— 8 min read
A Construction Expert’s Guide to BIM
Last Updated Jul 30, 2025
Tom Noctor
Senior Product Manager, International
16 articles
Having worked in construction for many years both on the ground as an electrician and in the design space in roles such as BIM Manager, I witnessed the highly inefficient operations of our industry and also the amount of waste generated from project delivery. I am a Digital Construction Technologies advocate @Procore Technologies, supporting and guiding the construction industry in adopting/utilising technology to deliver projects in a lean sustainable manner.
Jakir Hyder
Senior Sales and Solutions Consultant
Experienced construction engineer supporting the industry in digital transformation using experience and knowledge gained from Tier 1 contractor through customer focused and outcome based solution design during the presales process.
Last Updated Jul 30, 2025
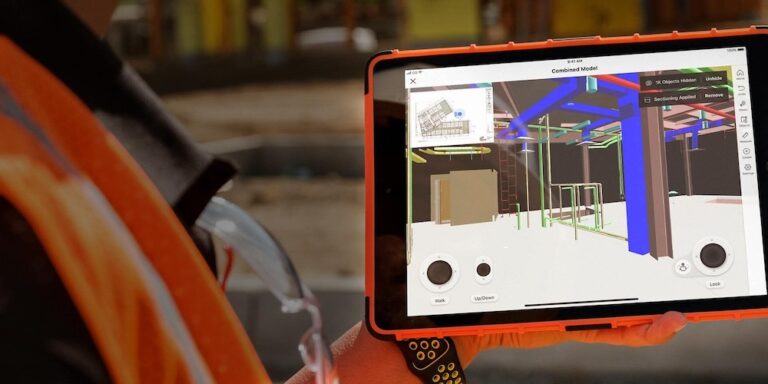
Builders have always relied on precisely-designed sets of plans to construct great buildings. As the industry rapidly digitises, the adoption of Building Information Modelling (BIM) has surged to combat rework, project delays, and cost overruns. Thanks to advancements in 3D modelling, BIM solutions now enable main contractors, specialty contractors, and owners to virtually build a structure before breaking ground.
BIM methodologies have been around for decades, but many companies still don’t realise its full benefits because they fail to achieve widespread adoption of the software solutions they deploy. By integrating greater on-site accessibility, improved interoperability, and easier collaboration tools, BIM can significantly enhance project outcomes.
Table of contents
What is BIM?
Building Information Modelling (BIM) is a methodology that allows construction professionals to work collaboratively, harnessing software to plan, design, manage, and build projects. A BIM model is often referred to as a “digital twin,” containing not just 3D representations, but also data about:
- Project schedules and timelines
- Maintenance schedules
- Costs and budgets
- Equipment and material requirements
- Risk assessments and more
Learn about the future of the built environment - Read Procore's Future State of Construction report
Learn how contractors, subcontractors, and project teams can take advantage of new opportunities to boost efficiency and profitability over the next decade. Download the report to get your roadmap to the future state of construction.
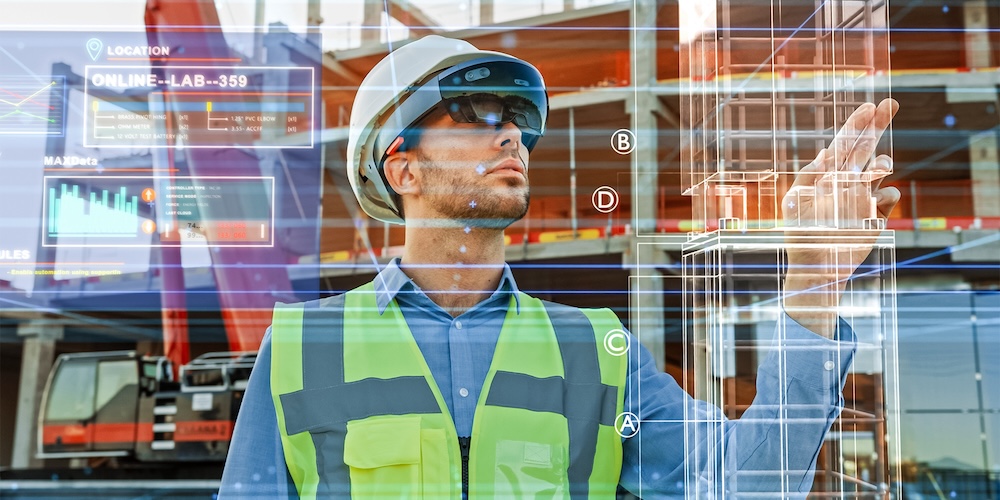
BIM serves as a platform for real-time communication and updates. When one stakeholder makes a change, everyone else can see and adapt immediately, reducing confusion and conflicts.
BIM creates detailed digital representations, known as "virtual models," which allow construction teams to test various design options and visualise potential outcomes before actual construction begins. These models act as a digital twin of the project, integrating 3D representations with additional data such as materials, scheduling, and costs. By simulating different scenarios, stakeholders can identify potential issues and optimise designs, ensuring that the final construction aligns closely with the intended vision. This capability not only reduces errors but also facilitates stakeholder engagement by providing a clear visualisation of the project's future.
What are the different levels of BIM?
Level 0 BIM
Characterised by traditional paper-based, 2D drawings with no digital collaboration.
Level 1 BIM
Involves the use of Computer Aided Design (CAD) for digital drawings. It commonly incorporates a common data environment (CDE) to manage and store documents. Many Tier 2 and Tier 3 companies operate at this level.
Level 2 BIM
A legal requirement for many public sector projects, Level 2 BIM involves creating 3D models composed of separate sub-models (e.g., structural, architectural, mechanical, electrical, and plumbing). These sub-models can be combined (federated) to detect clashes and resolve problems before construction begins.
Level 3 BIM
Often called integrated BIM or openBIM, it merges all data into a single, centralised model. Workers update and retrieve information in real time, which enhances collaboration and reduces errors. Level 3 also involves 4D and 5D BIM capabilities.
4D BIM
This adds the time element (scheduling) to the 3D model, enabling animations and simulations of the construction process.
If I have a 10-story residential tower with offices, restaurants, and cafes on the bottom floor, the 4D BIM model will show us how this is going to be built. You could imagine an animation of a building being constructed in front of you.
Jakir Hyder
Senior Sales and Solutions Consultant
Oracle
5D BIM
Integrates costing into the model, allowing project teams to price different elements of the build and generate Bills of Quantities automatically. This capability helps break down specific costs and track budgets more effectively.
Beyond 5D: 6D and 7D BIM
- 6D BIM introduces sustainability and energy performance into the model.
- 7D BIM adds facility management data to the mix, proving useful for clients once the building is finished and in use.
8 Benefits of BIM in Construction
BIM offers advantages throughout a project’s lifecycle, from preconstruction through to closeout. Below are seven key benefits that link directly to real-world efficiency gains.
1. Better Planning
4D BIM is a powerful tool because it merges scheduling data with a 3D model. Stakeholders get an end-to-end overview of a project, making it easier to spot clashes and inefficiencies early.
2. Improved Collaboration
BIM excels at breaking down information silos. It gives architects, engineers, builders, and subcontractors a single source of truth.
BIM helps teams collaborate better because everybody has access to an accurate, up-to-date model of the construction project.
Jakir Hyder
Senior Sales and Solutions Consultant
Oracle
When stakeholders have reliable access to 3D coordinated models and shop drawings, design changes become transparent, reducing errors.
3. Better Cost Estimation
Cost estimation can be time-consuming and prone to mistakes. 5D BIM links 3D building elements with scheduling and cost data, helping construction managers rapidly compare design choices. This reduces rework and shortens the feedback loop for budget-related issues.
4. More Efficient Building
When on-site teams can trust the information in the model, they’re less likely to misinterpret designs.
“Once we’ve got things coordinated in the model using the Co-ordination Issues tool and the trades are viewing the model using the Models tool, they’ll install their items in the proper coordinated space. That prevents rework.”
— Jeremy Felix, Okland Construction
This added clarity leads to accurate on-site execution and stronger alignment with the original design intent.
5. Reduced Risk
By giving teams the ability to compare existing site conditions to 3D models, BIM helps prevent costly mistakes. As described by Haselden Construction:
“They can see that tangible number in front of them. These VDC guys probably saved us $100,000 on a project because we didn’t have to do all this rework—which means we didn’t have to reorder materials, we didn’t have to respend man-hours, and we didn’t have to extend our programme.”
Thanks to BIM, well-informed decisions can be made before problems escalate, keeping projects within budget and on schedule.
6. Improved Safety
Rework and project delays can lead to rushed work and a higher chance of accidents. BIM empowers teams to plan ahead, spot issues in advance, and minimise surprises in the field. Better planning and coordination translate into fewer safety hazards.
7. Smoother Project Close Outs
6D BIM supports facilities management and ongoing operations by linking all relevant attributes (installation dates, performance specs, etc.) to the model. This makes it simpler to track maintenance, sustainability requirements, and future renovations.
8. Interoperability
Interoperability is a core strength of BIM, helping cross-disciplinary collaboration among architects, engineers, contractors, and other stakeholders. BIM tools support the integration of various sub-models (e.g., structural, mechanical, electrical) into a cohesive model. This approach aids in detecting and resolving clashes before construction whilst also ensuring that all parties operate from a single source of truth. The ability to exchange information freely across different software platforms and disciplines enhances communication, reduces misunderstandings, and leads to more informed decision-making processes.
Data-driven Decision Making
BIM centralises and updates key data in real time. When any stakeholder alters the design, the system automatically refreshes cost estimates, scheduling, and clash detections. This ensures decisions are always based on consistent, up-to-date information.
Clients now understand the level of information that goes into the BIM process. They might demand a digital twin to be handed to them at the end.
Jakir Hyder
Senior Sales and Solutions Consultant
Oracle
Potential Challenges
Skills Shortages
Shifting from 2D to BIM workflows requires upskilling. Construction professionals and trades need to be trained to read digital drawings and models. This can be time-consuming and expensive, but many companies find the investment worthwhile.
High Initial Costs
BIM demands significant initial costs in hardware, software, and training. However, this pays off through fewer mistakes and the ability to compete for larger projects—especially public-sector contracts requiring BIM Level 2.
Funds required for the right hardware are a barrier. Software companies are trying to make it easier, but there is still a way to go.
Jakir Hyder
Senior Sales and Solutions Consultant
Oracle
Perceived Lack of Demand
Some smaller firms see no immediate client pressures to adopt BIM. Yet those who invest in BIM often unlock broader markets and can serve a more diverse client base, including governmental bodies that mandate BIM for compliance.
Innovative Uses of BIM
There are many creative applications of BIM that go beyond design and construction:
One innovative use I saw early in my career, about 10 years ago, involved sequencing. We were given a concept tender 3D model… I modelled that piece of kit moving through the building and identified any obstructions.
Jakir Hyder
Senior Sales and Solutions Consultant
Oracle
BIM can also work with Virtual Reality (VR) and Augmented Reality (AR) to let clients virtually walk through a project. This immersive approach helps them visualise how the end result will look, reducing last-minute changes.
The Evolution of BIM
With demands for faster timelines and tighter margins, BIM provides a glimpse into the project’s future and allows professionals to fix issues before they arise. As technology progresses, BIM evolves:
- 4D BIM already includes scheduling.
- 5D BIM adds cost estimation.
- 6D BIM factors in energy performance and sustainability.
- 7D BIM addresses facility management.
- 8D BIM (occupational health) is on the horizon, along with VR, AI, and IoT integrations for predictive modeling and an even deeper digital twin experience.
Frequently Asked Questions
What’s the difference between BIM and CAD?
CAD focuses on creating 2D or 3D drawings of a building or its components. BIM expands on this by integrating data about scheduling, materials, costs, and more to form a holistic project model.
When was BIM developed?
BIM’s roots trace back to the 1970s with the introduction of 3D modelling. By the early 2000s, advances in software led to more widespread adoption of BIM for construction.
What’s the future for BIM?
Future BIM will harness AI, IoT, and predictive tools for deeper analysis. It will also incorporate sustainability, energy performance, and facility management into a single, unified system.
Are there any standards or frameworks for BIM?
Yes. ISO 19650 is an international standard for information management in BIM. The UK BIM Framework outlines guidelines for British-based projects, building upon PAS 1192 standards.
BIM is changing construction for the better. By uniting 3D models with scheduling, costs, sustainability data, and collaborative workflows, BIM helps construction teams reduce risk, improve safety, and complete projects more efficiently. Whether starting with Level 1 or aiming for Level 3, adopting BIM is an investment that pays off in both the short and long term—and positions companies to thrive as the industry continues to innovate.
Categories:
Tags:
Written by
Tom Noctor
Senior Product Manager, International | Procore Technologies
16 articles
Having worked in construction for many years both on the ground as an electrician and in the design space in roles such as BIM Manager, I witnessed the highly inefficient operations of our industry and also the amount of waste generated from project delivery. I am a Digital Construction Technologies advocate @Procore Technologies, supporting and guiding the construction industry in adopting/utilising technology to deliver projects in a lean sustainable manner.
View profileJakir Hyder
Senior Sales and Solutions Consultant | Oracle
Experienced construction engineer supporting the industry in digital transformation using experience and knowledge gained from Tier 1 contractor through customer focused and outcome based solution design during the presales process.
View profileExplore more helpful resources

A Guide to Construction Risk Assessments in the UK
Construction is one of the United Kingdom’s most dynamic industries, driving economic growth, shaping skylines and creating essential infrastructure. But with opportunity comes risk. From worker safety to cost pressures...

Construction Cash Flow Forecast: A Step-by-Step Guide
In construction, sound financial management revolves around the cash flow strategy: knowing when money will come in, how much will go out, and whether the gap between the two is...
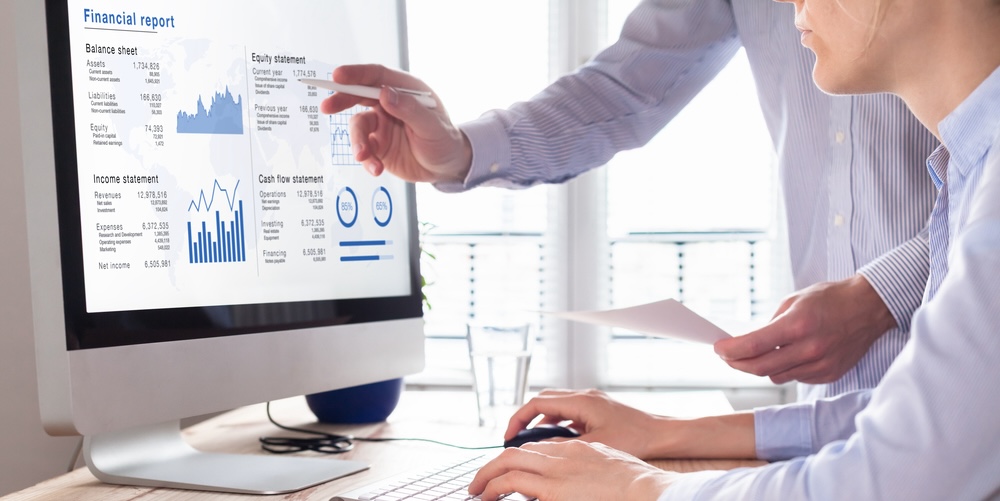
Holistic Portfolio Insights for Proactive Resource and Cost Management in Construction
Holistic portfolio insights help teams to get an understanding of progress, costs, resources and more. Construction companies rely on insights into their portfolios to make proactive decisions about their projects...
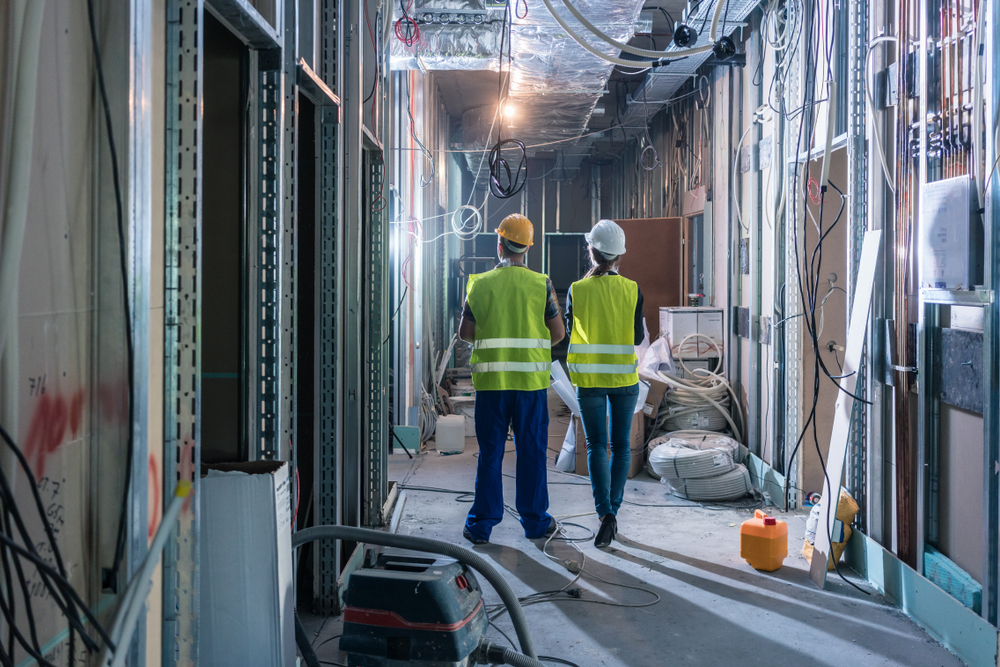
Inspection and Test Plans (ITPs): A Comprehensive Guide to Construction Quality Control
An Inspection and Test Plan (ITP) is far more than a compliance checklist – it’s a proactive quality control strategy that ensures every phase of a construction project meets the...