— 11 min read
What Is Commissioning in Construction? Purpose, Process, and Best Practices
Last Updated Aug 28, 2025
Samantha Nemeny
24 articles
Sam—Samantha if she’s feeling particularly academic—has spent a decade in content marketing, with eight years focused on Australia’s construction industry. She has a knack for making complex ideas easy to understand, turning industry jargon into clear, engaging stories. With a background in SEO and marketing, she’s spent the past three years at Procore, helping industry professionals navigate the world of construction with content that’s both insightful and easy to digest.
Last Updated Aug 28, 2025

During project closeout, owners expect more than a finished building. They want systems that work, safety measures that hold, and performance that matches the design.
Commissioning helps deliver on that expectation. It provides a structured process to verify that every system, from HVAC to fire projection, functions as intended and aligns with the project’s original requirements.
This article explains commissioning in construction, why it matters, and how to approach it with the rigor required for reliable outcomes.
Table of contents
What Is Commissioning in Construction?
Commissioning is a quality assurance process that applies rigorous testing, inspection, and documentation to a building's systems during and after construction. It covers installation quality, operational performance, system calibration, and alignment with the project’s technical specifications.
In Australian commercial construction, commissioning documents confirm that all systems meet the Owner’s Project Requirements (OPR), design intent, and compliance obligations before handover. Ultimately, they verify whether a building’s systems perform according to standards and the original project intent.
Six Key Aspects of Commissioning
Commissioning includes a defined set of activities that repeat across each stage of construction. The six aspects below outline how teams structure, manage, and execute the process from planning to handover.
1. Systematic Process
Commissioning follows a step-by-step structure that applies across planning, construction, testing, and handover. Each stage builds on documented checks and verification tasks to confirm that systems are installed and ready for operation.
This structured approach supports traceability through checklists, status logs, and test records, helping teams verify installation milestones, track unresolved issues, and meet handover requirements with confidence
2. Quality Assurance
Commissioning adds a layer of quality control by verifying documented performance targets and compliance benchmarks across trades and systems. It supports compliance with the National Construction Code (NCC), and contributes to sustainability goals under frameworks like Green Star.
These validations are typically based on functional tests, trend logs, and sign checklists, providing clear evidence that quality benchmarks have been met.
3. Early Engagement
Commissioning adds the most value when it’s integrated from the earliest stages of project planning. During the pre-design phase, owners and design teams define performance targets and embed commissioning requirements into project documentation.
This early alignment improves coordination, clarifies trade responsibilities, and reduces the risk of late-stage changes or delays
4. Detailed Commissioning Plan
A commissioning plan defines the scope, responsibilities, schedule, and success criteria for the commissioning process. It ensures all parties understand what systems will be tested, how performance will be measured, and who is responsible for each activity. Commissioning plans typically include:
- Defined roles for the commissioning provider, design team, builder and subcontractors
- Testing procedures, acceptance criteria, and documentation requirements
- Budget allowances for commissioning activities, including test execution and coordination
- Scheduling aligned with key construction milestones and access requirements
- Trade scopes that clearly assign commissioning responsibilities to subcontractors
5. Testing and Verification
Testing and verification confirm whether building systems, like HVAC, fire protection, and plumbing, perform under real-world conditions before handover. Commissioning providers coordinate with subcontractors and consultants to observe performance, log deficiencies, and confirm when systems are ready for signoff.
6. Collaboration and Communication
Commissioning depends on strong coordination across the project team, including the owner, builder, subcontractors, consultants, and commissioning provider. Timely communication is essential for resolving issues, sequencing work, and tracking readiness for testing.
Common tools include RFIs, submittals, and defect lists to manage information flow and close out open items. Digital platforms also support live issue tracking, version control, and documentation handover at project completion.
Stages of the Commissioning Process
Commissioning spans the entire project lifecycle, from initial planning through post-occupancy. Each stage plays a specific role in confirming that building systems meet performance targets and comply with contractual and regulatory obligations.
Pre-Design Phase
Commissioning begins by establishing the Owner’s Project Requirements, which define system performance goals, energy targets, and sustainability outcomes.
Teams also identify documentation needs early in the process. This often includes preparing a draft Owner’s Project Requirements document based on the intended use, applicable regulations, and manufacturer specifications.Design Phase
The design team translates the Owner’s Project Requirements into a Basis of Design and integrates commissioning criteria into specifications and drawings. This stage typically involves creating system-level test protocols and documenting performance expectations.
Some teams use Building Information Modelling to identify system coordination issues before construction begins.Construction Phase
Contractors and subcontractors review commissioning responsibilities during early coordination. Pre-functional inspections confirm that installations are ready for testing. For example, mechanical or electrical systems may be checked against commissioning checklists to ensure correct installation.
Coordination meetings are used to track progress and resolve sequencing or access issues.Functional Acceptance Phase
Performance testing occurs under operating conditions to confirm that key systems function as intended.
This stage includes verifying HVAC airflow and temperature output, assessing plumbing functionality, and testing life safety systems such as fire alarms and emergency lighting. Any deficiencies are logged and assigned for correction.Occupancy and Initial After-Care
Once the building is occupied, systems are fine-tuned based on actual use.
Teams calibrate sensors, adjust control set points, and refine operational sequences to improve efficiency and occupant comfort. For example, building management system controls may be adjusted to better align with daily usage patterns.Warranty Phase
System performance is reviewed across different seasons, and any issues are addressed under the contractor’s warranty terms. For example, cooling systems may be assessed during peak summer conditions to ensure they meet performance expectations and do not require corrective action.
Ongoing and Continuous Commissioning
Commissioning continues after handover through regular monitoring and scheduled reviews. Annual performance checks are commonly used to confirm energy efficiency and to meet long-term targets such as those required for Green Star certification.
Owner or Developer
The owner initiates commissioning during pre-design and ensures project goals are clearly defined and documented. They remain responsible through handover, verifying that all commissioning deliverables are complete and accurate.
- Define the Owner’s Project Requirements
- Approve the final commissioning report
- Confirm delivery of training and documentation
- Support seasonal or ongoing re-commissioning as needed
Commissioning Provider or Agent
The commissioning provider leads the commissioning process from planning through final reporting. They manage test execution, document issues, and confirm all systems meet performance expectations.
- Develop the commissioning plan
- Coordinate and observe system testing
- Identify and track deficiencies
- Prepare test reports and the final commissioning report
Design Team
Architects and engineers ensure system designs meet the Owner’s Project Requirements and support commissioning throughout the project. They respond to site issues and update design documentation as conditions evolve.
- Align designs with commissioning scope and performance goals
- Include commissioning specs in project documentation
- Attend key tests and revise designs if needed
- Maintain and update as-built drawings
Contractors and Subcontractors
Builders and trades are responsible for installing systems to the required standards and preparing them for testing. They also help resolve any deficiencies identified during commissioning.
- Install systems in line with design intent and commissioning requirements
- Complete pre-functional checklists
- Provide documentation and access for testing
- Address installation issues or test failures
Operations and Maintenance Team
The operations team takes over at handover and maintains performance over time. They receive training, manage documentation, and participate in re-commissioning if needed.
- Attend system training sessions
- Receive and manage O&M documentation
- Monitor system performance post-handover
- Assist with warranty reviews and ongoing optimisation
Commissioning Documentation and Reports
Commissioning is not complete without clear, structured documentation.
The commissioning report provides formal evidence that systems meet performance expectations and is included in project closeout documentation. It serves as a long-term reference for maintenance teams and helps ensure the building operates as designed.
Unlike start-up reports, which only confirm that systems turn on and perform basic functions (such as a pump starting or lights powering on), the commissioning report verifies whether those systems meet defined performance targets. For example, it shows whether the HVAC system delivers specific airflow rates, maintains temperature ranges, and responds appropriately to automation controls.
A complete commissioning report typically includes:
- Executive summary and compliance statement: Summarises findings and confirms that commissioned systems meet all project and regulatory requirements.
- Completed checklists and test procedures: Details the tests conducted across each system, including pass criteria and verification steps.
- Performance data and trend logs: Present output data such as air volume, pressure, temperature, and flow rates to create a baseline for future reviews.
- Deficiency log with resolution dates: This log outlines issues identified during testing, the corrective actions taken, and when each item was resolved.
- Sign-off sheets and training records: Confirms that the commissioning process was witnessed and that the operations team received required training and documentation.
The commissioning report is included in the project’s closeout documentation, confirming that systems function as intended before final payment is released. It also reduces risk and liability by providing written proof of system performance.
Often, a commissioning report is required alongside as-built drawings, warranties, and operation manuals.
Counteracting the Most Common Commissioning Challenges
Commissioning delivers long-term value, but poor planning or execution can limit its impact. The challenges below frequently affect commercial projects.
Late Start or Compressed Schedule
Commissioning is often left too late in the program, leaving insufficient time for thorough testing and issue resolution. Late-stage problems are harder to fix and can delay handover.
Best practice: Integrate commissioning into the project schedule from pre-design to ensure adequate time and resourcing.
Poor Coordination Across Trades
Overlapping responsibilities can lead to confusion, especially where scopes intersect. Without a clear lead, issues are either missed or resolved inefficiently.
Best practice: Define commissioning responsibilities within each subcontractor’s scope and appoint the general contractor as the coordination lead.
Inadequate Documentation
Commissioning produces large volumes of records, including checklists, test reports, and logs. Disorganised documentation can delay project closeout and complicate future audits.
Best practice: Use shared templates and structured systems to standardise documentation and maintain consistency across teams.
Front-Loaded Budgets or Cost-Cutting
Commissioning is sometimes underfunded due to budget pressure late in the project. This results in incomplete testing, rushed reporting, or unverified systems.
Best practice: Allocate a dedicated commissioning budget from project start and treat it as essential to risk management and compliance.
Limited Operations and Maintenance Team Involvement
Facilities teams are often brought in too late to influence setup or receive effective training. This leads to improper use or missed maintenance requirements post-handover.
Best practice: Involve operations staff during final testing and training to support a smoother transition and long-term performance.
Best Practices for Successful Commissioning for Construction Projects
Commissioning must be executed with structure, clarity, and technical discipline to prevent delays, rework, and underperforming systems. The following practices help ensure reliable performance outcomes and a smooth handover.
1. Integrate Commissioning Early
Embed commissioning in the project from day one by taking the following actions:
- Add commissioning milestones to the master program, including design coordination, equipment start-up, and final verification
- Include commissioning requirements in Division 01 specifications, particularly Section 01 90 00
- Allocate dedicated time for testing within the construction schedule
- Flag interdependencies early to prevent delays caused by unavailable services
- Make the commissioning kickoff meeting a contractual requirement during pre-construction
2. Define Clear Acceptance Criteria
Implement these strategies to make acceptance criteria measurable, aligned, and enforceable:
- Document pass and fail thresholds in the commissioning plan, linked to the Owner’s Project Requirements and Basis of Design
- Use quantifiable benchmarks such as airflow rates, temperature variance, or system pressure
- Require formal approval of all test scripts from both the commissioning agent and the design engineer
- Specify testing tolerances, durations, and required operating conditions
- Include clear retesting protocols for systems that fail initial verification
3. Use an Independent Commissioning Agent
Maintain objectivity and technical rigour by following these commissioning agent practices:
- Engage an agent with no contractual ties to the builder or design team
- Define scope in the contract, including test witnessing, issue tracking, and final sign-off
- Require the agent’s presence at start-up meetings and readiness inspections
- Empower the agent to pause or defer testing if prerequisites are not met
- Set a regular meeting cadence for reporting, coordination, and resolution
4. Leverage Digital Tools
Use the following digital processes to improve traceability, reporting, and efficiency:
- Use mobile checklists during site walks to capture test results and deficiencies in real time
- Store all commissioning documentation in a centralised cloud platform with access controls
- Apply timestamped digital signatures to validate test completions and observations
- Track testing progress and unresolved issues through live dashboards
- Pull trend data from building systems to verify long-term performance
5. Provide Thorough Training and Turnover Documentation
Support long-term building performance by completing these training and handover steps:
- Conduct hands-on training before handover, covering controls, safety systems, and maintenance procedures
- Record all sessions and include the files in the final turnover package
- Compile manuals, as-builts, warranties, and standard operating procedures into a structured handover binder in both digital and hard copy formats
- Include quick-reference guides for essential actions such as adjusting HVAC set-points or responding to system alarms
- Verify training completion and document delivery with signed checklists or training logs
Commissioning ensures that building systems perform as intended
It connects design intent to operational outcomes by verifying that each system performs to project requirements. When done right, commissioning reduces risk, supports compliance, and helps deliver safer, more reliable buildings.
Categories:
Tags:
Written by
Samantha Nemeny
24 articles
Sam—Samantha if she’s feeling particularly academic—has spent a decade in content marketing, with eight years focused on Australia’s construction industry. She has a knack for making complex ideas easy to understand, turning industry jargon into clear, engaging stories. With a background in SEO and marketing, she’s spent the past three years at Procore, helping industry professionals navigate the world of construction with content that’s both insightful and easy to digest.
View profileExplore more helpful resources

Take 5 Safety: A Practical Layer in Construction Risk Management
Construction sites don’t run on plans alone. They run on people making decisions in unpredictable conditions — where one missed hazard can lead to serious injury, lost time, or legal...

Site Safety Plan: What It Is, WHS Requirements, and How to Create One That Works
For project leaders, a site safety plan is more than a compliance requirement. It is an operational blueprint for keeping people safe, work flowing, and projects protected from costly disruption....
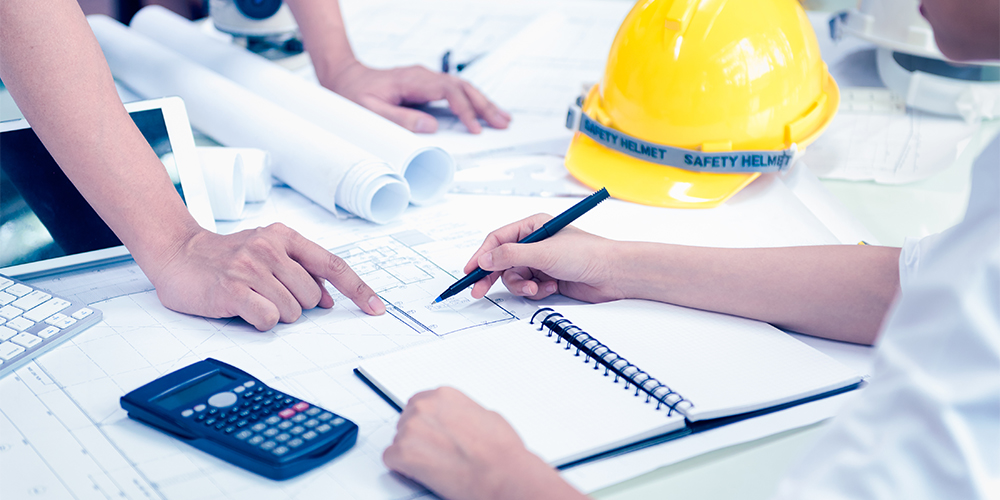
Construction ERP Explained: Why Builders Need a Unified System
As Australian construction projects grow in value and complexity, the pressure on operational teams is intensifying. Site supervisors, safety managers, and project engineers are expected to deliver precision execution—on tighter...
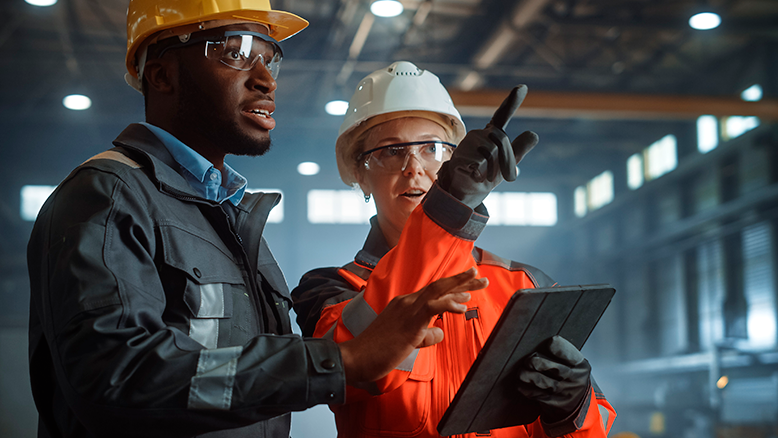
How to Prepare and Use a SWMS to Manage High-Risk Construction Work
On Australian job sites, Safe Work Method Statements (SWMS) are more than a legal requirement, they’re a critical part of delivering high-risk construction work without indecent, delay or regulatory exposure....