— 9 min read
Construction Inventory Management: How to Track Materials, Tools, and Costs
Last Updated Aug 28, 2025
Josh Krissansen
25 articles
Josh Krissansen is a freelance writer with two years of experience contributing to Procore's educational library. He specialises in transforming complex construction concepts into clear, actionable insights for professionals in the industry.
Last Updated Aug 28, 2025
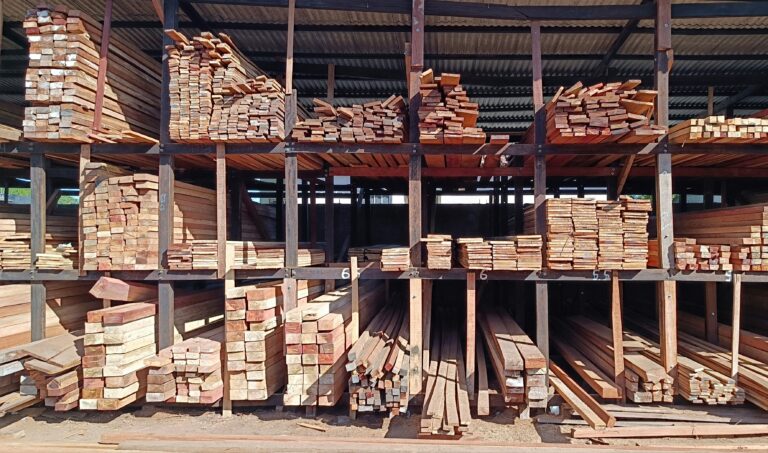
Inventory management is often treated as a back-office task, but its significance—and its effects—are front and center, extremely visible, and clearly connected to project success.
How strategically and efficiently materials, tools, and equipment are managed impacts everything, from details like subcontractor productivity to the primary levers of project success (and even financial growth), like margin maintenance.
And as projects grow in scale and complexity, the operational stakes get riskier because they’re directly connected to how well you’re ‘doing’ inventory oversight.
It’s in a development project’s best interests to structure inventory practices in ways that support better outcomes. In this guide, we’ll examine how to achieve that worthy aim, explore the most relevant functions on Australian construction sites, and the steps experienced contractors take to prevent the common failures that drive up cost and delay.
Table of contents
What is Construction Inventory Management?
Construction inventory management underpins cost control, productivity, and schedule certainty on Australian construction sites. It provides a structured process for tracking, controlling, and managing materials, tools, and equipment across the project lifecycle.
The process covers everything required for delivery, including owned or rented plant, consumables, and trade materials. Accurate oversight ensures teams know what’s available, where, and how it’s being used.
Poor inventory control can erode efficiency and inflate costs on complex builds, where tight margins and sequencing matter.
Core functions include:
- Tracking: Capturing real-time data on materials and equipment in use, including timber, concrete, PPE, and plant
- Control: Enforcing accountability to reduce overuse, theft, and unplanned purchasing
- Optimisation: Managing stock levels based on forecast demand, storage capacity, and supply chain reliability
Importance of Effective Inventory Management in Construction
Inventory management is a strategic function supporting financial control, project performance, and site safety.
Its operational aspects are critical to Australian contractors delivering projects on time and within budget. This is especially important in an environment with cost volatility and unpredictable supply chains.
Well-managed inventory enables accurate forecasting, reduces waste, and improves productivity. It also helps mitigate risks tied to delivery delays, labour inefficiencies, and material handling issues.
Accurate budgeting and cost control
- Tracks usage to prevent overspending
- Reduces urgent off-site purchases that inflate costs
- Improves forecasting using historical consumption data
Reduced downtime and increased productivity
- Ensures materials and equipment are available when needed
- Minimises delays caused by missing items or slow supply chains
- Enables better labour coordination by avoiding idle time
Improved project timelines and reliability
- Supports scheduling through the timely procurement of long lead-time items
- Prevents disruptions caused by shortages or misplaced assets
- Provides real-time visibility to support faster adjustments on-site
Enhanced safety through organised material handling
- Maintains a tidy jobsite to reduce trip hazards
- Ensures proper storage to protect material integrity
- Secures high-value tools to limit unauthorised access
Key Components of Construction Inventory Management
Inventory tracking and control
Digital platforms give contractors real-time visibility over materials, consumables, and tools across multiple locations. Inventory categories typically include:
- Consumables such as fasteners, sealants and PPE
- Building materials such as timber, plasterboard and steel
- Tools and equipment such as drills and compactors
These systems track usage, monitor movement, and provide accurate records to support forecasting. Combined with clear accountability protocols, they help prevent overuse, reduce loss, and eliminate duplicate purchasing.
Procurement and supplier management
Forecasting future needs based on past consumption helps avoid reactive purchasing and supports more stable pricing.
Pro Tip
Procurement plans should align with construction schedules and lead time risks. Diversifying the supplier base reduces exposure to delays, while early use of RFIs ensures specifications are confirmed before orders are placed.
Storage solutions
Storage approaches should reflect the project phase, access needs and available space. To improve efficiency and reduce waste:
- Schedule just-in-time deliveries to limit on-site clutter
- Secure high-value tools and materials to prevent theft
- Inspect stored inventory regularly to identify damage early
Material and tool distribution
Efficient distribution ensures that materials and equipment are available when and where needed. This involves coordinating deliveries from central storage or staging areas and anticipating jobsite requirements in advance.
Communication between the warehouse, site, and office helps avoid delays and idle labour.
Technology and coordination
Inventory platforms centralise data and improve collaboration between office and site teams. QR codes, barcoding and RFID enable faster check-in and tracking across sites. Integrating inventory with cost tracking and scheduling tools supports more accurate forecasting and procurement.
Close coordination across departments ensures that inventory availability keeps pace with project progress.
Common Inventory Management Challenges in Construction & How to Solve Them
Inventory breakdowns create knock-on effects across cost, scheduling, and site productivity.
These issues are common in Australian commercial construction, where project complexity, variable lead times, and site constraints compound the risk. Solving them requires more than tools; it demands structured processes and cross-team accountability.
Below are the most frequent challenges and the steps experienced contractors take to address them.
1. Inaccurate inventory counts
Stock discrepancies are one of the most persistent issues in construction. They typically arise from manual tracking, inconsistent data entry, or unrecorded site-level purchases. Small errors accumulate quickly across multiple job sites, leading to overordering, missed deliveries, or inflated material costs.
To improve accuracy:
- Conduct weekly or fortnightly audits using structured digital checklists
- Replace spreadsheets with cloud-based platforms that sync data in real time
- Track usage daily through foremen reports, including damaged or missing items
- Standardise data entry protocols to ensure consistency across teams
2. Material theft and loss
Theft and misplacement of tools and materials continue to impact project margins. Items left unsecured at the end of the day, especially high-value tools and plant, are vulnerable to internal and external theft. There is often no clear tracking or check-in system, which limits recovery options and weakens accountability.
To reduce loss:
- Implement end-of-day security procedures using fenced storage and lockable containers.
- Tag tools and plant with GPS or RFID for real-time tracking and location alerts.
- Use geofencing to detect unauthorised movement of high-value items.
- Train all staff on theft prevention practices and reinforce personal responsibility.
3. Poor storage practices
Improper storage damages materials, increases site hazards, and causes delays when items cannot be located or used.
This issue often emerges from last-minute deliveries, lack of designated laydown areas, or poor weather protection. Storing items too early or in the wrong conditions reduces quality and creates unnecessary waste.
To improve storage outcomes:
- Assign dedicated storage zones based on material type and usage patterns.
- Schedule just-in-time deliveries for bulky or high-risk items to reduce exposure.
- Conduct regular inspections to check the condition, safety compliance, and organisation.
- Use temporary structures to shield sensitive materials from weather and contamination.
4. Delayed procurement and logistics issues
Procurement delays often stem from missed approvals, unclear specifications, or supplier constraints.
When lead times blow out or items arrive late, flow-on effects disrupt task sequencing and force costly workarounds. These delays are especially critical for structural components or materials tied to long-lead procurement.
To mitigate delays:
- Maintain a live procurement schedule linked to the construction program.
- Flag long lead time items early and initiate ordering during preconstruction.
- Use RFIs to confirm specifications before issuing purchase orders.
- Develop supplier redundancy by prequalifying multiple vendors for critical materials.
5. Insufficient forecasting and planning
Forecasting is often based on guesswork rather than historical data or project-specific needs. As scope changes or sequencing shifts, teams are forced into reactive purchasing that raises costs and reduces productivity.
To improve planning:
- Use data from past projects to forecast tool, equipment and PPE requirements.
- Keep a buffer stock of high-use items and use just-in-time supply for lower-risk categories.
- Conduct monthly planning reviews across site, warehouse and procurement leads.
- Build contingency ranges into material plans to absorb unexpected changes.
6. Lack of real-time visibility
When inventory data is out of date or stored in silos, teams lose the ability to plan and respond effectively. Miscommunication between the office, warehouse and site creates blind spots in ordering, stock levels, and usage. This often results in duplicate orders, idle crews, or unused stock on the wrong site.
To improve transparency:
- Use a cloud-based platform that centralises data across teams and locations.
- Give foremen and warehouse staff mobile access to track inventory on-site.
- Link material orders to job cost codes for more accurate reporting.
- Schedule weekly coordination meetings to align inventory planning across departments.
7. Disorganised inventory categorisation
Without a consistent structure, tracking what has been used, where it is stored, or how much remains becomes difficult. Mixing tools with materials or consumables creates inefficiencies, especially when multiple crews share resources across phases or locations.
To improve organisation:
- Categorise inventory by type, usage and value in all tracking systems.
- Label shelves, bins and containers with digital or physical identifiers.
- Use barcoding or RFID to standardise check-in and check-out processes.
- Assign stock to job numbers or work phases to streamline reporting and audits.
8. Untrained or underprepared staff
Even the best systems fail without proper execution. Inventory issues are often caused by unclear responsibilities, missed reporting, or poor site-level practices. These failures usually reflect a lack of training or supervision rather than deliberate error.
To improve capability:
- Train warehouse and site staff on inventory protocols during onboarding
- Require daily usage logs tied to site activity and task completion
- Define clear roles for ordering, tracking and reporting within the project team
- Monitor compliance monthly and address gaps through follow-up training or accountability measures
Utilising Construction Inventory Management Software
Inventory management software helps commercial contractors manage materials, tools, and equipment more effectively across multiple sites. Integrating into day-to-day operations improves visibility, reduces cost leakage, and supports more accurate planning and forecasting.
The right platform should align with your delivery model, team structure, and project size. Look for systems that include:
- Barcode scanning or RFID to streamline check-in, check-out and onsite tracking
- Cloud-based access to allow real-time updates from the site, warehouse and office
- Multi-location tracking using GPS or geofencing to monitor equipment movement
- System integration with scheduling, procurement and budgeting tools
- Automation of data entry, cost allocation and reporting
- Analytics and reporting to support forecasting, usage trends and risk identification
Contractors that embed inventory software into their workflows gain measurable improvements in both operational efficiency and financial performance. Here’s what that could look like:
- Automated tracking eliminates manual entry errors, leading to cleaner, more reliable data across sites.
- Faster ordering and approval processes save project managers and on-site teams time, reducing administrative overhead.
With access to historical usage patterns, teams can forecast demand more accurately and adjust procurement strategies proactively. This, in turn, helps prevent stockouts, avoid duplicate purchases, and reduce downtime, tightening overall cost control across the project.
Pro Tip
Adopting inventory software involves change across systems and people, which can cause friction. Avoid these common challenges by:
- Ensuring platforms integrate properly to prevent data silos
- Providing hands-on training to help site teams adopt new tools and workflows
- Allocating budget for licensing, onboarding, and any required process redesign
For contractors operating across multiple sites or project types, software provides the structure and visibility needed to manage inventory with greater confidence and control.
Strong construction inventory management reduces risk, improves forecasting, and protects margins
Effective inventory management gives Australian contractors greater control over materials, tools, and equipment across every delivery phase. By standardising processes, using the right technology, and addressing common failure points, teams can reduce delays, lower costs, and deliver projects with greater confidence.
Categories:
Tags:
Written by
Josh Krissansen
25 articles
Josh Krissansen is a freelance writer with two years of experience contributing to Procore's educational library. He specialises in transforming complex construction concepts into clear, actionable insights for professionals in the industry.
View profileExplore more helpful resources

Take 5 Safety: A Practical Layer in Construction Risk Management
Construction sites don’t run on plans alone. They run on people making decisions in unpredictable conditions — where one missed hazard can lead to serious injury, lost time, or legal...

Site Safety Plan: What It Is, WHS Requirements, and How to Create One That Works
For project leaders, a site safety plan is more than a compliance requirement. It is an operational blueprint for keeping people safe, work flowing, and projects protected from costly disruption....
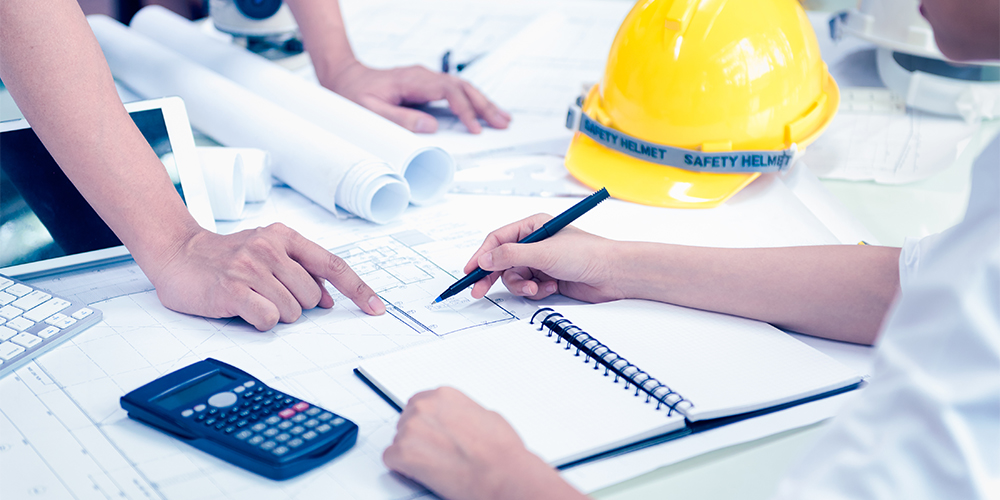
Construction ERP Explained: Why Builders Need a Unified System
As Australian construction projects grow in value and complexity, the pressure on operational teams is intensifying. Site supervisors, safety managers, and project engineers are expected to deliver precision execution—on tighter...
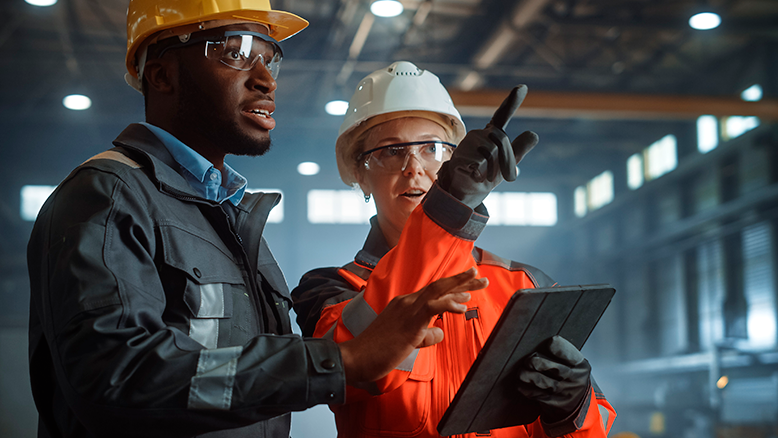
How to Prepare and Use a SWMS to Manage High-Risk Construction Work
On Australian job sites, Safe Work Method Statements (SWMS) are more than a legal requirement, they’re a critical part of delivering high-risk construction work without indecent, delay or regulatory exposure....