Related Articles
— 5 min read
Construction Procurement Strategy, Methods and Processes
Last Updated Aug 28, 2025
Nicholas Dunbar
Content Manager
60 articles
Nick Dunbar oversees the creation and management of UK and Ireland educational content at Procore. Previously, he worked as a sustainability writer at the Building Research Establishment and served as a sustainability consultant within the built environment sector. Nick holds degrees in industrial sustainability and environmental sciences and lives in Camden, London.
Zoe Mullan
27 articles
Zoe Mullan is an experienced content writer and editor with a background in marketing and communications in the e-learning sector. Zoe holds an MA in English Literature and History from the University of Glasgow and a PGDip in Journalism from the University of Strathclyde and lives in Northern Ireland.
Last Updated Aug 28, 2025
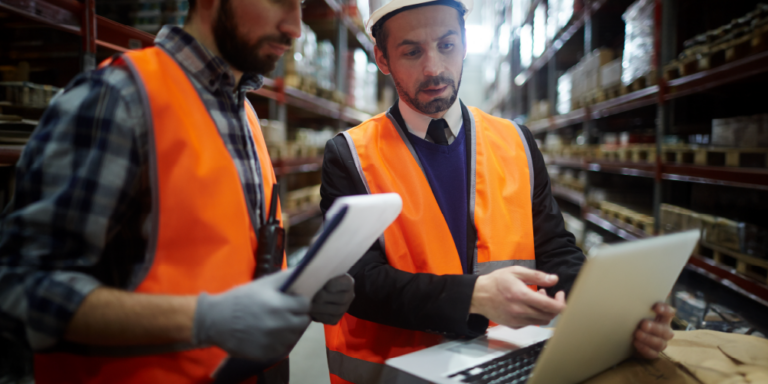
Every successful construction project depends on securing the right materials, labour, and services at precisely the right time and cost. Procurement serves as the engine that drives this coordination, quietly ensuring everything reaches the site when needed while keeping projects moving forward. From permit acquisition to subcontractor management, procurement influences every construction phase.
To master construction procurement strategy, methods, and processes, professionals must understand what the term truly encompasses, why the process matters, and which key activities and methods drive smooth operations.
Table of contents
What Construction Procurement Entails
Construction procurement involves acquiring all goods, services, and resources necessary to complete a project. This includes everything from concrete and steel to plant hire, labour, logistics, and legal permissions.
Rather than simply placing orders, construction procurement includes strategic planning, supplier vetting, commercial negotiations, and ongoing contract management. This comprehensive approach ensures resources arrive when teams need them, meet required standards, and support overall project delivery.
Consequently, a well-executed procurement process forms the backbone of any successful project. It drives timelines, safeguards budgets, and helps teams work through complexity with confidence.
Why Strategic Procurement Matters
Construction projects typically face tight timelines and strict budgets. However, a well-planned construction procurement strategy eases these pressures by ensuring vital resources arrive on time while maintaining supply chain adaptability when changes occur. Strategic procurement delivers:
Precise timing
Reliable procurement prevents delays by coordinating material and labour resources to ensure availability when and where teams need them.
Budget Control
Early supplier engagement and intelligent contract negotiation reduce cost overruns and eliminate waste.
Quality assurance
Thorough supplier vetting and clear specifications maintain quality standards from project inception.
Sound procurement practices prevent compliance issues, delivery delays, and scope change complications.
Strategic procurement builds stronger long-term relationships across the supply chain. By partnering with trusted suppliers and contractors, project teams gain consistency and flexibility to adapt to unforeseen changes without compromising outcomes.
Core Elements of Construction Procurement
Every well-executed procurement plan relies on core activities that bring control and coordination to projects. These activities span procurement's complete life cycle – from initial planning to contract close-out – and determine how effectively project teams respond to challenges. Construction procurement includes these essential elements:
Needs Identification
Before procurement begins, teams must clearly define project requirements. This includes material specifications, equipment needs, labour requirements, and service expectations. Additionally, teams must consider timing constraints, quality standards, and compliance obligations.
Sourcing and Selection
Once teams establish needs, they source suppliers and contractors through market research, prequalification processes, and partner evaluation. This assessment considers potential partners' capabilities, experience, and commercial alignment with project objectives.
Contract Negotiation and Award
Procurement teams then negotiate commercial terms, delivery schedules, and service expectations before finalising agreements. Well-structured contracts establish the foundation for optimal performance throughout projects while promoting greater accountability.
Contract Management
Importantly, procurement continues after contract signing. Ongoing contract management – including progress monitoring, dispute resolution, and compliance verification – keeps projects on track throughout their duration.
Supply Chain Management
Construction success depends on smooth material, equipment, and information flow. Effective supply chain management ensures timely deliveries, maintains adequate stock levels, and facilitates clear communication across multiple parties.
Regardless of project size or complexity, these elements help construction teams secure appropriate resources while maintaining control over quality, timing, and costs.
Procurement Methods in Construction
Construction projects vary enormously in scope. From straightforward builds to complex infrastructure developments, procurement strategies must meet vastly different demands. The chosen procurement method shapes everything from project leadership to risk and responsibility distribution. Common procurement methods include:
Traditional (Design-Bid-Build)
This method separates design and construction phases. Contractors bid on fully developed design documents, establishing clear roles and responsibilities from the outset.
Design and Build
A single contractor handles both design and construction phases. This integrated approach reduces client risk, streamlines communication, and often shortens project timelines.
Construction Management
Teams appoint a construction manager to coordinate and oversee multiple trade packages. Rather than holding contracts directly, they act on the client's behalf, offering enhanced flexibility, clearer cost control, and greater delivery transparency.
Management Contracting
Similar to construction management, this method sees the management contractor hold trade contracts directly. This approach shifts more responsibility to the contractor while allowing project delivery in overlapping phases to save time.
Framework Agreements
These establish long-term agreements with pre-approved suppliers or contractors for recurring or multi-phase work. Common in public sector projects, they eliminate the need to tender for each new work package.
Each method carries different implications for cost certainty, programme control, and risk allocation. Therefore, aligning the construction procurement strategy with project goals before proceeding becomes crucial.
In the UK, both public and private sector procurement practices continuously evolve to adapt to new regulations clearly established in government legislation.
The Construction Procurement Process
While procurement processes vary depending on projects and chosen methods, most follow similar patterns. Each stage builds upon the previous one, establishing groundwork for smooth delivery and ongoing control. Here's how typical procurement processes unfold:
Define Requirements
Teams establish project needs, including materials, services, timelines, specifications, and performance standards.
Conduct Market Research
Teams explore suppliers and contractors who meet project requirements. This stage commonly includes prequalification, capability assessments, and performance reviews.
Issue Tenders or Solicit Bids
Teams prepare and release tender documents, requests for proposals (RFPs), invitations to tender, or requests for quotations (RFQs). This step may include site visits or clarification rounds.
Evaluate Bids and Select Suppliers
Teams assess submissions based on cost, capability, quality, compliance, and delivery risk. They may invite shortlisted suppliers for negotiations.
Negotiate and Award Contracts
Teams finalise commercial terms, responsibilities, and deliverables before awarding and signing contracts.
Mobilise and Deliver
Suppliers and contractors prepare to begin work or deliver goods. This phase often includes kick-off meetings, scheduling, and early site coordination.
Monitor Performance and Manage Contracts
Throughout construction, procurement teams oversee contract compliance, delivery performance, and issue resolution. They make adjustments responding to project changes as needed.
Final Thoughts
Procurement plays a central role in construction projects, defining how teams source and manage materials, labour, and services. With the right strategy, procurement helps projects run more smoothly, reducing costs and risks throughout delivery lifecycles.
As projects grow in scale and complexity, the ability to coordinate procurement effectively – from early planning stages through contract close-out – becomes increasingly important. Whether teams manage procurement in-house or through digital platforms, clear procurement practices establish strong foundations for project success.
Categories:
Tags:
Written by
Nicholas Dunbar
Content Manager | Procore
60 articles
Nick Dunbar oversees the creation and management of UK and Ireland educational content at Procore. Previously, he worked as a sustainability writer at the Building Research Establishment and served as a sustainability consultant within the built environment sector. Nick holds degrees in industrial sustainability and environmental sciences and lives in Camden, London.
View profileZoe Mullan
27 articles
Zoe Mullan is an experienced content writer and editor with a background in marketing and communications in the e-learning sector. Zoe holds an MA in English Literature and History from the University of Glasgow and a PGDip in Journalism from the University of Strathclyde and lives in Northern Ireland.
View profileExplore more helpful resources
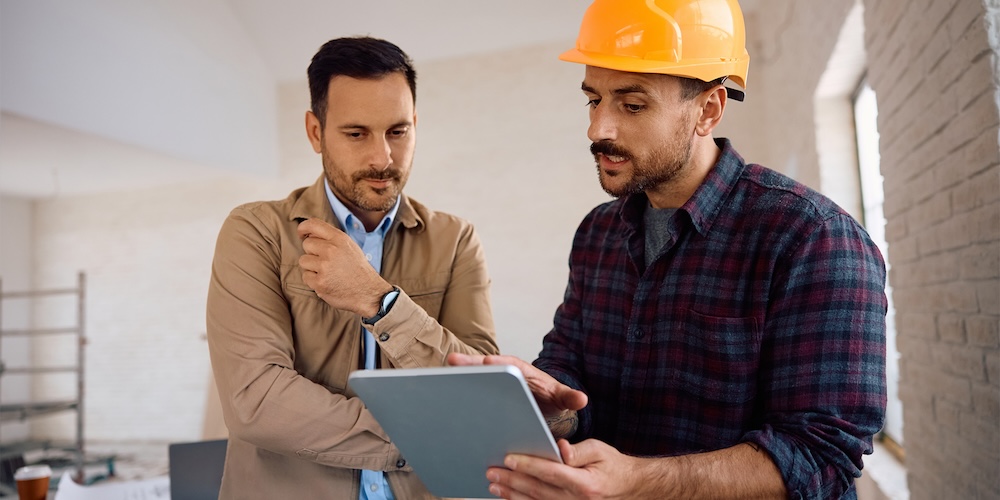
From Tender to Contract: How Digital Workflows Reduce Risk & Improve Accountability
The buy-out phase of construction, from tender award through contract, remains one of the riskiest stages of the process. Why? Quite simply, the sheer volume of information handled by construction...
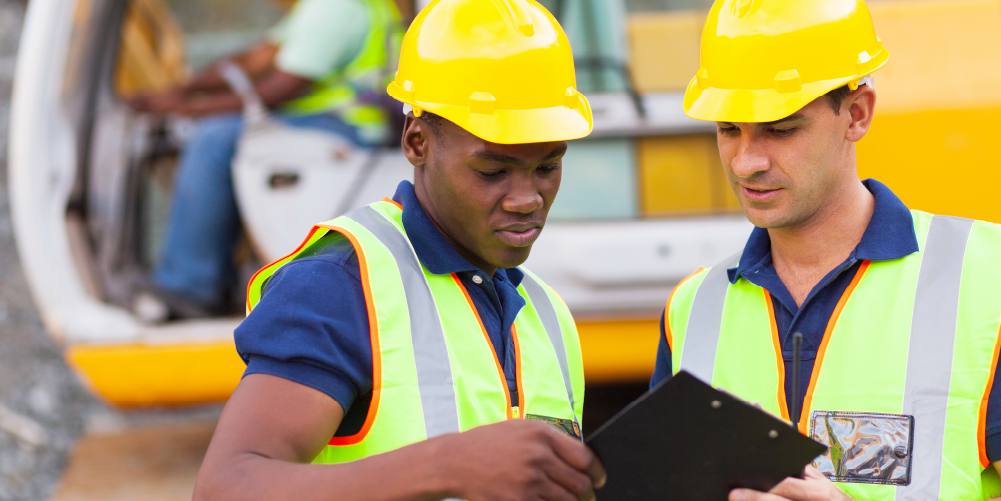
Streamlining the Buy-Out: Reducing Scope Gaps, Delays & Margin Erosion
There isn’t a single construction project that doesn’t get impacted by how well—or poorly—the buyout phase is managed. In fact, the post-tender subcontract stage of the procurement process is crucial:...
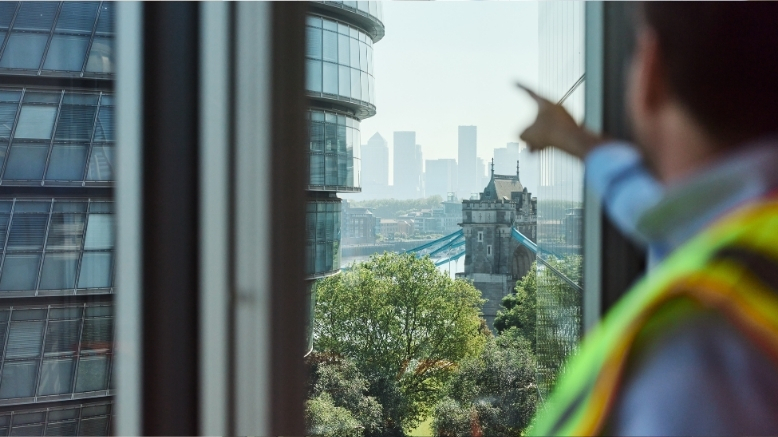
Procurement Intelligence: How AI Is Helping Contractors Make Smarter Commercial Decisions
The UK construction sector is under sustained cost and schedule pressure. While the out-of-control materials cost volatility of the pandemic era is, thankfully, behind us, the industry is still experiencing...

Construction Cost Estimating: a Step-by-Step Guide
Construction estimating is a crucial process in the construction industry, as it involves accurately predicting the cost of a project before work begins. Within the United Kingdom, construction estimating is...