— 7 min read
Building a Data-Development Culture for Precision and Progress in MEP
Last Updated Jun 10, 2025
Anthony Verdiglione
Senior Strategic Product Consultant
Anthony Verdiglione is a seasoned construction professional and accomplished project manager with more than two decades of solid experience. Well-versed in nearly every construction discipline, Anthony adds immediate value to any transaction, leveraging his vast base of knowledge to drive projects, profits, and the industry. A true champion of construction, he works tirelessly to stay abreast of the latest trends while passing that value on to the customers he dutifully services.
Diane McCormick
Writer
26 articles
Diane McCormick is a freelance journalist covering construction, packaging, manufacturing, natural gas distribution, and waste oil recycling. A proud resident of Harrisburg, PA, Diane is well-versed in several types of digital and print media. Recognized as one of the premier voices in her region, she was recognized as the Keystone Media Freelance Journalist of the Year in 2022 and again in 2023.
Last Updated Jun 10, 2025
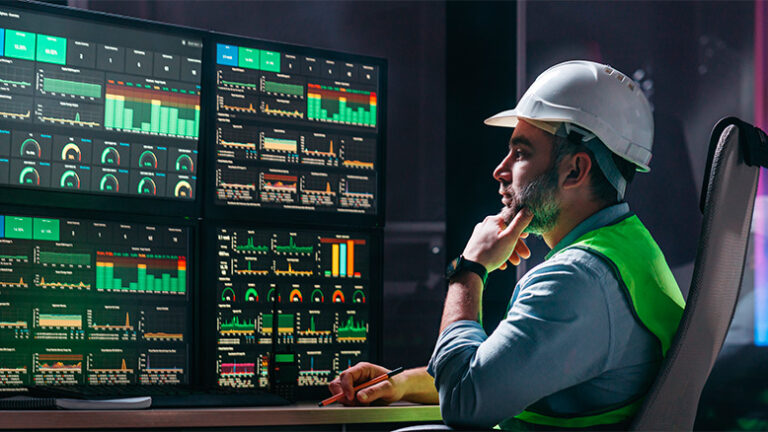
Every time a project manager or executive misses a warning sign of a jobsite slowdown or clash, that’s money left on the table. When key indicators of lagging productivity or imbalanced earned value are overlooked, they will balloon into costly problems.
Methodical development and analysis of data keeps the obstacles in view, for actionable insights. Data uncovers progress, challenges and the risks that sap money, time and resources. For MEP coordination, leveraging data can guide corrective steps in project management, risk mitigation and operational efficiencies.
Table of contents
Focusing on Quality First
Good data identifies trends in safety, quality and productivity. With a fact-based perspective, construction leaders can take the proactive measures that fix jobsite malfunctions and keep performance improving in a continuous loop.
Project management software that’s “platform-integrated” — linking the disparate data sets loaded into the PMS — draws the complete picture needed for effective project tracking and data-driven decision making. By revealing relationships and cascading impacts, platform integration equips project leaders to follow the thread of a challenge in one area to its root cause in another.
These platform-integrated tools put redlining in digital form. They feed information to field operations to prevent clashes, while giving senior supervisors the power to visualize an evolving project and make real-time adjustments.
Data Collection Fundamentals
Construction companies beginning the data-development journey don’t have to dive into the deep end of the pool. Developing data into manageable packages takes intention and direction.
Precise information collection fuels better decisions, so it’s best to start small, with a foundation of clean, quality data. A few basic steps build capabilities and confidence.
Make tracking a daily process.
Weekly lookbacks are only guesstimates. Daily time entries, while memories are fresh, get closer to actual time counts and cost codes, for more accurate productivity tracking. Encourage subcontractors to collaborate in daily data entry. Hold them accountable for data quality and timely input. Top-down leadership shows the way. When team members see the decision makers holding themselves accountable, they will follow suit.
The main thing is, just enter it. Enter it right. Enter it each day. That way we get a better cost accounting of what happened. In no contract are you ever out there to do penny for penny. If you're going to give some, you're going to get some. Knowing where to give, though, you've got to know where the cost is.
Anthony Verdiglione
Senior Strategic Product Consultant
Procore Technologies
Track submittals properly.
Remind subcontractors that marking rejected submittals as “open” inadvertently conceals the data explaining the rejections. By preserving those rejections, project executives and PMs can evaluate misalignments with contract documents, saving the time and money they would otherwise spend later correcting recurring mistakes.
In this mindset, submittal tracking becomes a technique for assessing subcontractor performance and PM time allocation. Here is data for managing not just the project but also the process of extracting vital information and using it to optimize efficiencies, reduce costs and minimize risk.
Take advantage of PMS capabilities.
Generate production rates by using the PMS to tie cost codes to production quantities. Monitoring production rates against budgeted hours helps identify potential issues early. If a time lag starts to surface, look for the cause, such as a shortage of manpower or equipment onsite. This is where earned value – the metric intertwining cost, schedule and scope – reveals whether the value of work completed so far is aligned with planned costs.
Use platform integration to mark requests for information (RFIs) for cost or schedule impact, even if that impact is none or to-be-determined. From there, running a report can reveal the RFIs that harbor potential cost or savings impacts and, at a more granular level, the number of RFIs linked to change events. Subtracting the change-event RFIs from the cost-impact RFIs shows how many RFIs are waiting for resolution and, by their indeterminate nature, costing money.
Utilize PMS’ quick-capture tools for efficient field observations and issue tracking. Even busy supervisors can be trained to enter a simple voice memo or to tap a tablet when they witness the jobsite minutiae that, collated for analysis by a PM or PX, reveal trends in safety and operational risks ripe for correction.
Using Data to Drive Project Management
Applying data-based practices to daily routines creates insights for targeted decisions on the everyday calls that keep a project in scope and on budget.
Run regular reports on open and closed RFIs and submittals, and link them to drawings for field operations to view. Review the results with specialty contractors, including response time, tags, cost or schedule impact and people involved in change events.
Out of each job, there are always lessons you're going to learn. If I’ve worked with an architect on three jobs, I can now go back and pull data from those jobs and say, ‘Where did I have the problem? Where were my RFIs from?’ Now I'm ahead of the game. I know where I can ask those questions in the bid.
Anthony Verdiglione
Senior Strategic Product Consultant
Procore Technologies
Optimize workforce allocation by scrutinizing labor classifications and ratios. Make sure that the balance of journeymen to apprentices aligns with contract documents. Weigh each task for whether too many apprentices signal trouble ahead or too many journeymen are draining the budget.
Take a big-picture look at specialty contractors bidding for jobs. A review of historical data might show, for example, that a low-bidding SC could end up costing more in rejected submittals and excess punch-list items.
Tighten future bids and project scheduling by bringing the data to post-project autopsies. Tease out why line items ran over or under budget. In the man-hour part of the equation, evaluate whether capabilities are in place to bid for the next job and how to deploy the best people for greatest advantage and productivity.
Risk Mitigation Through Data Analysis
In the never-ending chase for risk mitigation, data becomes a valuable ally.
Identify potential schedule risks by tracking average RFI and submittal response times. Let history help predict the impact on the timeline.
Monitor safety observations to identify trends and proactively address recurring issues. If people aren’t wearing protective gear or not tying off properly, the problem could be systemic, requiring a different approach to training.
And, importantly, implement an organization-wide safety-awareness culture that functions uninterrupted on the jobsite. Use the safety data collected to develop a “good catch” program, rewarding workers with gift cards or merchandise for calling out safety violations, or plan pizza parties for every 100 days without an accident.
The MEP data gathered and applied to creation of building information models (BIM) can also be applied to mitigating risk and promoting efficiencies.
Project leaders can use BIM’s coordination-issues feature to predict possible pathways from clash to RFI to change event and, finally, to potential change order.
BIM findings can anticipate MEP-related patterns and proclivities among players in the process, such as a certain architect’s preferences in fixtures. MEP subcontractors can input real-time data into their mobile BIM viewers, generating a steady stream of emerging items to address before they become full-blown predicaments.
Data Refinement and Advanced Analytics
After data-driven mindsets become the norm in the organization and across jobsites, it’s time to start shaping the parameters for what to collect and how to use it.
These tactics, steeped in shaping data development to the company’s distinct needs, can hone the process for heightened effectiveness.
Refine definitions of risk.
Clearly define what risk is regarding safety, budget and productivity. For example, zero in on the key performance indicators, uncovering a schedule that’s losing steam, such as average response times for submittals and RFIs.
Use PMS’ enhanced reporting features.
Take advantage of the reporting features of PMS to customize data fields with relevant filters, creating subsets that will feed targeted reports and analyses.
Keep questioning the findings and conclusions.
If there’s a hole in the data, add filters that extract the information needed to answer questions regarding financials, resource management, project execution and other critical functions.
Don’t let data grow stale.
For more accurate findings, continuously evaluate data quality, completeness and the processes for collection and review.
Establish regular cadences for running and reviewing reports.
Train everyone at all levels of the organization to understand the importance of quality data input and their role in keeping data fresh, timely and applicable to project goals.
Courses about construction.
For construction.
Unlock your career potential with our free educational courses on Health & Safety, Data in Construction, and more.
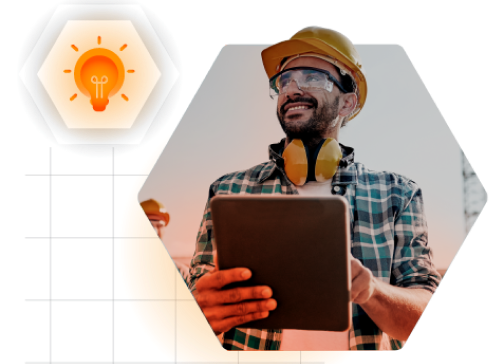
Creating Transformation Through Data
To senior leadership, distance from the day-to-days of the jobsite can skew the image and make it blurry. Complete, quality data brings the picture into focus, while structured processes empower PXs and PMs to extract actionable findings.
By targeting pain points and constantly tweaking procedures, project leadership can keep progress on schedule, minimize and mitigate risk and institutionalize operational efficiencies for a more profitable project and a well-built structure.
Was this article helpful?
Thank you for your submission.
0%
0%
You voted that this article was . Was this a mistake? If so, change your vote here.
Scroll less, learn more about construction.
Subscribe to The Blueprint, Procore’s construction newsletter, to get content from industry experts delivered straight to your inbox.
By clicking this button, you agree to our Privacy Notice and Terms of Service.
Thank you!
You’re signed up to receive The Blueprint newsletter from Procore. You can unsubscribe at any time.
Categories:
Tags:
Written by
Anthony Verdiglione
Senior Strategic Product Consultant | Procore Technologies
Anthony Verdiglione is a seasoned construction professional and accomplished project manager with more than two decades of solid experience. Well-versed in nearly every construction discipline, Anthony adds immediate value to any transaction, leveraging his vast base of knowledge to drive projects, profits, and the industry. A true champion of construction, he works tirelessly to stay abreast of the latest trends while passing that value on to the customers he dutifully services.
View profileDiane McCormick
Writer | Procore Technologies
26 articles
Diane McCormick is a freelance journalist covering construction, packaging, manufacturing, natural gas distribution, and waste oil recycling. A proud resident of Harrisburg, PA, Diane is well-versed in several types of digital and print media. Recognized as one of the premier voices in her region, she was recognized as the Keystone Media Freelance Journalist of the Year in 2022 and again in 2023.
View profileExplore more helpful resources

Low-voltage Systems: A New Frontier for MEP Contractors
From design through commissioning, low-voltage system designers and the MEP trades are colleagues. They work together to provide the systems that make buildings safe, comfortable, efficient and equipped for modern...
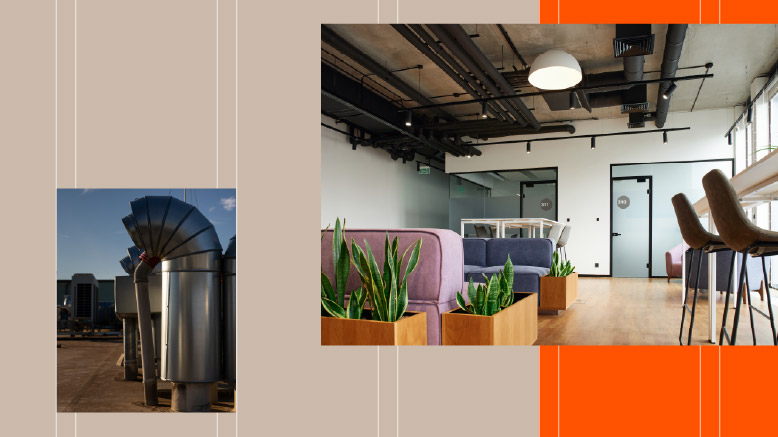
Comfort Mood: Making MEP Central to Occupant Comfort
In many post-COVID-19 projects, occupant comfort has transitioned from a “nice to have” to a “must have.” It’s infused into collaborations from the earliest phases of design and preconstruction. That...
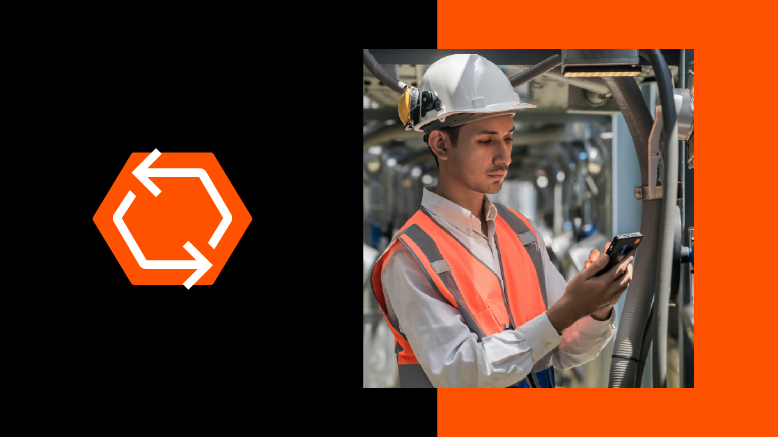
The MEP Lifecycle: How Contractors Can Benefit from Thinking Ahead
From the beginning of a project, MEP contractors should be thinking about the lifecycle of their systems. Prioritizing the lifecycle early in the process helps MEP trades influence design, select...
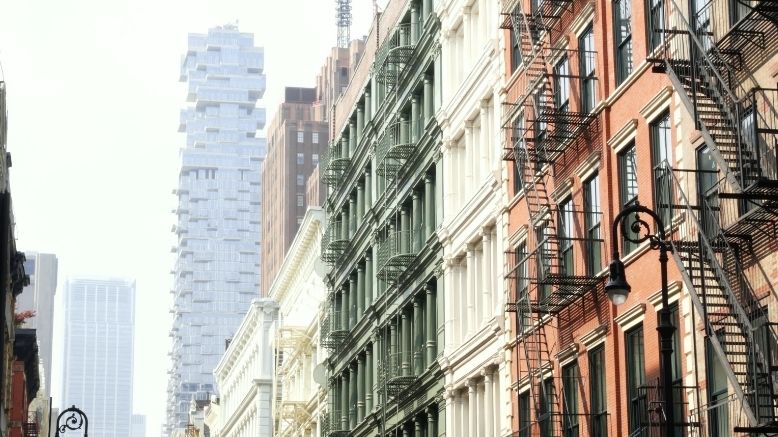
Retrofitting Aging Infrastructure: 5 Essentials for Managing MEP Risk
MEP contractors help preserve aging infrastructure by bringing systems to contemporary standards in sustainability, comfort and accessibility. Although the opportunities are unique, retrofits of existing buildings present known obstacles and...
Free Tools
Calculators
Use our calculators to estimate the cost of construction materials for your next project.
Templates
Find a template to help you with your construction project tasks.
Material Price Tracker
Get the latest U.S. retail prices and view historical trends for common building materials.
Glossary
Explore key terms and phrases used in the industry.