced refrigerant might reduce ozone depletion but could lower energy efficiency. Any HVAC system, no matter how highly rated, will consume a large percentage of a structure’s energy.
Weighing short-term factors such as price tags against long-term benefits, including operational savings from energy efficiency, can demystify the equation by calculating ROI according to dollars saved on operations and the consequent payback periods.
Green building certifications such as LEED also offer guidance for assessing competing factors. LEED certification has helped standardize sustainable construction, creating industry yardsticks for measuring project decisions against good, better and best practices.
Taking Proactive Steps for MEP Construction
The tools and practices designed to blunt the impact of climate change are continuously evolving – and so is climate change. In this shifting atmosphere, strategies for keeping pace while continuing to drive efficiencies and mitigate risk include:
Stay informed.
Staying informed on and continuously applying climate-related MEP codes and standards. Use available project management information systems (PMIS) software to connect quality control to field operations, providing on-the-spot access to codes and standards for seamless application on jobsites.
Collaborate as often as possible.
Collaborate early and often with designers and owners. Bring climate change into the dialogue, and apply it to every aspect of MEP design, installation and operations.
Adopt technology.
Exploring and adopting new technologies and equipment that enhance MEP system efficiency and climate resilience. Read industry newsletters and blogs, talk with peers and ask service reps for data on climate change resilience and redundancy.
Train early.
Starting early to train and educate the workforce on the value of climate considerations in MEP trades.
Go above and beyond.
Aim above contractually obligated green-certification levels. If achieving a higher level is feasible, go for it.
The sooner design teams, builders, owners and agencies begin communicating, the more effective and productive they’ll be at combating climate change. Early collaboration allows for open, constructive dialogue in a cooperative environment. Waiting until later stages — especially during construction — makes it significantly more difficult to implement changes.
Michael Spano
Solutions Engineer, Public Sector
Procore Technologies
While images of destruction dominate the news after a disaster, contractors don’t have to step up only for rebuilds. The rise of extreme weather events offers opportunities for the construction industry to plan ahead with adaptations that keep newbuild and retrofitted structures on their feet, ready to serve people and help communities survive and recover.
Was this article helpful?
Thank you for your submission.
100%
0%
You voted that this article was . Was this a mistake? If so, change your vote here.
Scroll less, learn more about construction.
Subscribe to The Blueprint, Procore’s construction newsletter, to get content from industry experts delivered straight to your inbox.
By clicking this button, you agree to our Privacy Notice and Terms of Service.
Thank you!
You’re signed up to receive The Blueprint newsletter from Procore. You can unsubscribe at any time.
Categories:
Tags:
Written by
Michael Spano
Solutions Engineer, Public Sector | Procore Technologies
Michael Spano is a Procore Solutions Engineer who partners with Public Sector agencies to deliver tailored technical solutions for their project management and construction processes. Michael brings a strong background in the construction and engineering industries, having spent time focusing on HVAC, plumbing design and managing a wide range of construction projects.
View profileDiane McCormick
Writer | Procore Technologies
26 articles
Diane McCormick is a freelance journalist covering construction, packaging, manufacturing, natural gas distribution, and waste oil recycling. A proud resident of Harrisburg, PA, Diane is well-versed in several types of digital and print media. Recognized as one of the premier voices in her region, she was recognized as the Keystone Media Freelance Journalist of the Year in 2022 and again in 2023.
View profileExplore more helpful resources

Low-voltage Systems: A New Frontier for MEP Contractors
From design through commissioning, low-voltage system designers and the MEP trades are colleagues. They work together to provide the systems that make buildings safe, comfortable, efficient and equipped for modern...
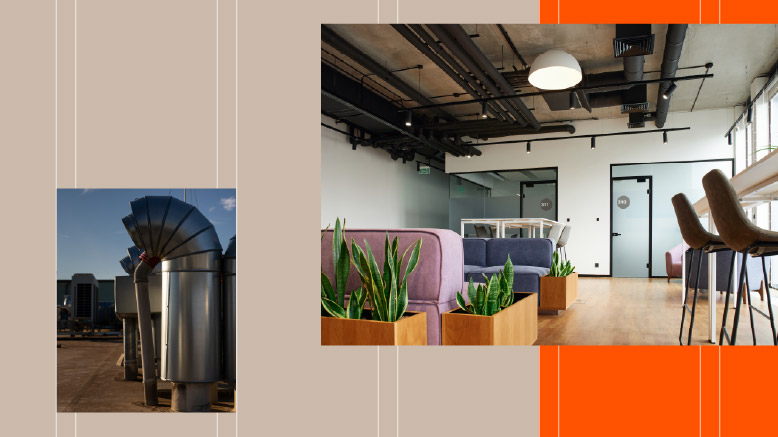
Comfort Mood: Making MEP Central to Occupant Comfort
In many post-COVID-19 projects, occupant comfort has transitioned from a “nice to have” to a “must have.” It’s infused into collaborations from the earliest phases of design and preconstruction. That...
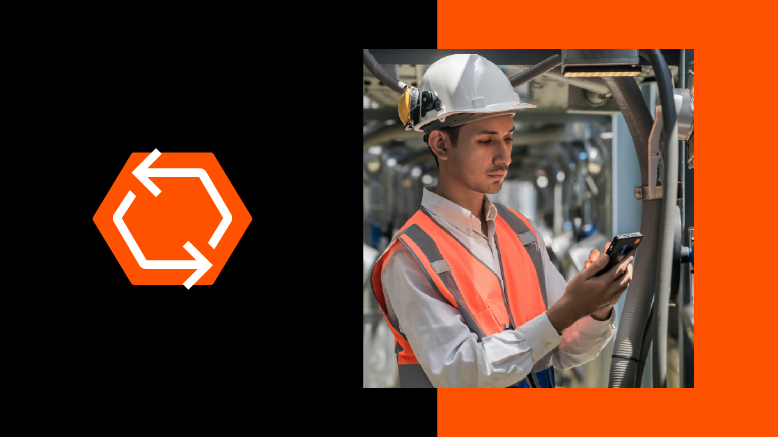
The MEP Lifecycle: How Contractors Can Benefit from Thinking Ahead
From the beginning of a project, MEP contractors should be thinking about the lifecycle of their systems. Prioritizing the lifecycle early in the process helps MEP trades influence design, select...
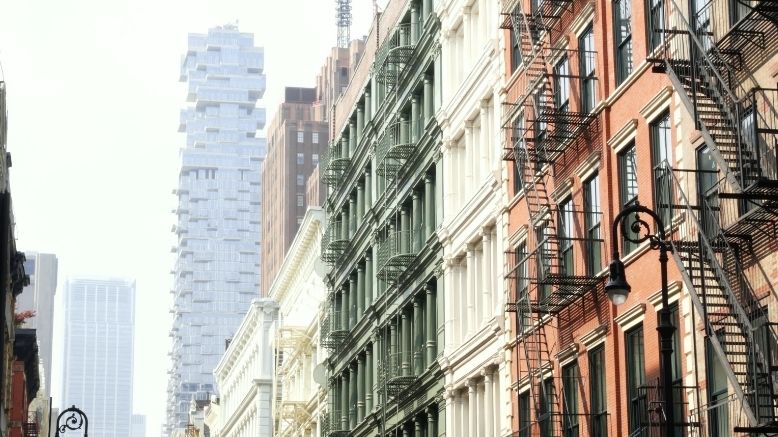
Retrofitting Aging Infrastructure: 5 Essentials for Managing MEP Risk
MEP contractors help preserve aging infrastructure by bringing systems to contemporary standards in sustainability, comfort and accessibility. Although the opportunities are unique, retrofits of existing buildings present known obstacles and...
Free Tools
Calculators
Use our calculators to estimate the cost of construction materials for your next project.
Templates
Find a template to help you with your construction project tasks.
Material Price Tracker
Get the latest U.S. retail prices and view historical trends for common building materials.
Glossary
Explore key terms and phrases used in the industry.