— 4 min read
Ctrl + Build: The Carbon Code – Why Embodied Emissions Are The Next Big Test For Data Centre Builders
Last Updated Aug 28, 2025
Paul Acker
As a Strategic Product Consultant at Procore, Paul Acker boosts construction financials through expert Procore implementation and ERP integrations. He translates complex technical and financial problems into practical solutions, improving cash flow, reporting, and project margins for construction firms, developers, and subcontractors. Paul's blend of construction management, financial optimisation, and an MBA - backed by success leading multi-billion dollar system and data migrations - ensures technology delivers tangible commercial results and drives efficiency.
Last Updated Aug 28, 2025
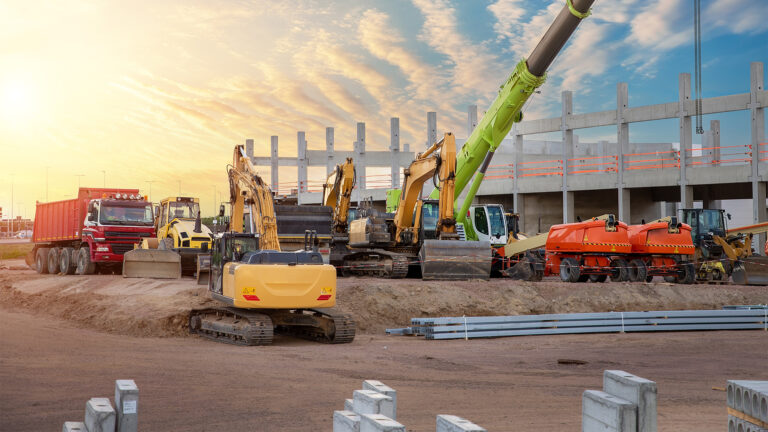
Data centre operators are under pressure to decarbonise – and operational efficiency is no longer enough. The carbon locked into construction materials is now under the spotlight. For builders, that means new expectations, new workflows and a new kind of accountability on site.
Table of contents
Looking Beyond Operational Emissions
Carbon conversations in the data centre world tend to revolve around operations: cutting consumption, switching to renewables and improving performance.
And with good reason. In Australia, data centres already consume around 5% of total electricity. CBRE expects this to climb to 8% by 2030.
But there’s a quieter carbon story playing out behind the scenes: the emissions locked in before the servers even arrive.
Steel and concrete – two of construction’s most carbon-intensive ingredients – dominate the emissions profile of a typical data centre. Globally, cement and steel account for roughly 15% of all CO₂ emissions.
More than 60% of the world’s largest companies are now setting net zero targets. To achieve them, they must address all sources of emissions – including those embedded in the construction of buildings.
This puts new expectations on builders and contractors.
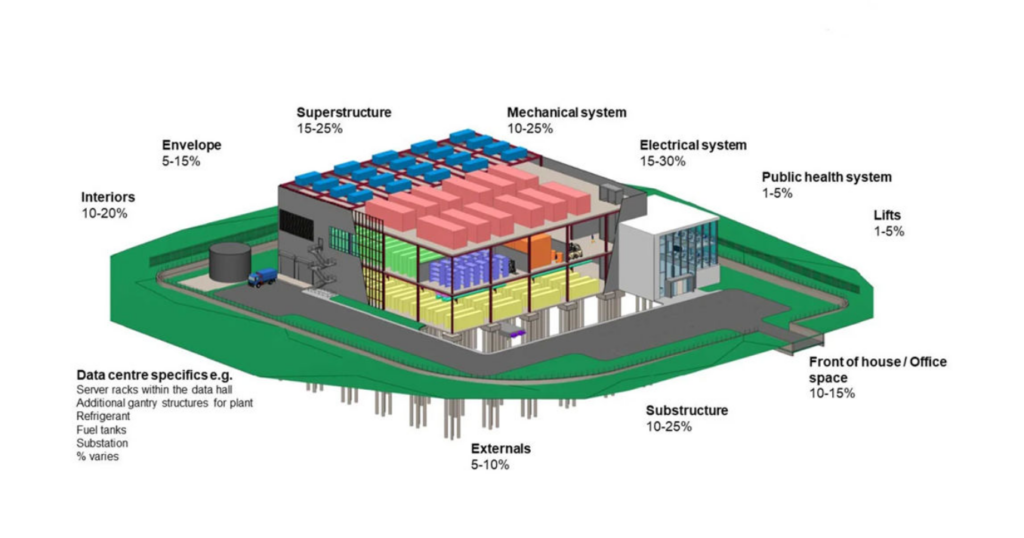
Visualisation of components to consider in WLCA for data centres and an approximate breakdown of lifecycle module A-C emissions
Source: Adapted from Arup, 2022. Illustrative only.
Why Embodied Carbon Matters
Embodied carbon emissions are generated during a building’s entire lifecycle – from raw materials extraction to transportation of building products, and from powering construction machinery right through to demolition and disposal.
The World Green Building Council estimates that 38% of global emissions come from our buildings. Operational emissions account for 29%. The remaining 11% are generated during design, delivery or demolition.
As Australia’s electricity grid decarbonises and more buildings are powered by 100% renewable electricity, the proportion of emissions created during construction will grow. The Green Building Council of Australia says as much as 85% of Australia’s built environment emissions will be “locked in” before anyone steps through a door – or switches on a server.
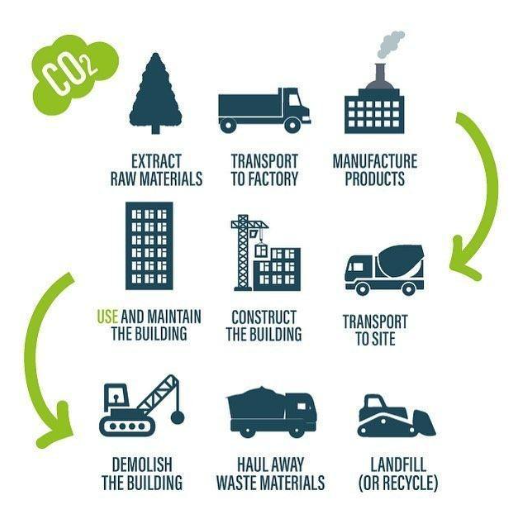
Embodied Carbon Sources Across the Building Lifecycle
Hidden Emissions, Big Impact
When it comes to data centre construction, one big source of emissions stands out: concrete. Concrete alone can represent up to 80% of a data centre’s embodied carbon emissions.
According to analysis by global architecture firm Gensler, reducing the amount of concrete used in a data centre through efficient structural design is the single most effective strategy. This is followed by material quality. High-performance aggregates and optimised mix designs can reduce the amount of cement needed.
But here’s the kicker. Gensler’s analysis suggests many of the emissions linked to supply, transport and rework aren’t captured – because they aren’t tracked.
Everyone’s focused on kilowatts. But before the first server goes in, you’ve already locked in tonnes of CO₂. That comes with reputational and regulatory risk.
Paul Acker
Cracking the Carbon Code
Some project teams are already embedding embodied carbon tracking into digital workflows. Using Procore, they can:
- Benchmark embodied carbon for materials and major plant
- Coordinate delivery schedules to align with lower-carbon material availability
- Report embodied carbon metrics alongside traditional quality and cost data.
The goal? A single source of truth and a clear audit trail for data centre operators under pressure to prove their ESG performance.
Table 1: Who Holds the Key to Embodied Carbon?
Stakeholder | Key Responsibility | Embodied Carbon Opportunity | How Procore Helps |
---|---|---|---|
Developers and Owners | Set targets and carbon goals | Establish whole-of-project carbon benchmarks | Centralised platform for setting, sharing and tracking targets |
Designers and Engineers | Specify structure, materials and performance standards | Optimise for low-carbon, efficient design, and EPDs | Embed carbon metrics into design reviews and tender documentation |
Contractors and Builders | Procure materials, manage trades and quality assurance | Reduce rework, track product emissions, align with low-carbon materials | Quality assurance templates linked to emissions benchmarks and install data |
Suppliers | Deliver certified low-carbon materials | Provide EPDs, innovate | Upload data, certifications and delivery information to platform |
Sustainability Consultants | Monitor progress and report against benchmarks | Verify Scope 3 and lifecycle emissions, support ratings submissions | Export carbon data for NABERS, Green Star or custom reports |
Key Takeaways
- Embodied carbon is the next emissions frontier in data centre delivery
- Constructors and contractors will be expected to track and reduce construction-phase emissions
- Structured digital workflows are essential to capture and report embodied carbon
- Procore enables carbon visibility across materials, trades and timelines.
As data centre operators face growing pressure to limit embodied carbon, constructors and contractors who deliver clarity and accountability through data will earn trust – and win work.
See what’s coming in construction over the next decade.
Download the Future State of Construction Report for insights, trends, and innovations shaping the industry over the next 8–10 years.
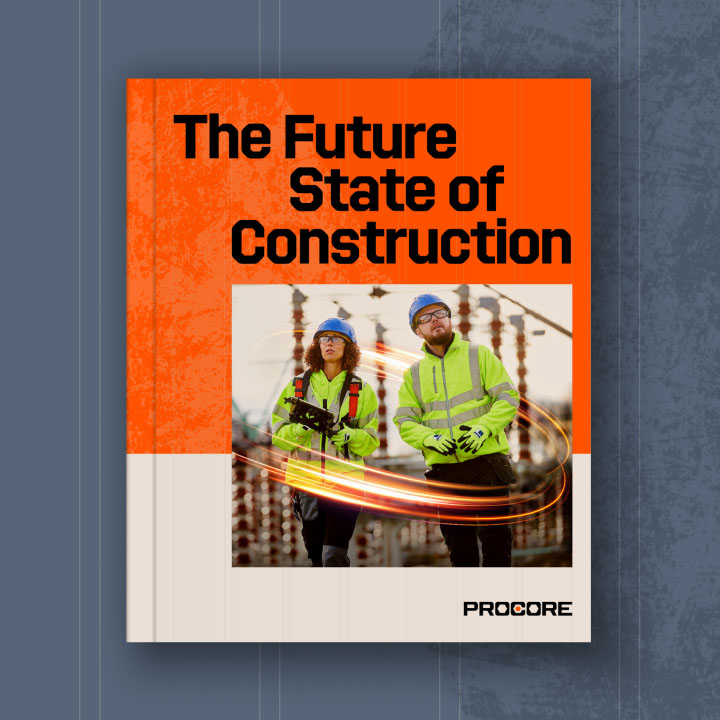
this is part of the series
Ctrl + Build
Categories:
Tags:
Written by
Paul Acker
As a Strategic Product Consultant at Procore, Paul Acker boosts construction financials through expert Procore implementation and ERP integrations. He translates complex technical and financial problems into practical solutions, improving cash flow, reporting, and project margins for construction firms, developers, and subcontractors. Paul's blend of construction management, financial optimisation, and an MBA - backed by success leading multi-billion dollar system and data migrations - ensures technology delivers tangible commercial results and drives efficiency.
View profileExplore more helpful resources

Take 5 Safety: A Practical Layer in Construction Risk Management
Construction sites don’t run on plans alone. They run on people making decisions in unpredictable conditions — where one missed hazard can lead to serious injury, lost time, or legal...

Site Safety Plan: What It Is, WHS Requirements, and How to Create One That Works
For project leaders, a site safety plan is more than a compliance requirement. It is an operational blueprint for keeping people safe, work flowing, and projects protected from costly disruption....
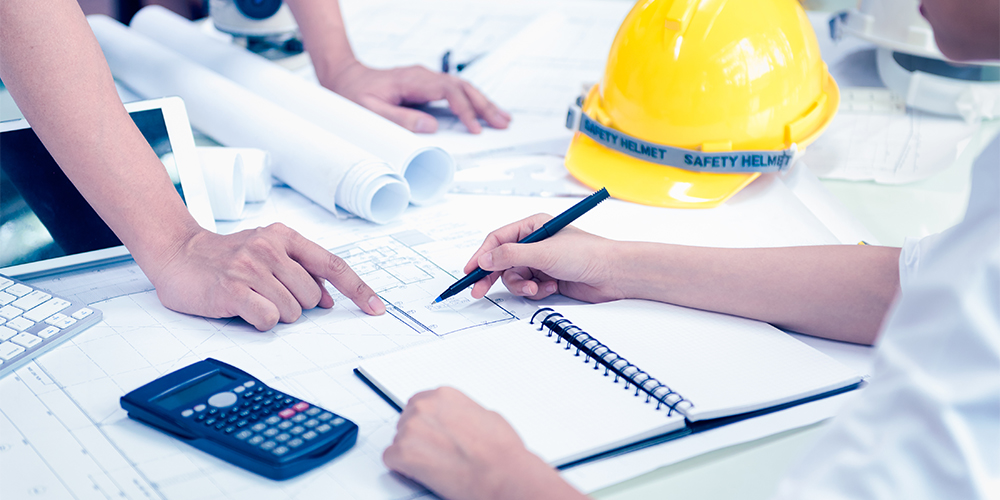
Construction ERP Explained: Why Builders Need a Unified System
As Australian construction projects grow in value and complexity, the pressure on operational teams is intensifying. Site supervisors, safety managers, and project engineers are expected to deliver precision execution—on tighter...
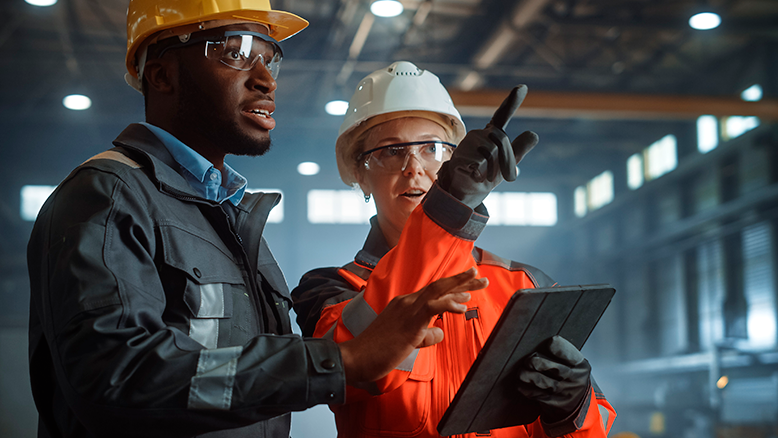
How to Prepare and Use a SWMS to Manage High-Risk Construction Work
On Australian job sites, Safe Work Method Statements (SWMS) are more than a legal requirement, they’re a critical part of delivering high-risk construction work without indecent, delay or regulatory exposure....