— 8 min read
Construction Sustainability: The Impact of Climate-Conscious Building
Last Updated May 14, 2024
Kacie Goff
Contributing Writer
79 articles
Kacie Goff is a construction writer who grew up in a construction family — her dad owned a concrete company. Over the last decade, she’s blended that experience with her writing expertise to create content for the Construction Progress Coalition, Newsweek, CNET, and others. She founded and runs her own agency, Jot Content, from her home in Ventura, California.
Last Updated May 14, 2024
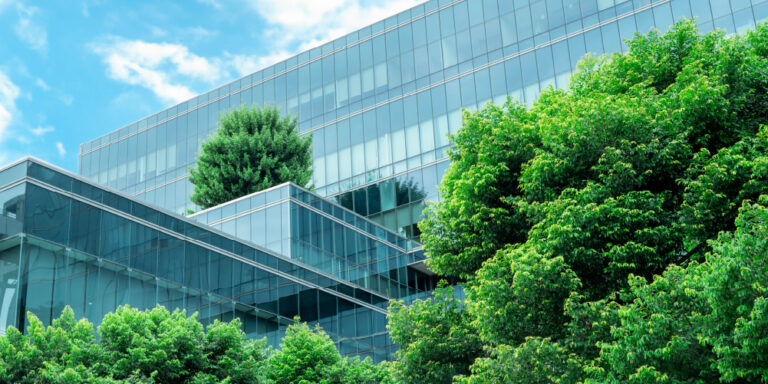
Amid the increasing severity of natural disasters worldwide, the urgent search for climate change solutions often leads to the construction industry, which accounts for 37% of global emissions according to the United Nations Environment Programme. With such a significant share, efforts to enhance construction sustainability are critical to reducing greenhouse gas emissions.
Sustainability in construction extends far beyond mere emissions management. It encompasses a comprehensive approach that includes responsible resource use and a nuanced understanding of environmental impacts that range from global warming to more localized issues like water use, acid rain, and the destruction of natural habitats. A broader view is advocated — one that encompasses all environmental aspects, not just carbon emissions.
Ultimately, there’s a big opportunity to protect the environment by moving toward construction sustainability. As an added bonus, many measures will also protect project owners’ bottom lines.
Table of contents
The 2 Sides of Construction Sustainability
To give a broad definition, construction sustainability means the responsible use of resources paired with mindfulness of the effect of that use on the environment.
There are a lot of facets to consider here. In fact, sustainability is such a broad topic that experts tend to break it into separate components — for instance, decarbonization. When speaking on decarbonization in the construction industry, they usually look at two separate ways that buildings impact the environment:
- Embodied carbon: This accounts for the carbon emissions related to the actual construction of the building. It encompasses everything from the extraction of the raw materials required for the structure and the transportation of those materials to the emissions from equipment during building and the waste of material that goes unused. This also accounts for the project's end-of-life, or their demolition and transportation of demolished materials.
- Operational carbon: This measures the carbon impact of a building once it’s completed and used. The carbon footprint that a building creates as its users heat it, cool it, turn on its lights, flush its toilets, etc. is totaled as part of that structure’s operational carbon.
All of this said, carbon — meaning greenhouse gas emissions, usually measured as kilograms of carbon dioxide equivalent — isn’t the only impact of erecting a building. Construction sustainability also seeks to offset other adverse impacts, like:
- Acidification
- Adverse human and wildlife impact
- Damage to local water sources
- Contribution to landfills
- Destruction of natural habitats
- Eutrophication
- Natural resource depletion
- Photochemical ozone formation
When stakeholders want to move toward construction sustainability, they can generally make the biggest impact by focusing on the areas that are most relevant to them geographically. Projects in Australia may focus primarily on mitigating ozone depletion, for example, while construction sites in Southern California may implement water-conscious practices.
Scopes of Embodied Carbon
The first step to limiting embodied carbon is understanding it. As the construction industry tries to do that, it has assigned three different scopes. The people involved in a project have direct responsibility for scope 1 emissions, while they have a hand in but don’t directly control the other three. To give some examples:
- Scope 1 emissions are within a company’s control, like the emissions its fossil fuel-burning vehicles and equipment generate as they run.
- Scope 2 emissions are an indirect consequence of the company’s activities, like the emissions created from lighting the jobsite. The company may turn on the lights, but the power source from which they’re pulling is another entity’s jurisdiction.
- Scope 3 emissions aren’t produced by the company and aren’t a direct result of their actions. Take, for example, the carbon impact of products that the company buys from suppliers.
Companies looking for a place to start with limiting their environmental impact should begin with a focus on scope 1 emissions. As they ramp up their construction sustainability initiatives, they can scale up to focus on scope 2 and scope 3 emissions.
Standards for Construction Sustainability
A plethora of standards and strategies for sustainable building practices exist, with international and regional standards such as BREEAM, LEED, and Passive House, DGNB, and Miljöbyggnad providing guidance. Circular construction models emphasize resource reuse and recycling, encouraging creative and eco-conscious building strategies. Examples include using excess heat from a busy train station to warm nearby buildings or cold water from natural sources to cool data centers:
Beyond these standards, eco-conscious building strategies are also driving change. Some project managers now focus on circularity, for example. The circular construction model aims to make resources as useful as possible for as long as possible, with an emphasis on reusing and recycling materials.
Circularity can also encourage the creative use of resources. In Stockholm, for example, the heat generated from a busy train station is used to warm nearby buildings. Other Northern European countries use cold water from natural sources to cool down data centers, then direct that water to homes to use once it’s hot.
Whichever standards or strategies companies enact, the goal is the same: to improve construction sustainability and move away from construction processes that generate excess emissions, waste and other negative environmental impacts.
Roadblocks to Sustainability in the Construction Industry
One of the biggest hurdles blocking construction sustainability is a lack of tracking mechanisms. A 2022 analysis of the environmental impacts of construction waste found that stakeholders at more than 95% of projects said waste was a challenge. Even so, only 57% of construction companies record and measure the volume of material waste, and 75% of companies don’t have any staff members assigned to handle waste.
Ultimately, with different entities handling different parts of the project — often each with their own materials and equipment — understanding a project’s environmental impact often presents a significant challenge. Plus, telling a site manager that it’s their responsibility to track sustainability metrics on top of all of the other work they’re already doing often isn’t welcome news. Layer on the tight timelines that construction projects come up against and it’s not surprising that limited resources go toward monitoring these metrics.
To make the whole situation even more complex, what’s sustainable on one project may not be the most environmentally conscious choice on another. Take prefabricated construction as an example. These types of buildings may have a smaller carbon footprint at the outset. But if the prefabricated building needs to travel far, the emissions from the required transportation might offset those gains.
Movement Toward Sustainability
People tend to think building more sustainably is always more expensive, but that’s not the case. In fact, studies have shown the opposite. High production costs tend to go hand in hand with negative environmental impacts.
Change is happening as companies see how protecting the environment can help them protect their bottom line. Many projects now focus on repurposing existing buildings rather than demolishing them and building new ones. Similarly, many owners now demand compliance with green construction standards because buildings that use less heat, water, energy, etc. have lower operating costs. Some companies in Europe have started building embodied carbon reporting into their contractual agreements.
Ultimately, for sustainability in the construction industry to move forward, project owners and contractors need to build it in so that it’s the default. For example, most construction professionals don’t think twice about adhering to safety standards. The processes and safeguards are designed to improve safety at each project step. Sustainability needs the same level of embedding into established processes.
A Place to Start: Reducing Concrete Waste
Two materials are the most carbon-intensive in terms of extracting the raw materials, transporting them, and installing them: structural steel and concrete.
Because structural steel is so expensive, most companies do an excellent job of minimizing waste. Concrete, on the other hand, is relatively cheap. As a result, overages are common.
Let’s say that in order to erect the minimum viable product of a certain building, you need 100 tons of concrete. To build in a coefficient of safety, the structural engineer calls for 120 tons. When the general contractor interprets those designs, they order 130 tons to make sure the project is covered. The concrete subcontractor might send 140 tons to the site so they won’t be held liable for a shortage, and the supplier might send 150 tons of aggregate just to be safe. Ultimately, 50% of the concrete in this example would go to waste.
Companies looking for an easy construction sustainability win can start here. Consider that wasted concrete a mistake, the same way you would if it was poured incorrectly and had to be jackhammered out. Through site drawings and material invoices, stakeholders should have the data on what the project calls for, what was ordered, and what actually got delivered to the site. From there, they can begin to pinpoint overages and make changes to limit them.
While many companies will struggle to get to a zero loss yield (meaning there is no waste at all), each step taken to reduce concrete waste goes a long way toward minimizing a project’s embodied carbon footprint.
Using concrete waste as a starting point can help companies build the muscle to monitor environmental impact. To further develop competency there, they may choose to start calculating shadow costs, e.g., $1 for every 1 kilogram of embodied carbon. This can help project managers to make decisions that benefit not just the company’s financial outlook, but also its environmental impact.
Was this article helpful?
Thank you for your submission.
100%
0%
You voted that this article was . Was this a mistake? If so, change your vote here.
Scroll less, learn more about construction.
Subscribe to The Blueprint, Procore’s construction newsletter, to get content from industry experts delivered straight to your inbox.
By clicking this button, you agree to our Privacy Notice and Terms of Service.
Thank you!
You’re signed up to receive The Blueprint newsletter from Procore. You can unsubscribe at any time.
Categories:
Tags:
Written by
Ed Neuman
View profileKacie Goff
Contributing Writer | Procore Technologies
79 articles
Kacie Goff is a construction writer who grew up in a construction family — her dad owned a concrete company. Over the last decade, she’s blended that experience with her writing expertise to create content for the Construction Progress Coalition, Newsweek, CNET, and others. She founded and runs her own agency, Jot Content, from her home in Ventura, California.
View profileExplore more helpful resources

Building Culture: How Investing in People Can Transform Construction
This article is part of a series exploring the transformation of RNGD, a contractor with offices in Louisiana, Tennessee and Alabama. RNGD evolved from a conventional general contractor to a...

Maximizing Performance by Making Data Visible and Accessible
This article is part of a series exploring the transformation of RNGD, a contractor with offices in Louisiana, Tennessee and Alabama. RNGD evolved from a conventional general contractor to a...

Embracing Offsite Construction for a More Sustainable Future
This article is part of a series exploring the transformation of RNGD, a contractor with offices in Louisiana, Tennessee and Alabama. RNGD evolved from a conventional general contractor to a...
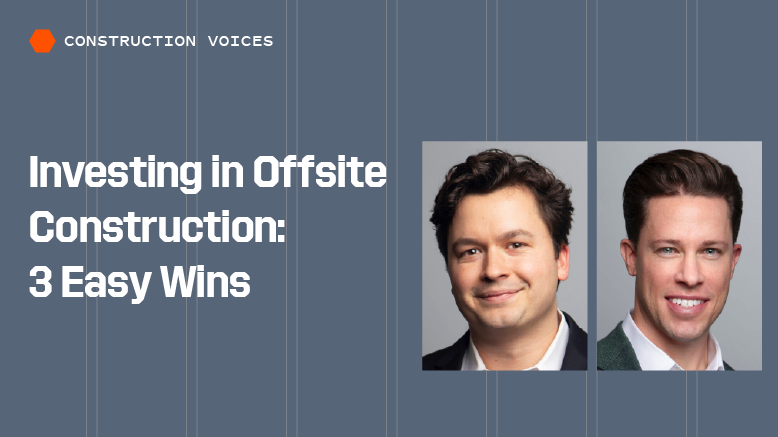
Investing in Offsite Construction: 3 Easy Wins
This article is part of a series exploring the transformation of RNGD, a contractor with offices in Louisiana, Tennessee and Alabama. RNGD evolved from a conventional general contractor to a...
Free Tools
Calculators
Use our calculators to estimate the cost of construction materials for your next project.
Templates
Find a template to help you with your construction project tasks.
Material Price Tracker
Get the latest U.S. retail prices and view historical trends for common building materials.
Glossary
Explore key terms and phrases used in the industry.